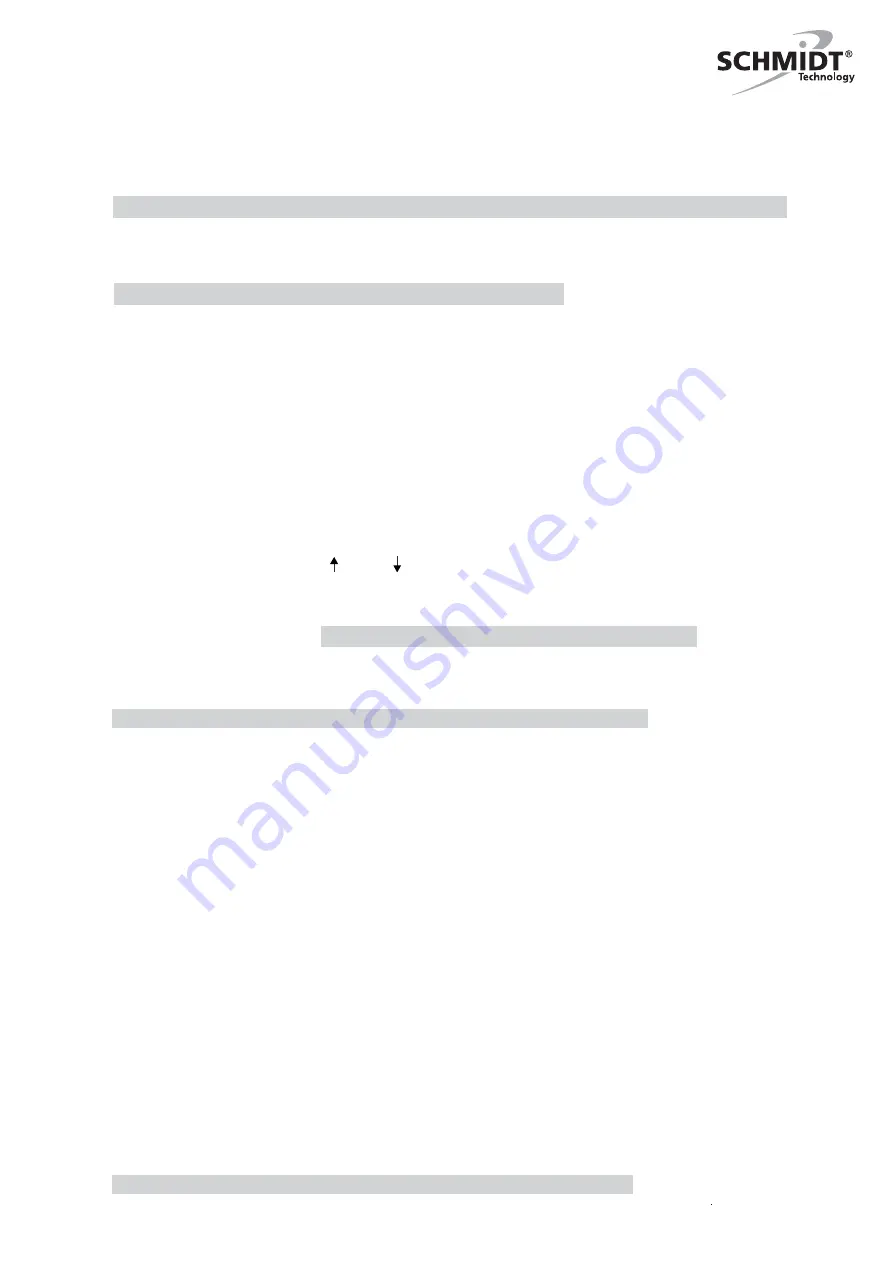
5
3.5 Return stroke lock (optional) Attention: Consider minimal stroke! See techn. data.
On delivery, the return stroke lock is adjusted ex work. adjustments afterwards are not possible because B.D.C.
is not allowed to be adjusted afterwards (ISO 9001 Quality Standard).
The stop bolt
(17)
is sliding when reaching the stroke reducer (toggle is fully straightened) over the
activating rim in the return stroke curve of the cam
(16)
.
Attention: If B.D.C.- position is not reached, return stroke remains blocked
.
No11/15
Block position I = 12.0mm before B.D.C., block position II = 1.5mm before B.D.C., release precision* 0.03 mm
No13
Block position I = 14.5mm before B.D.C., block position II = 1.5mm before B.D.C., release precision* 0.03 mm
No14/16
Block position I = 14.0mm before B.D.C., block position II = 1.5mm before B.D.C., release precision* 0.04 mm
No111
Block position I = 13.0mm before B.D.C., block position II = 4.5mm before B.D.C., release precision* 0.07 mm
*Minimum remainder stroke before BDC-limit for safe releasing of the return stroke lock
3. Setup instructions
3.3 Working stroke (return stroke) adjustment
(not valid for No.111 and 113 with fine adjustment and No.13)
(Round ram configuration, just for No.11, No.15, No.17 , No.111 and No. 113)
•
Unfasten ram stroke reducer
(12)
, adjust the necessary return stroke with the hand lever and fasten the
stroke reducer in the most upper position.
(Square ram configuration)
•
Unfasten by locking screw
(6)
the stroke reducer, adjust the necessary return stroke with the hand
lever, fasten stroke reducer in accordance to the requested position.
3.4 Fine adjustment of ram ± 1.5mm
(optional)
•
The fine adjustment is positioned to the middle ex work. In the middle position, the marking rim
(13)
on the ram shaft is even with the upper rim of the adjustment nut
(15).
(With square ram configuration "
V
", the marking rim on the ram adapter is in middle position of the
sight window.)
•
Unfasten set screw
(14).
•
Turn adjustment nut
(15)
right ( ) or left ( ). (Square rame configuration in opposite direction)
•
Retight set screw
(14 ).
•
Adjustment precision is 0.01mm. One gradiation mark = 0.02mm.
3.2 Setting of working height
•
Loosen head locking screws
(10)
.
•
Raise or lower head unit
(2)
via vertical adjustment
(9)
.
Important!
Lock head locking screws
(10)
before operation of press.
3.7 Adjustment of gibs (
Version
V)
The ground surfaces of the ram are guided via the teflon lined gibs
(4)
via factory set gib adjustment
screws
(5)
. The gibs are set for "play-free" operation.
•
Field adjustments are recommended from time to time via appropiate adjustment of adjustment screws
and nuts
(5)
.
3.6 Emergency release for return stroke lock
By pressing the emergency release button
(18)
the return stroke in locked positions I and II is released in
emergency sitations
3.1 Handlever
•
Mount handlever
(1)
to shaft and tighten it with a clamping screw.
The fastening torque is from 6 Nm till max. 10 Nm
Attention: The max.operating force at the handlever is 200 N (is not allowed to be exceeded)
3.8 Cleaning of Ram
•
The ram needs to be cleaned from time to time with a slightly oiled cloth.
•
In any case do not use any solvent based cleaners, in order to avoid any dry running condition of the ram.
3.9 Max. weights for upper tools mounted at the press ram
By using reinforced springs the max. tool weight can be increased.
Such reinforced springs are available as special equipment and marked in red.
Press
Standard
Special execution
13 / 113
~ 0 - 0.6 kg
~ 0.6 - 2 kg
11/15/14/16
~ 0 - 1.2 kg
~ 1.2 - 6 kg
17/ 111
~ 0 - 1.5 kg
Attention: Reinforced springs are not allowed to be used with light tools.