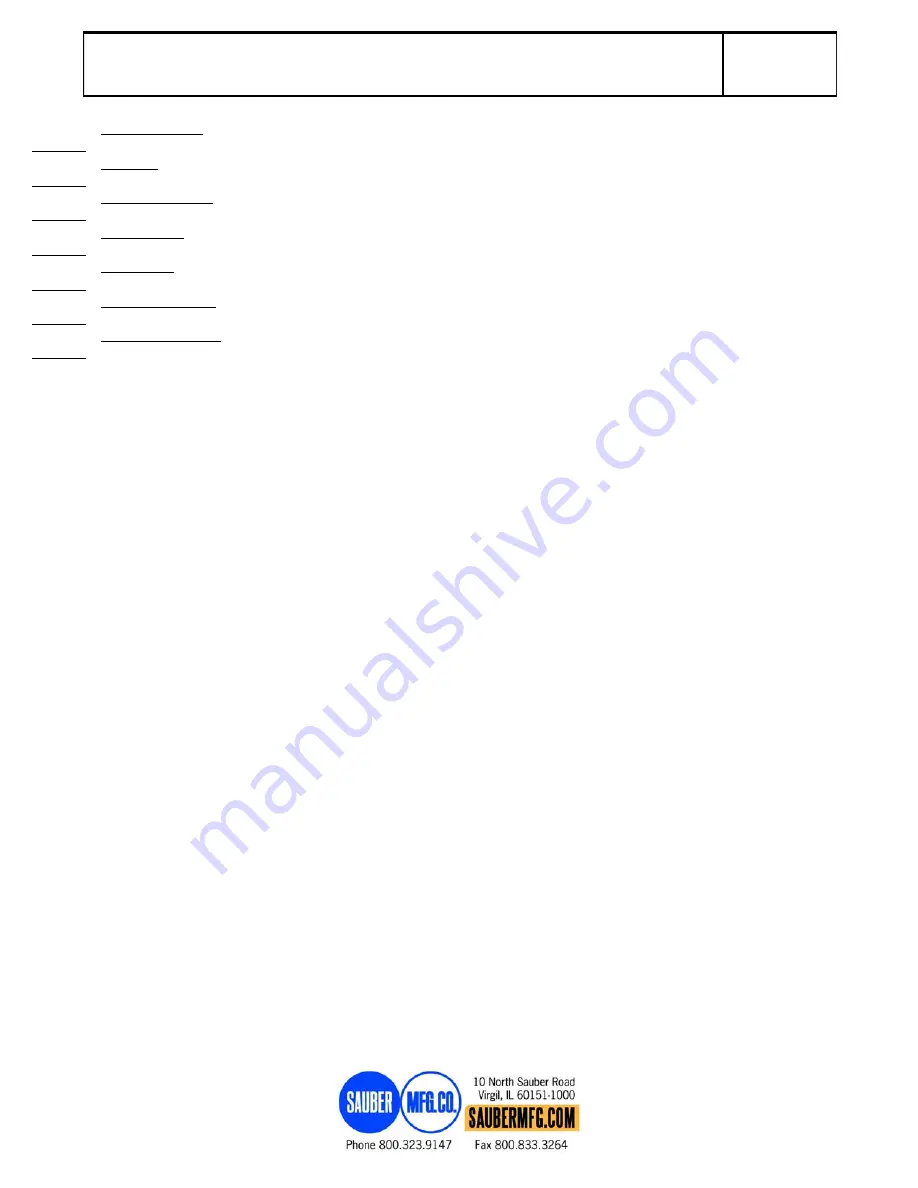
* Quick Couplers
Tighten or replace as necessary; try dripless fittings if problem persists
* Tank Lid
Remove tank lid and re-seal w/ new gasket and gasket compound
* Engine Mounting
Remove tank lid and engine and re-seal w/ gasket compound
* Sight Gauge
Remove sight gauge and replace O-rings or entire gauge
* Tank Drain
Tighten drain plug
* Return Line Filter
Tighten or replace filter
* Pressure Manifold
Remove cover and tighten fittings or replace O-rings
Oil Filtration
Keeping the oil clean in your power source is one of the best precautions you can take to ensure maximum system life.
There are three components to the filtration system. The sump strainer, located inside the tank, filters large particles introduced
into the tank. The return line filter is located outside the tank. This filter has a back pressure gauge that shows relative filter ef-
fectiveness. As the filter becomes dirty and clogged, the dial will move into the red area of the gauge. This signals that a filter
change is required. The third element of the filtration system is the fill/breather element. This filter is designed to keep large
scale impurities from entering the tank during fill operations. Hydraulic oil works at peak performance when it is pure. Therefore
change the oil and flush the tank if water or impurities inadvertently enter the system. A drain plug is provided at the base of
the tank. Always change the return line filter with the hydraulic oil.
Oil Level/Temperature Gauge
At the power source side a sight gauge has been installed. This gauge shows the level of hydraulic fluid in the tank, its
temperature and visual condition. Look for signs of impurities or water (cloudiness) in the glass. If found, refer to the oil filtration
section above. On level ground, the optimal oil level is 1" from the top of the sight gauge. Over-filling the tank will result in leak-
age through the tank/lid seal. Low oil levels will cause increased system heat and may "starve" the pump resulting in loss of flow
and pressure. Check the temperature gauge periodically during use. Hydraulic oil temperatures should not exceed 250 degrees
Fahrenheit. If this temperature level is encountered, we recommend an optional oil cooler for your system.
Pressure Gauge & Control
Your unit is equipped with a gauge that indicates operating pressure in pounds per square inch (PSI). While in opera-
tion, the system pressure gauge will indicate pressures between 50 PSI and the maximum pump pressure shown in the Com-
ponents Sourcing Information section. The system pressure should correlate to the amount of work being done by the tool in
use. If it appears that this relationship is not true, check for restrictions in the line or excessive heat build-up.
The maximum system pressure can be controlled by changing the relief setting at the side of the power source. Turn the
relief screw counterclockwise to lower the relief setting. Rotating it clockwise will raise the relief setting. Always make certain
the relief setting is set at least 100 PSI below the engine stall level. Many tools, including our Retrievers have their own internal
relief. The lowest relief setting in the system will prevail. Set the power source relief at the maximum level unless you wish to
limit maximum tool power or your tool does not have internal relief.
If the power source will not produce its rated pressure, check other reliefs in the system. Also check for blockage
between the pump and the pressure manifold/gauge. In order to produce maximum pressure, the engine must be running at top
performance. Any reduction in engine horsepower will reduce system pressure and/or flow. If engine performance is satisfact-
ory, check the pump output.
Hour Meter
Your system is equipped with an hour meter. Use this meter to track service intervals shown in maintenance section.
Operation & Maintenance Manual
Model 1570-B Puller
09/2010
Page 16