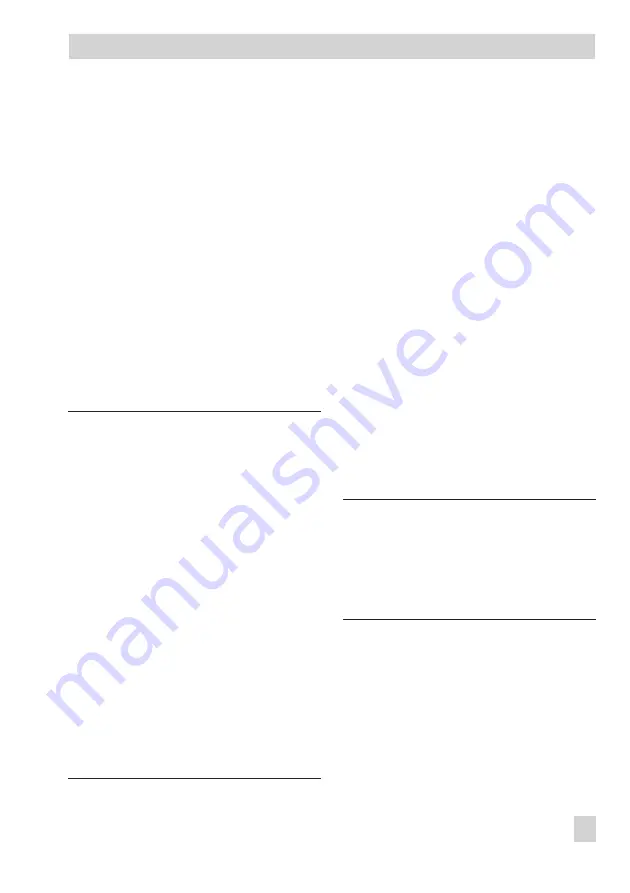
Connection
4
For electropneumatic positioners, con-
nect an ammeter to ter11
and –12.
4
For pneumatic positioners, connect con-
trol signal input (Input 27) to a com-
pressed air source providing
max. 1.4 bar using a pressure trans-
ducer and pressure gauge.
4
Apply compressed air to the supply input
(Supply 9).
4.2 Adjustment
4.2.1 Spring-return actuator: valve
CLOSED without supply air
Important!
To ensure that the full closing force can be
effective in the control valve, the actuator
must be completely vented when either the
lower (direct operating direction) or upper
(reverse operating direction) range value of
the reference variable is reached.
As a result, set the input signal to a slightly
higher starting point of 4.5 mA (0.225 bar)
for direct operating direction and to a
slightly lower starting point of 19.5 mA
(0.975 bar) for reverse operating direction.
This applies in particular to controllers and
control systems whose output signal is lim-
ited to 4 to 20 mA.
For electropneumatic positioners with
tight-closing function, the starting point and
upper range value can be set to 4 or
20 mA. The activation/deactivation function
ensures that the valve's closed position is
reached.
Example:
With direct operating direction, the control
valve is expected to travel through an angle
of rotation of 90° (90° cam disc must be in-
stalled) with a reference variable of 4 to
20 mA (0.2 to 1 bar).
The valve opens when the reference variable
increases.
Starting point (zero)
4 mA (0.2 bar)
1. Set input signal to 4.5 mA using the am-
meter or set the pressure adjuster to
0.225 bar.
2. Turn zero adjuster (3) until the closure
member of the valve just starts to move
from its rest position.
3. Switch off the input signal and slowly in-
crease it again. Check whether the clo-
sure member starts to move at 4.5 mA
(0.225 bar).
4. Correct any deviations by turning the
zero adjuster (3).
Note on adjustment with reverse operating
direction
With reverse operating direction (Fig. 5, top
right), set the starting point (valve CLOSED)
to 20 mA (1 bar). The upper range value
(valve OPEN) will then be 4 mA (0.2 bar)
EB 8386 EN
17
Operation – Adjustment
Содержание 3761
Страница 23: ...EB 8386 EN 23...
Страница 24: ...24 EB 8386 EN...
Страница 25: ...EB 8386 EN 25...
Страница 26: ...26 EB 8386 EN...
Страница 27: ...EB 8386 EN 27...