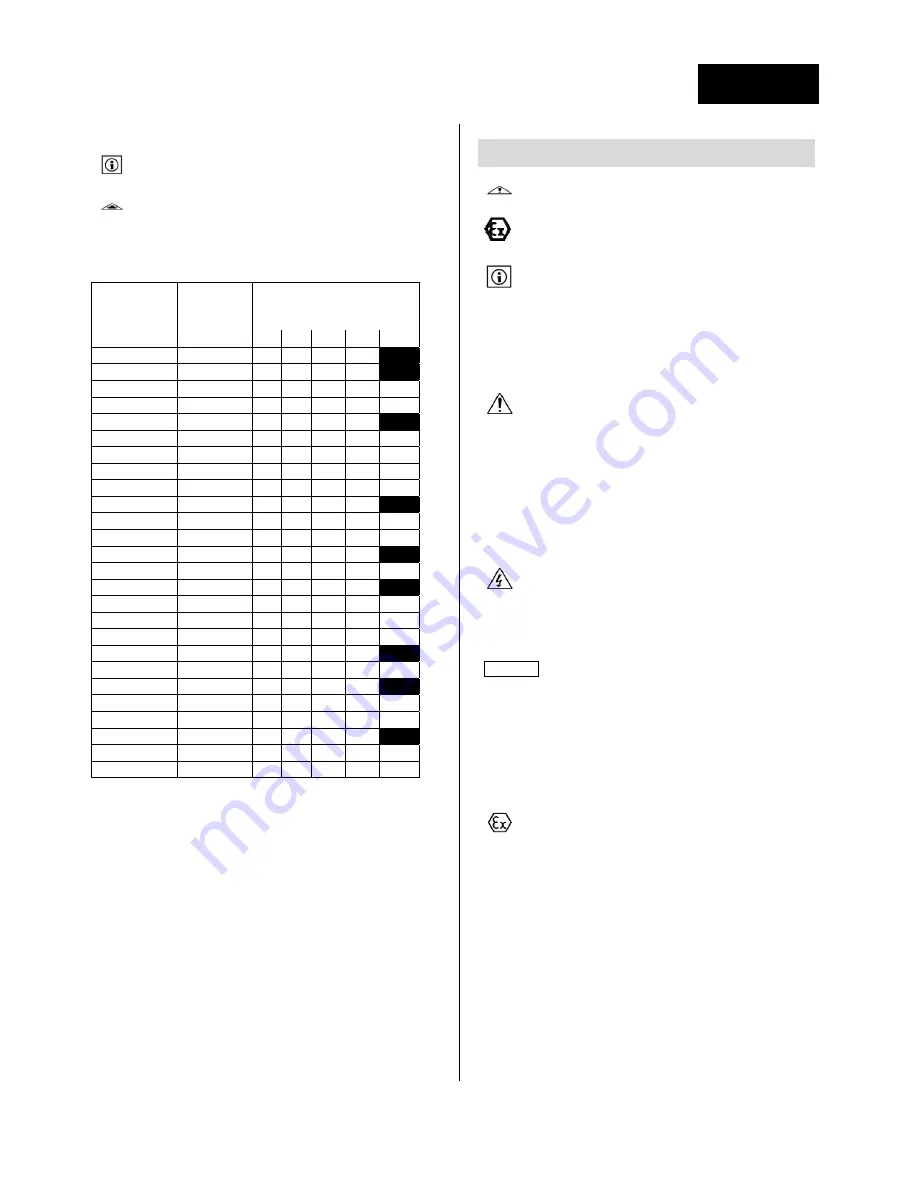
ENGLISH
17
is
reached
before
pump
has
primed.
Measure
liquid
temperature
and
modify
alarm
and
stop
trips
settings
accordingly.
Theoritically
the
pump
could
prime
up
to
8
meters
but
lifting
height
will
be
limited
to
6
meters
to
take
suction
line
head
losses
into
account.
Check
that
the
system
available
NPSH
(NPSH
A
)
is
always
higher
than
the
required
NPSH
(NPSH
R
)
of
pump
when
fluid
level
is
at
its
lower
point.
Theoretical
priming
times
(Nominal
Dia
of
pipe
=
pump
nominal
dia)
:
Pump
size
Pump
speed
Priming
time
in
seconds
vs
suction
lift
height.
[Tt]
2
3
4
5
6
S40
2900
21
47
78
135
S41
2900
27
57
93
153
S45
2900
12
22
35
47
62
S46
2900
5
8
13
23
34
S50
2900
17
29
46
83
S51
2900
19
34
55
87
155
S60
2900
19
29
42
56
77
S61
2900
10
15
21
29
41
S63
2900
7
10
14
19
33
S65
1450
30
58
83
186
S68
2900
9
14
19
26
38
S80(
‐
2)
2900
36
49
62
74
95
S80
2900
21
53
95
132
S83
2900
14
20
26
31
39
S85
1450
32
63
100
152
S88
2900
4
7
11
18
26
S88
(210)
2900
5
8
11
15
20
S100
2900
19
30
38
45
54
S105
1450
38
69
110
167
S105
2300
9
13
17
21
25
S105
T114
1450
30
62
110
189
S108
2900
10
14
18
22
27
S120
1450
10
18
31
50
95
S150
1450
33
71
117
176
S160
1450
15
26
41
63
93
S170
950
28
51
85
129
181
Priming
time
depends
on
lifting
height,
length
of
the
suction
line,
inner
diameter
of
suction
pipe
and
specific
gravity
of
the
fluid.
It
will
be
necessary
to
apply
correction
factors
to
know
priming
time
:
Tt
=
table
with
Ha
=
Hg
x
d
Ta
=
Tt
x
L/Hg
x
(DT/DN)²
With
:
Tt
:
theoretical
priming
time
Ha
:
suction
height
with
specific
gravity
correction
factor
d
:
Specific
gravity
of
fluid
L
:
total
length
of
suction
line
DT
:
inner
diameter
of
suction
pipe
DN
:
pump
suction
flange
nominal
diameter
9
MAINTENANCE
9.1
GENERAL
INFORMATION
Only
properly
trained
and
skilled
staff
should
undertake
maintenance
operations.
Only
authorized
personnel
should
undertake
maintenance
on
ATEX
certified
equipments.
Make
sure
to
avoid
creation
of
explosion
hazard
while
proceeding
to
maintenance
in
a
ATEX
zone.
All
technical
documents
delivered
with
the
pump
should
be
known
and
should
be
available
near
the
pump.
The
maintenance
crew
should
be
informed
about
the
risks
linked
to
the
use
of
the
pump
and
to
the
pumped
fluids
before
they
can
start
working
on
the
equipment
(dangerous
products,
fluid
and
pump
temperature,
pressurized
parts,
…).
They
should
be
equipped
with
all
appropriated
individual
safety
protections
(glasses,
gloves,
…)
and
should
respect
local
industrial
and
security
rules.
Pump
contains
a
part
of
pumped
fluid
even
when
it
is
at
a
standstill.
Drain
and
flush
pump
casing
with
care
before
starting
pump
disassembly.
Appropriate
lifting
devices
should
be
available
to
help
personnel
moving
heavy
loads.
The
maintenance
area
must
be
clearly
identified.
Install
warning
boards
with
the
words
«
WARNING
:
machine
under
repair
!
»
on
the
pump
and
on
the
control
cabinet.
Any
work
on
the
machine
must
be
performed
when
pump
is
stopped.
Prior
to
any
maintenance
or
repair
work
the
motor
should
be
electrically
isolated
and
secured
against
uncontrolled
start.
Lock
the
main
switch
open
and
disconnect
circuit
breaker.
Withdraw
the
fuses
if
any.
WARNING
:
electrical
equipments
that
must
be
powered
on
during
the
maintenance
work
or
pressurized
equipments
must
be
clearly
identified.
End
of
maintenance
operations
:
all
protective
parts
that
were
removed
before
maintenance
should
be
reinstalled
and
all
security
devices
should
be
reactivated.
Pump
surrounding
area
should
be
cleaned.
9.2
MAINTENANCE
AND
PERIODIC
INSPECTIONS
SCHEDULE
It
is
recommended
to
build
up
a
maintenance
and
inspection
plan
to
ensure
a
reliable
use
of
pump
and
to
reduce
malfunctions
hazards.
Following
check
points
should
be
included
in
this
maintenance
plan
:
Check
state
and
working
of
securities
and
auxiliary
systems,
Check
and
adjust
gland
packing
(if
any)
for
visible
leakage,
Check
for
any
leaks
from
pump
gaskets
and
flanges
seals,
Check
lubricant
level
and
aspect
of
oil
(oil
lubricated
bearings)
in
bearing
bracket,
Check
running
time
and
replacement
frequency
of
lubricants
/
ball
bearings,
Check
the
bearing
bracket
housing
surface
temperature
on
ball
bearings
area,
Check
dirt
and
dust
is
removed
from
pump
and
motor
,
Check
coupling
alignment
(depending
on
pump
variant),
Check
if
there
is
unusual
noises
(cavitations,
hissing,
purring,
…)
or
excessive
vibrations.
Содержание S series
Страница 2: ...S INSTALLATION ET MISE EN SERVICE N M S n 4071640 Ed 5 10 13 FRAN AIS...
Страница 23: ...FRAN AIS 23...
Страница 24: ...24...
Страница 25: ...S INSTALLATION AND OPERATING INSTRUCTIONS N M S n 4071640 Ed 5 10 13 ENGLISH...
Страница 26: ...2...
Страница 48: ...24...