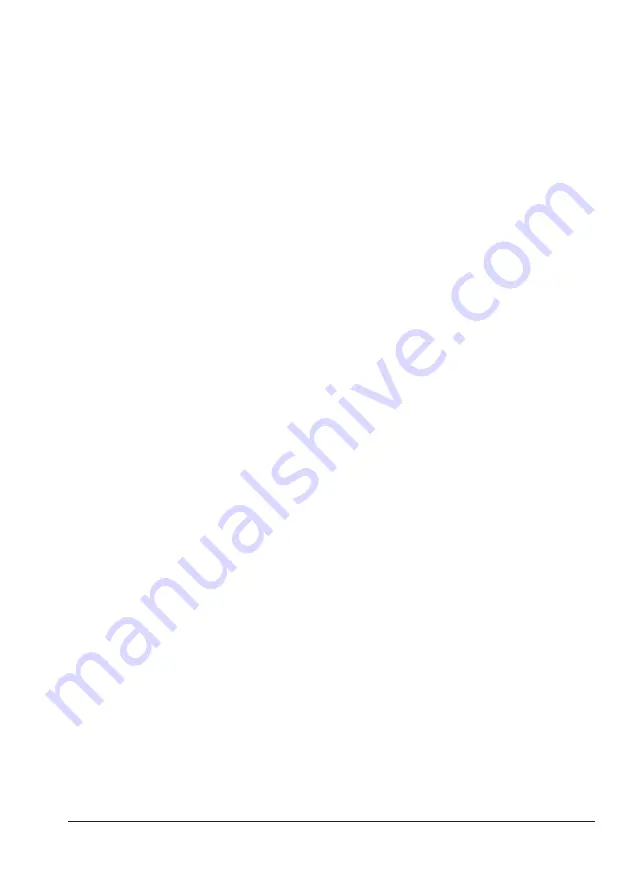
EB 8048-2/-3 EN
43
Servicing
7.4
Preparation for return ship
-
ment
Defective valves can be returned to
SAMSON for repair.
Proceed as follows to return valves to
SAMSON:
1. Put the control valve out of operation (see
section 9).
2. Decontaminate the valve. Remove any
residual process medium.
3. Fill in the Declaration on Contamination,
which can be downloaded from our
website at
u
> Check lists for after sales service >
Declaration on Contamination.
4. Send the valve together with the filled-in
form to your nearest SAMSON subsidi-
ary. SAMSON subsidiaries are listed on
our website at
u
7.5
Ordering spare parts and
operating supplies
Contact your nearest SAMSON subsidiary
or the SAMSON After-sales Service depart-
ment for information on spare parts, lubri-
cants, and tools.
Spare parts
Details on spare parts are available on re-
quest.
Lubricant
Details on suitable lubricants can be found in
the document
u
Tools
Details on suitable tools can be found in the
document
u
Содержание EB 8048-3
Страница 25: ...EB 8048 2 3 EN 25...
Страница 54: ...54 EB 8048 2 3 EN...
Страница 55: ...EB 8048 2 3 EN 55...