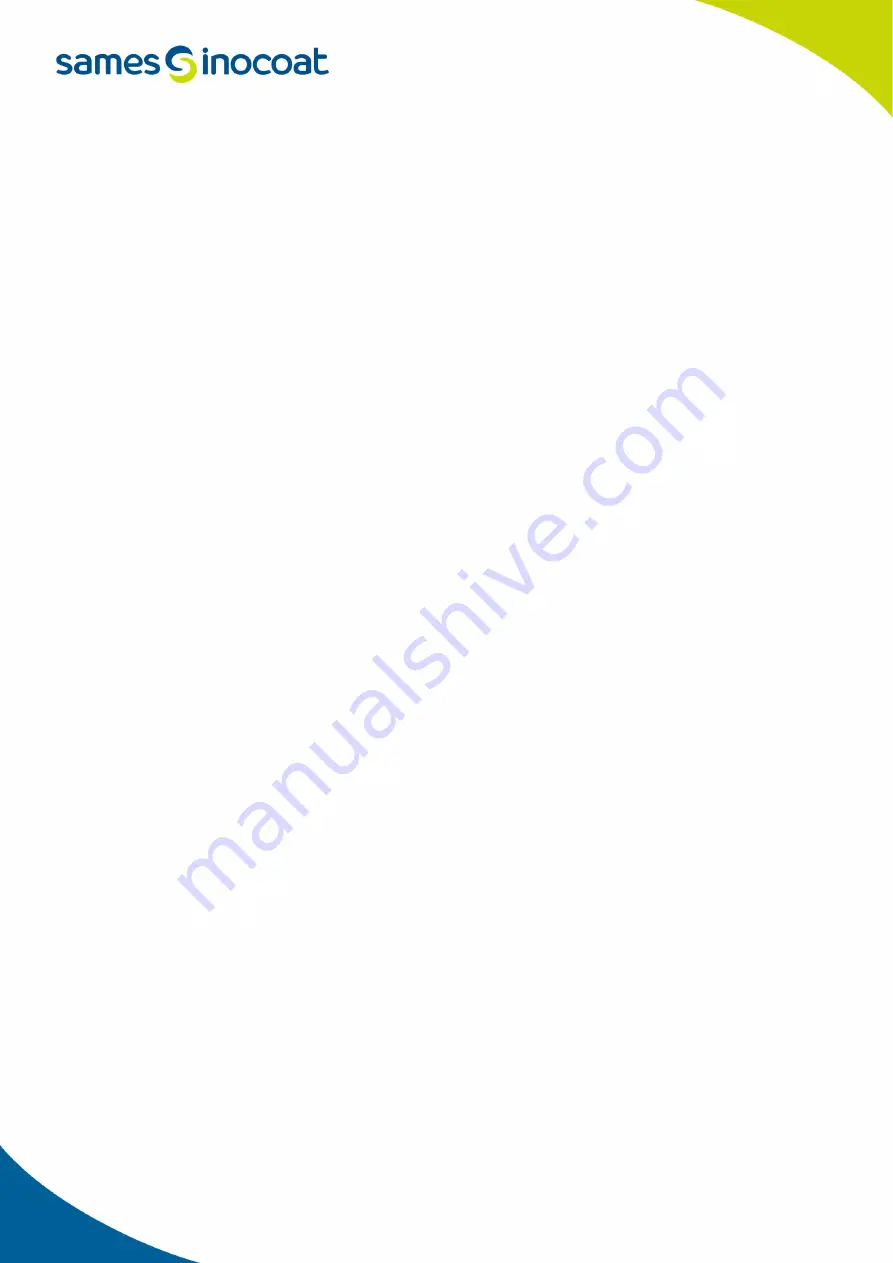
11
Member of Exel group
DRT7142
B - 2023/06
1.7. Guarantee
Under the guarantee, which applies only to the buyer,
Sames
agrees to repair operating faults resulting from a
design fault, materials or manufacture, under the conditions set out below.
The guarantee claim must define the exact nature of the fault concerned, in writing.
The
Sames
guarantee only covers equipment that has been serviced and cleaned according to standard procedures
and our own instructions, that has been fitted with parts approved by
Sames
or that has not been modified by the
customer.
More precisely, the guarantee does not cover damage resulting from:
• the customer's negligence or inattention,
• incorrect use,
• failure to follow procedures,
• use of a control system not designed by
Sames
or a
Sames
control system modified by a third party without
written permission from an authorized
Sames
technical agent,
• accidents such as: collision with external objects, or similar events,
• flooding, earthquake, fire or similar events,
• the use of seals that do not comply with those recommended by
Sames
,
• pollution of pneumatic circuits by fluids or substances other than air.
The
Sames
Inocenter
equipment is covered by a warranty (refer to the general sales conditions for its application).
The guarantee does not apply to wearing parts.
The guarantee will take effect from the date of the first start-up or of the provisional acceptance report.
Under no circumstances, either in the context of this guarantee or in other contexts, will
Sames
be held responsible
for physical injury or intangible damage, damage to brand image and loss of production resulting directly from its
products.