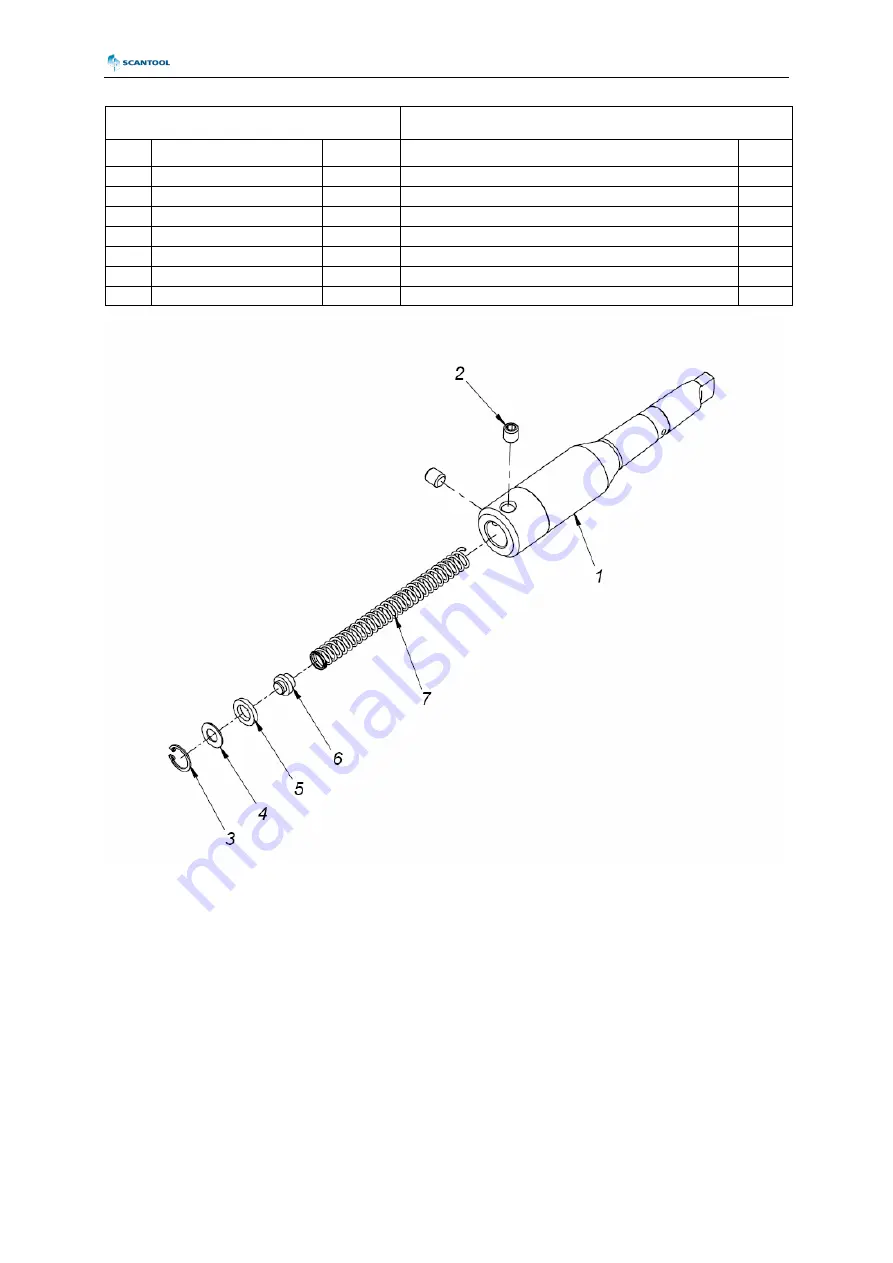
COMPACT 75
COMPACT 75
Operator’s manual for drilling machine
- 36 -
UCW-0173-00-00-00-0
ARBOR ASSY AMT3-U19/3-3
ITEM
PART NUMBER
VERSION
DESCRIPTION
Q-TY
10.1 KRP-0173-00-01-00-0
ARBOR BODY
1
10.2 WKR-000032
HEX SET SCREW-M10X10
2
10.3 PRS-000009
INTERNAL RETAINING RING 19W
1
10.4 PDK-0139-00-04-00-0
WASHER D=18,8x10x1
1
10.5 USZ-0140-05-04-00-0
SEAL
1
10.6 WYP-0154-00-02-00-0
PLUNGER
1
10.7 SPR-0154-00-03-00-0
SPRING 1,6x12,4x159
1
Содержание COMPACT 75
Страница 19: ...COMPACT 75 COMPACT 75 Operator s manual for drilling machine 19 ...
Страница 26: ...COMPACT 75 COMPACT 75 Operator s manual for drilling machine 26 10 ELECTRICAL DIAGRAM COMPACT 75 ...
Страница 28: ...COMPACT 75 COMPACT 75 Operator s manual for drilling machine 28 ...
Страница 32: ...COMPACT 75 COMPACT 75 Operator s manual for drilling machine 32 ...