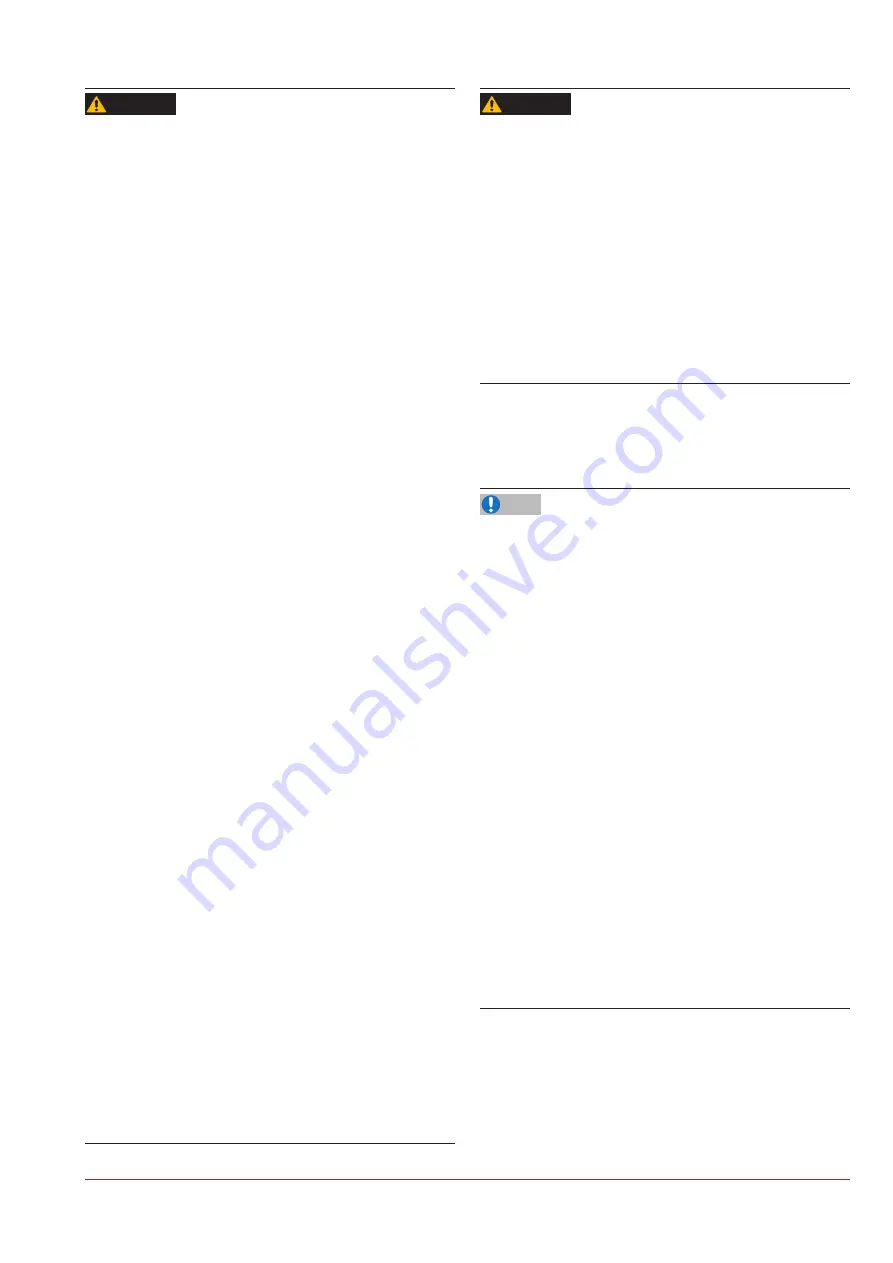
1-3
EB 01a_EN
March 2023 edition
Subject to technical changes
Safety instructions and safety measures
Danger of crushing due to moving parts!
The valve contains moving parts (actuator and plug stem) that
can lead to crushing if reaching into it.
Ö
Do not reach into the yoke during operation.
Ö
When working on the valve, interrupt and lock pneumatic en-
ergy and the control signal.
Danger of injury during the switching operation if performing
test runs on valves not installed in the pipe!
Ö
Do not reach into the valve. This can result in serious injuries.
Danger of injury due to venting the actuator!
During operation, when regulating or opening and closing the
valve, the actuator can be ventilated.
Ö
Install the valve such that the actuator does not ventilate at
eye level.
Ö
Use suitable silencers and plugs.
Ö
Wear eye protection and, if necessary, hearing protection
when working near the valve.
Danger of injury due to prestressed springs!
Valves that are equipped with preloaded actuator springs are un-
der mechanical tension. These valves, in combination with the
pneumatic SAMSON actuators, can be identi
fi
ed by the elon-
gated screws on the bottom of the actuator.
Ö
Before working on the actuator, release the compression from
the preloaded springs, see the corresponding actuator docu-
mentation.
Danger of injury due to residual medium in the valve!
When a valve must be removed from a pipe, medium can escape
from the pipe or the valve.
Ö
In the case of media that is harmful to health or hazardous,
the pipe must be completely emptied before a valve can be
removed.
Ö
Pay attention to the after
fl
ow of residuals or residuals that re-
main in dead spots.
Danger of injury due to the releasing of body screw connec-
tions!
If the body screw connections must be released, medium can es-
cape from the valve.
Ö
The screw connections on the connection of the body and
bonnet
fl
ange may only be released or loosened after the
valve has been removed.
Ö
During reassembly, tighten the screws according to Table
15-1 in Chapter “15.1.1 Tightening torques“ using a torque
wrench.
Dangers due to use as an end
fi
tting!
During normal operation, in particular with gaseous, hot and/or
hazardous media, spraying medium can cause hazards. It must
be kept in mind that the media is usually hazardous!
Ö
A blind
fl
ange must be assembled on the free connecting
pieces or the valve must be secured against unauthorized ac-
tuation.
Ö
If a valve used as an end
fi
tting in a pressurised line is
opened, this may only be done with extreme caution so that
the escaping medium does not cause any damage.
WARNING
Deviation of the breakaway and actuating forces due to
non-actuation of the valve!
Depending on the period of time of non-actuation, the breakway
and actuation forces can deviate considerably from the actuating
power data in the data sheet.
It is recommended to actuate the valve at regular intervals.
Ö
In consideration of the design, actuation must take place dur-
ing the year.
Ö
Indicate the duration of non-actuation when making an en-
quiry, so that this condition is taken into consideration in the
actuator design.
Ö
In the case of retro
fi
tted actuators by the operator, the correct
actuator design as regards the duration of non-actuation is
no longer the responsibility of PFEIFFER.
1.3 Notes regarding possible property
damage
Damage to the valve due to contamination!
Contamination (e.g. solid particles) in the pipes can damage the
valve.
Ö
The plant operator is responsible for cleaning the pipes in the
plant.
Ö
Rinse the pipes prior to commissioning.
Ö
Observe the maximum permissible pressure the valve and
plant.
Damage to the valve due to unsuitable medium properties!
The valve is designed for a medium with certain properties.
Other media can damage the valve.
Ö
Only use a medium that corresponds to the design criteria.
Damage to the valve and leakage due to excessively high or
low tightening torques!
The valve components must be tightened with speci
fi
c torques.
Deviating torques can lead to valve leakage or damage.
Ö
Excessively tightened components are subject to increased
wear.
Ö
Insuf
fi
ciently tightened components can cause leakage.
Ö
Observe the tightening torques, see Table 15-1 in Chapter
“15.1.1 Tightening torques”.
Damage to the valve due to unsuitable tools!
Unsuitable tools can damage the valve.
Ö
Suitable tools are required to work on the valve, see Chapter
“15.1.3 Tools”.
WARNING
NOTE
Содержание EB 01a
Страница 30: ...4 4 EB 01a_EN March 2023 edition Subject to technical changes Shipment and on site transport...
Страница 36: ...6 2 EB 01a_EN March 2023 edition Subject to technical changes Start up...
Страница 38: ...7 2 EB 01a_EN March 2023 edition Subject to technical changes Operation...
Страница 42: ...8 4 EB 01a_EN March 2023 edition Subject to technical changes Malfunction...
Страница 46: ...10 2 EB 01a_EN March 2023 edition Subject to technical changes Decommissioning...
Страница 48: ...11 2 EB 01a_EN March 2023 edition Subject to technical changes Removal...
Страница 54: ...13 2 EB 01a_EN March 2023 edition Subject to technical changes Disposal...
Страница 56: ...14 2 EB 01a_EN March 2023 edition Subject to technical changes Certificates...
Страница 57: ...14 3 EB 01a_EN March 2023 edition Subject to technical changes Certificates...
Страница 58: ...14 4 EB 01a_EN March 2023 edition Subject to technical changes Certificates...
Страница 59: ...14 5 EB 01a_EN March 2023 edition Subject to technical changes Certificates...
Страница 60: ...14 6 EB 01a_EN March 2023 edition Subject to technical changes Certificates...
Страница 75: ...EB 01a_EN March 2023 edition Subject to technical changes...