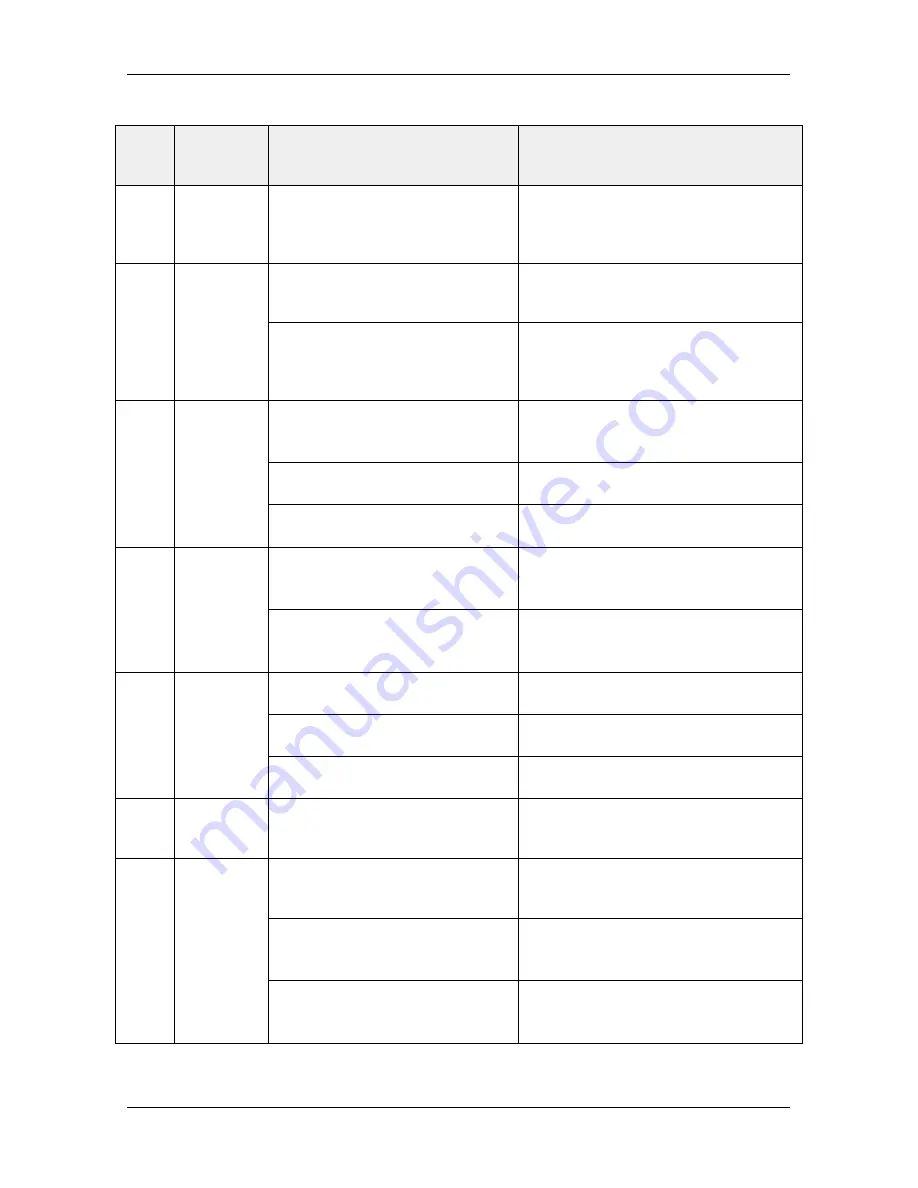
PDM20 Series
- 46 -
Fault
code
Fault type
Possible reasons
Solution
3
.
The power of the SPD is too
low
3
.
Use bigger power SPD
E005
Over
voltage in
accelerated
running
1
.
The input voltage is abnormal 1
.
Check input power supply
2
.
Restart rotating motor after
momentary outages
2
.
Avoid restarting after it is stopped
E006
Over
voltage in
decelerated
running
1
.
Too fast deceleration
1
.
Increase acceleration time
2
.
The inertia of load is too big
2
.
Increase dynamic braking modules
3
.
The input voltage is abnormal. 3
.
Check input power
E007
Over
voltage in
constant
speed
running
1
.
Abnormal changes happen to
input voltage
1
.
Install input reactor
2
.
The inertia of load is too big
2
.
Add proper dynamic braking
modules
E008
Hardware
over
voltage
1
.
The input voltage is abnormal 1
.
Check input power supply
2
.
Too fast deceleration
2
.
Increase deceleration time
3
.
The inertia of load is too big
3
.
Increase dynamic braking modules
E009
Bus under
voltage
1
.
The grid voltage is too low
1
.
Check grid input power supply
E010
Controller
overload
1
.
Too fast acceleration
1
.
Increase acceleration time
2
.
Restart rotating motor
2
.
Avoid restarting after it is stopped
3
.
The grid voltage is too low
3
.
Check grid voltage
Содержание PDM20 series
Страница 1: ...PDM20 Smart Mini Pump Drive User Manual Version Code PDM20 EN 60200256 1612 ...
Страница 12: ...PDM20 Series 11 Example Modify P0 02 from 0 to 1 Remarks 0 1MPa 100kPa 1bar 1kgf cm2 ...
Страница 14: ...PDM20 Series 13 2 3Dimensions Unit mm 136 116 176 158 114 105 124 138 ...
Страница 59: ...PDM20 Series 58 V1 1 Inverter ...