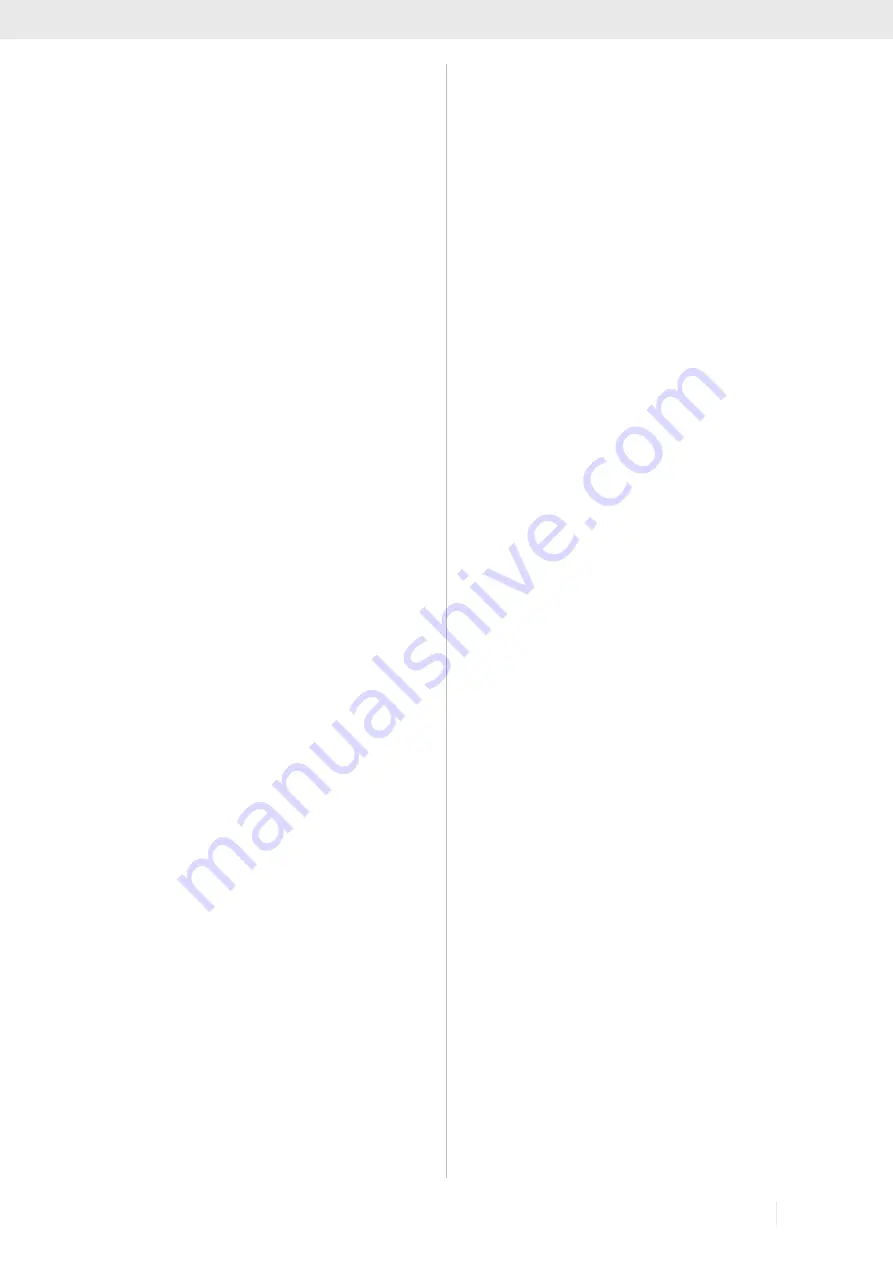
37
GB/IE/NI
• Select the suitable scale according to whether the stop rail
(30) has been turned around for working with thick or thin
material: High stop rail (thick material) (Fig. 22); Low stop
rail (thin material) (Fig. 24).
• Adjust the parallel stop (14) to the desired dimension on the
inspection glass and use the eccentric lever to fix in place for
the parallel stop (13).
Adjusting the Stop Length (Fig. Z)
• In order to prevent the material being cut from jamming, the
stop rail (30) can be moved in the longitudinal direction.
• Rule of thumb: the rear end of the stop abuts on an imagi-
nary line. This begins at about the middle of the saw blade
and runs towards the back at an angle of 45°.
• Adjust the required cutting width.
• Release the knurled nuts (m) and push the stop rail (30) for-
ward until the imaginary 45° line is touched.
• Tighten the knurled nuts (m) again.
Adjusting the Parallel Stop (Fig. X,Y, AA)
• Caution! Remove the guard.
• Adjust the saw blade (4) to the maximum cutting depth.
• Adjust the parallel stop (14) such that the stop rail (30)
touches the saw blade (adjustment for thick material).
• If the parallel stop (14) is not parallel to the saw blade(4)
please proceed as follows. Release the screws (r) on the par-
allel stop until the parallel stop (14) can be aligned to be
parallel with the saw blade(4).
• Retighten the screws (r).
Transverse stop (Fig. AB)
• When the wood is being cut to size, the transverse stop (31)
must be extended with the stop rail (30) of the parallel stop
(14).
• Push the transverse stop (31) into a groove (28) of the saw
table.
• Loosen the knurled screw (29).
• Turn the transverse stop (31) until the desired angle is set.
The notch on the guide bar shows the angle that has been
set.
• Retighten the knurled screw (29).
• To extend the lateral end stop (31) with the end stop rail
(30), the end stop rail (30) must be removed from the paral-
lel end stop (14). Now the stop rail has to be mounted as
shown in Figure AB; use the knurled nuts (m) for this purpose..
Caution!
• Do not push the stop rail (30) too far in the direction of the
saw blade.
• The distance between the stop rail (30) and saw blade (4)
should be approximately 2 cm.
Adjusting the scale of the parallel stop (Fig. AC)
• Check whether the display on the sight glass (p) of the par-
allel stop (14) shows the correct values with respect to the
cutting line. If this is not the case, please proceed as follows:
• Release the screw (q) with which the display on the sight
glass (p) of the parallel stop (14) is attached. The sight glass
(p) display can now be set to the correct position.
• Now, retighten screw (q) on the sight glass (p).
12. Use
m
Working Instructions
After each new adjustment, we recommend a trial cut in order
to check the set dimensions. After the saw has been switched
on, wait until the saw blade has reached its maximum speed
before you carry out the cut.
Secure long workpieces against tilting at the end of the cutting
process (e.g. unwinding stand etc.)
Caution with incision cutting.
Operate the device only with a suction system. Check and
clean the suction channels regularly.
Suitability of the saw blades:
• 24 teeth: soft materials, high chip removal, rough cut image
• 48 teeth (not included in the scope of delivery): hard materi-
als, lower chip removal, iner cut image
Performing Longitudinal Cuts (Fig. AD)
Here, a workpiece is cut in its longitudinal direction.
One edge of the workpiece is pressed against the parallel stop
(14) while the lat side lies on the saw table (1).
The saw blade guard (2) must always be lowered onto the
workpiece.
The working position during longitudinal cutting must never be
in a straight line with the cutting line.
• Adjust the parallel stop (14) according to the workpiece
height and the desired width.
• Switch on the saw
• Place your hands with the ingers closed together lat on the
workpiece and push the workpiece along the parallel stop
(14) into the saw blade (4).
• Guide from the side with your left or right hand (depending
on the position of the parallel stop) only up to the front edge
of the saw blade guard (2).
• Always push the workpiece through to the end of the riving
knife (3).
• The cutting waste remains on the saw table (1) until the saw
blade (4) is back in its resting position.
• Secure long workpieces against tilting at the end of the cut-
ting process! (e.g. unwinding stand etc.)
Cutting narrow Workpieces
Longitudinal cuts of workpieces with a width of less than 120
mm always have to be cut with the help of a push stick (17).
The push stick is included in the scope of delivery. Replace a
worn or damaged push immediately.
• Adjust the parallel stop according to the planned workpiece
width.
• Advance the workpiece with both hands, making sure that
you use a push stick (17) as a pushing aid in the vicinity of
the saw blade.
• Always push the workpiece through to the end of the riving
knife.
m
Caution!
In the case of short workpieces, the push stick
should be used from the beginning of the cutting process.
Содержание 313795
Страница 6: ...U V 30 14 A 1 1 5 W B 2 1 X 15 m m 14 30 14 B 1 2 Y A 1 2 A 45 Z p 15 13 m m 14 30...
Страница 7: ...A 1 2 AE A 1 2 AF 2 17 14 14 AA AB 30 r A 2 1 AC A 1 2 AD m m 29 14 p 13 30 31 28 q 2 14 1...
Страница 8: ...AG A 1 2 AH 4 AI AJ 14 28a 31 32 28b...
Страница 76: ...68...
Страница 79: ......