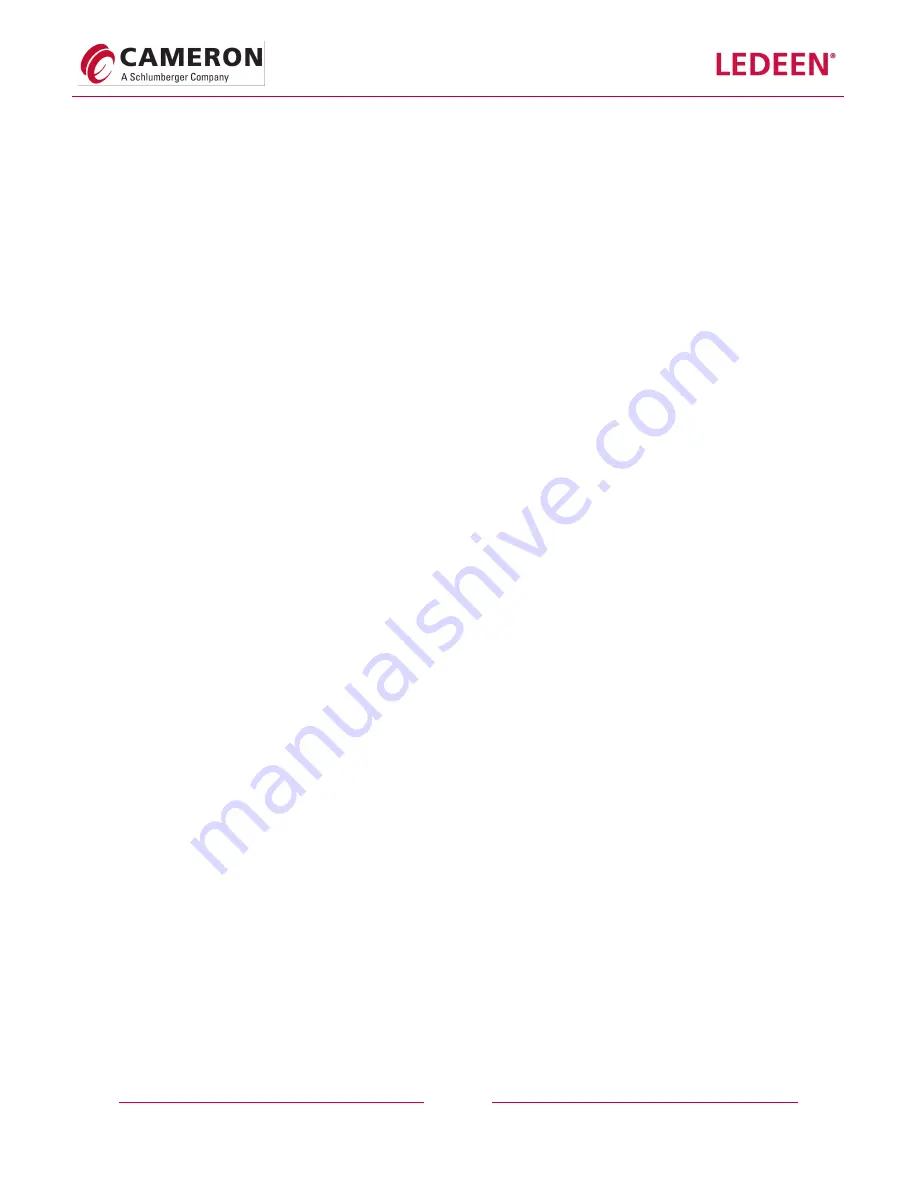
2
PREFACE
The procedures included in this book are to be performed in conjunction with the requirements and
recommendations outlined in API Specifications. Any repairs to the equipment covered by this book should be
done by an authorized Cameron service representative. Cameron will not be responsible for loss or expense
resulting from any failure of equipment or any damage to any property or death or injury to any person resulting
in whole or in part from repairs performed by anyone other than authorized Cameron personnel. Such
unauthorized repairs shall also serve to terminate any contractual or other warranty, if any, on the equipment
and may also result in equipment no longer meeting applicable requirements.
File copies of this manual are maintained. Revisions and/or additions will be made as deemed necessary by
Cameron. The drawings in this book are not drawn to scale, but the dimensions shown are accurate.
This book covers Cameron products.
Cameron, a Schlumberger Company
Ledeen Facility
Via L. Gandini 4
27058 Voghera (PV) – Italy
cameron.slb.com
Содержание CAMERON LEDEEN VA Series
Страница 4: ...3 NOTES ...
Страница 14: ...13 LIFTING DEVICES MAXIMUM WORKLOAD Chains ...
Страница 15: ...14 LIFTING DEVICES MAXIMUM WORKLOAD Slings ...
Страница 16: ...15 ...
Страница 17: ...16 ...
Страница 27: ...26 Figure 1 VA0 MODEL HEAD FLANGE INTEGRATED WITH FRAME Figure 2 ...