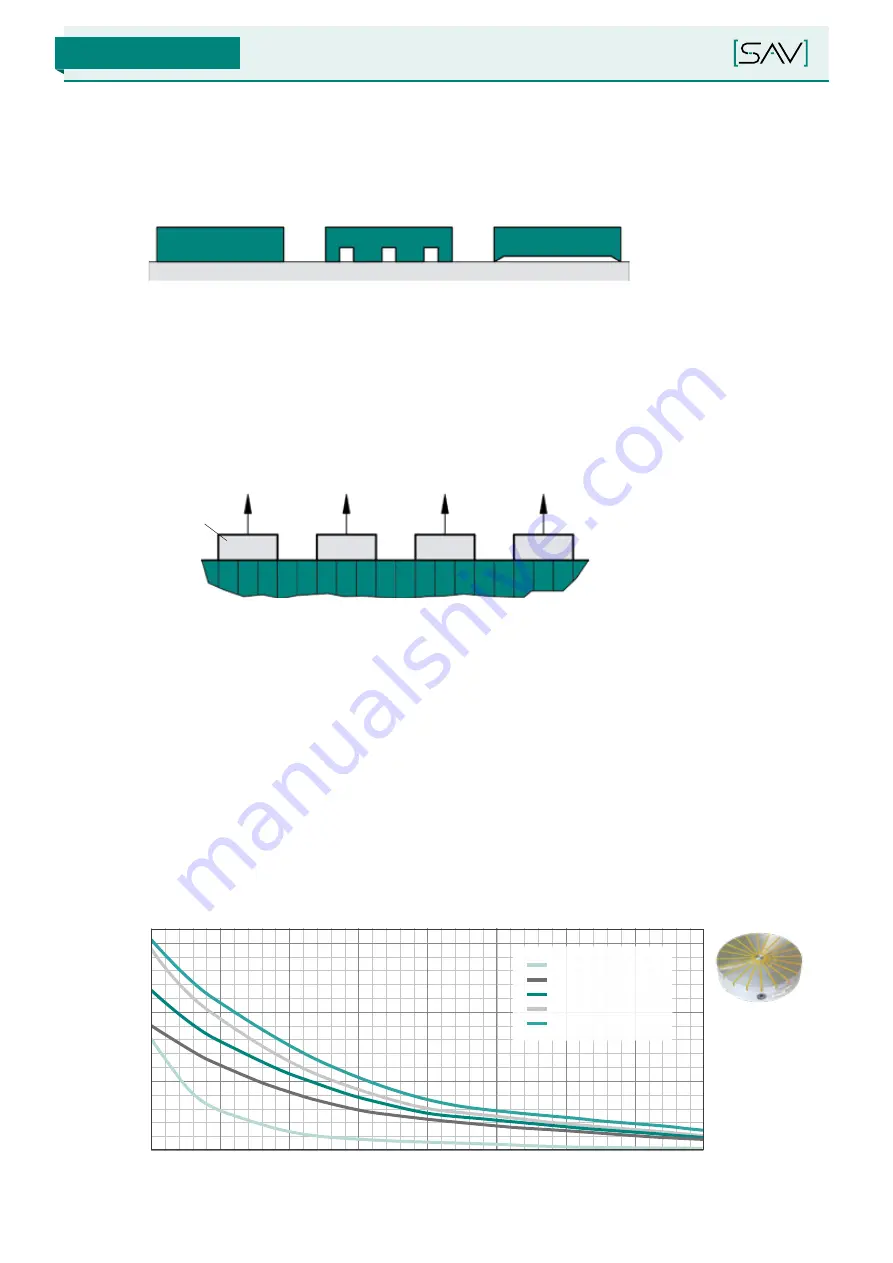
Version 1.0
[
42
]
SAV 244 .01 / .03 / .06 /
.07 / .10 / .11
3. TECHNICAL SPECIFICATIONS
Holding force and contact area
The contact area is the area of the workpiece which actually touches the magnet surface.
continuous contact
interrupted contact
linear contact
100 %
60 %
15 %
Fig. 5: Rough illustration of holding force reduced by unfavourable workpiece shapes
Holding force and surface quality
Surface quality is very important for the holding force of a workpiece as it rapidly decreases with increasing
roughness. The best values are achieved with a finely polished surface without air gap.
workpieces
magnet
Holding forces perpendicular to the magnet:
20 % – 50 %
50 % – 70 %
70 % – 80 %
80 % – 90 %
R
a
1.6
R
a
3.2
ROUGH
R
a
0.8
Fig. 6: Influence of the workpiece surface on the achievable holding forces (R
a
= calculated mean roughness value)
Holding force and air gap
Air gaps cannot always be avoided on workpieces. The can be created, for example, during upstream processes,
due to cavities and uneven areas on cast parts, roughness from machining, paint layers and non-magnetic surface
layers. As air has a very high magnetic resistance, only few field lines can be generated with larger gaps and the
holding forces decrease rapidly, as shown in the diagram as an example.
The air gap sensitivity is largely dependent on the workpiece size relative to the magnet size, on the material
composition and on the pole pitch of the magnet. It can be generally stated that magnet systems with a larger
primary pole pitch have a better bridging capacity. Compared to electro-permanent magnets, deeper magnetic
fields and therefore greater resistance can be achieved with electromagnets.
SAV 244.06
radial pole pitch
air gap in mm
ho
ld
ing f
or
ce i
n N
/c
m
2
0
150
100
50
0
0.1
0.2
0.4
0.5
0.6
0.7
0.8
0.3
D = 100 mm
D = 130 / 150 mm
D = 200 / 250 mm
D = 300 / 350 mm
D = 400 / 500 mm
Содержание 244.01
Страница 55: ......