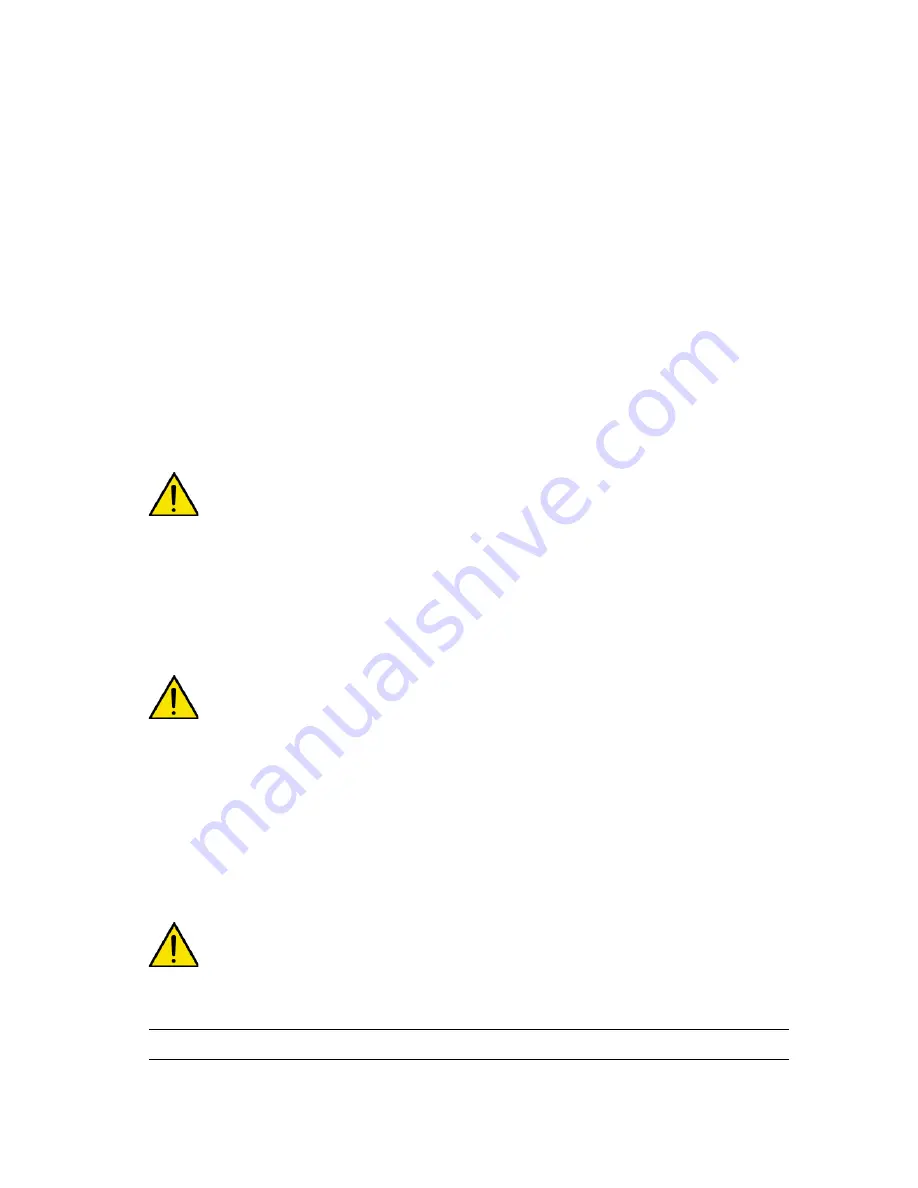
Index revision : F - November 2017
11
7012
1.5.3. Product Quality
The paint must be filtered to prevent any damage to the atomizer.
The maximum permissible particle size in the atomizer is 200 µm.
1.5.4. Bearing Safety
The compressed air connection to the air bearing must be made directly to the supply circuit
without the use of an isolating valve.
During operation, the air bearing must be continuously under pressure, otherwise considerable
damage may be caused. A sudden cut in the air supply could destroy the air bearing of the
turbine. Wait until the turbine has stopped completely before cutting off the bearing air.
Procedure for cutting off air to the air bearing:
• Switch off the turbine rotation air supply
• Wait until the turbine has stopped completely (at least 150 s).
• Switch off the bearing air supply.
Running the turbine with bearing air pressure of less than 6 bar at the atomizer inlet can dam-
age the bearing. The standard bearing air pressure is 6 bar at the air control cabinet.
All these pressure values are measured at the atomizer inlet. If the bearing pressure drops below
6 bar at the turbine or atomizer inlet, cut off the air supply to the turbine.
In addition, a 25-liter air reserve should be available so that the turbine brakes gradually if the
main air supply is cut off suddenly.
WARNING : The guarantee does not cover faults that occur if the turbine is operated with insuf-
ficient bearing air pressure.
1.5.5. Locking
Do not atomize the product if the bellcup is not turning at a speed of at least 15000 rpm. At
lower speeds, paint or solvent may enter the turbine, bearing and control circuits. Opening the
head valve, injector rinsing valve and bellcup exterior rinsing valve must be prohibited when
the bellcup is not turning. Only qualified personnel are authorized to by-pass this locking system
for flow rate checks
WARNING : If the turbine is not already operating, wait, after starting it up, until the bellcup
reaches at least 15000 rpm before opening the head valve. The recommended
minimum waiting time is 2 seconds.
1.5.6. Shaping Air
Do not atomize the product until the shaping air rate is at least 80 Nl/mn (i.e. 0.3 bar at the
atomizer inlet). If it is less, there may be a feedback of atomized product which fouls the outer
cover and the inside surface of the air shroud resulting in application faults.
1.5.7. High Voltage
Disable the high voltage if the PPH 308 is not operated for a prolonged period (conveyor shut-
down, no objects to be painted, slack periods, etc.) to prevent ionization of the air.
WARNING : The high voltage supply must be turned OFF before rinsing cycles, bell cup and
injector are engaged.