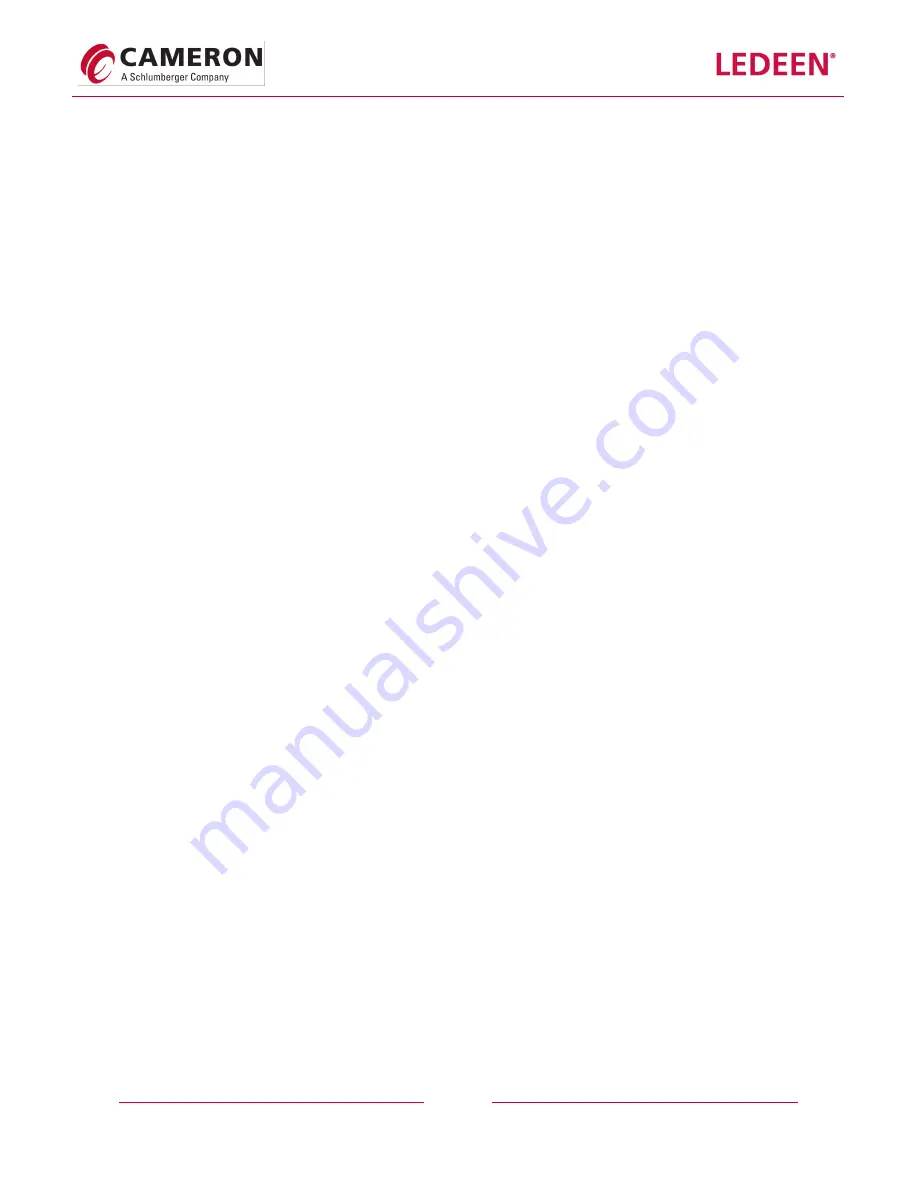
39
Note
: If the actuator is VA0 model, the cylinder head flange (item 25) is integrated with frame.
1.
Place the frame assembly (item 10) on a suitable work bench in vertical orientation.
2.
Locate the head flange (item 25) external (item 39) and internal seals (item 26) and carefully place it in
its grooves.
(If VA1 models only)
3.
Locate the four no’s of hexagonal socket head screws (item 27) with seal washers (item 52). Assemble
the head flange by threading the screws into the frame and through the piston rod.
(If VA1 models only)
4.
Locate the piston (item 42). Install the piston seal (item 28) and guide slider (item 41) into the piston.
5.
Locate the piston rod seal (item 29) and install in to the piston rod (item 5).
6.
Locate the piston assembly and gradually install it by using the hexagonal screw (item 30) and washer
(item 31) into the piston rod (item 5).
Note
: While Install the piston rod in the piston apply Loctite 243 for thread fixing.
7.
Locate the liner (item 43). Slide the liner over the piston seal and the head flange seal (item 39) without
damaging the seals.
8.
Locate the tie rods (item 40) and mount them by using hexagonal screw (item 37) and pins (item 38)
into head flange.
9.
If the actuator is spring return locate the spring (item 53*) into the groove of the piston.
10.
Locate the end flange (item 32) and install the seal (item 44) into the end flange groove.
11.
Locate the end flange (item 32) and install the end stop adjustment of screw (item 36), circlip (item 33),
seal (item 34) and hex nut (item 35) into the end flange. Lightly grease the threads on the end flange
where screw (item 36) is going to be assembled.
(Refer to figure 1 on page no. 32 for exploded view)
12.
Locate the end flange assembly and slowly lower it into the cylinder liner and in the tie rods. Ensure the
air supply ports are properly oriented with the air supply ports on the head flange.
Warning:
While closing the cylinder end flange assembly the spring gets preloaded. (If SR Actuator)
13.
Slowly pre-install the screws (item 45) into the tie rods (item 40) in the proper sequence, then threading
the same screws with their washers (item 46) and tighten to secure the end flange.
14.
Set the stroke required by the actuator. rotating the mechanical stop (item 36) clockwise reduces the
angular stroke and rotating it counter-clockwise increases the angular stroke.
15.
Adjust the nut (item 35) and seal (item 34) its grooves by applying grease film. (Suggested grease:
Parker super-o-lube or equivalent) (applying 45-50 Nm torque)
16.
Reassembly of the cylinder assembly is now complete.
17.
Place the actuator assembly in a horizontal orientation with the actuator frame resting on its base.
18.
Locate the frame gasket (item 19) and frame cover (item 23).
Содержание CAMERON LEDEEN VA Series
Страница 4: ...3 NOTES ...
Страница 14: ...13 LIFTING DEVICES MAXIMUM WORKLOAD Chains ...
Страница 15: ...14 LIFTING DEVICES MAXIMUM WORKLOAD Slings ...
Страница 16: ...15 ...
Страница 17: ...16 ...
Страница 27: ...26 Figure 1 VA0 MODEL HEAD FLANGE INTEGRATED WITH FRAME Figure 2 ...