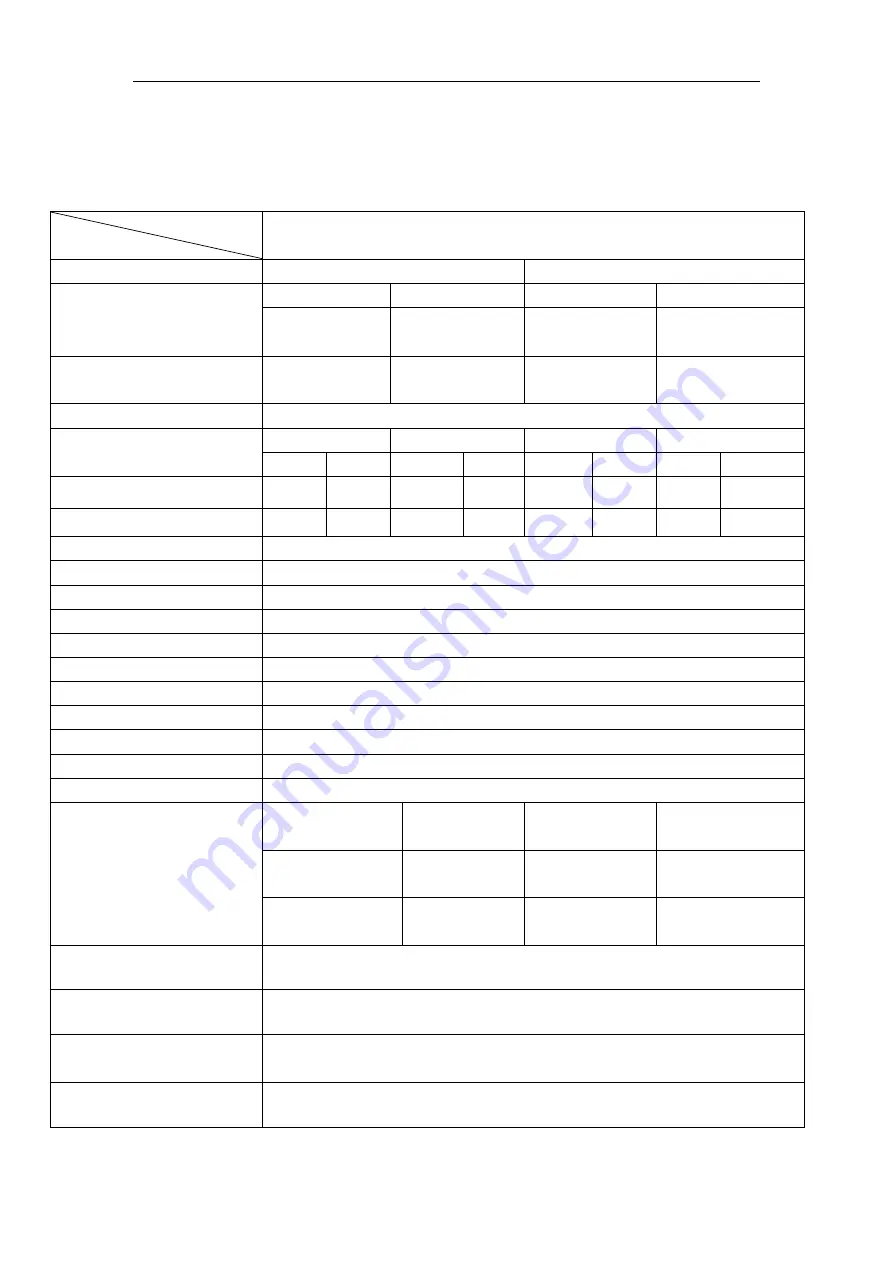
INSTALLATION AND ADJUSTMENT
9
§3 Installation and Adjustment
§3.1 Parameters
model
Parameters
SANARG 180AP
Rated input voltage
(
V
)
1~120V±10%
,
50Hz
1~240V±10%
,
50Hz
Rated input current
(
A
)
TIG
MMA
TIG
MMA
27.8(AC)
26.6(DC)
29.2(AC)
27(DC)
21.7(AC)
21.4(DC)
25(AC)
23(DC)
Rated input power
(
KW
)
3.7(AC)
3.4(DC)
3.7(AC)
3.4(DC)
5.0(AC)
4.7 (DC)
5.8(AC)
5.3(DC)
No load voltage(V)
45(52)
Welding current adjust range
(
A
)
TIG
MMA
TIG
MMA
AC
DC
AC
DC
AC
DC
AC
DC
Start Current Range
(
A
)
10
~
140
5
~
140
10
~
100
5
~
100
10
~
200
5
~
200
10
~
170
5
~
170
Crater Current Range
(
A
)
10
~
140
5
~
140
10
~
100
5
~
100
10
~
200
5
~
200
10
~
170
5
~
170
Up Slope Time(S)
0
~
10
Down Slope Time(S)
0
~
10
Pre Flow(S)
0.1
~
10
Post Flow(S)
1
~
10
Pulse Frequency(Hz)
0.5
~
200
Pulse Width Range
(
%
)
5
~
100
AC Frequency
(
Hz
)
50
~
250
Clearance Effect
(
%
)
15
~
50
Are Force
0
~
10
Hot Start
0
~
10
Are Length
0
~
10
Duty Cycle
(
40
℃
10min
)
40% 140A
DC 35% 100A
AC 40% 100A
DC 25% 200A
AC 30% 200A
DC 30% 170A
AC 35% 170A
60% 110A
DC 60% 75A
AC 60% 80A
DC 60% 130A
AC 60% 140A
DC 60% 120A
AC 60% 130A
100% 85A
100% 60A
DC 100% 100A
AC 100% 110A
DC 100% 90A
AC 100% 110A
Protection class
IP23
Insulation class
F
Machine
figure
size
(
length
×width× height
)
450*170*270
Net Weight(Kg)
11.2