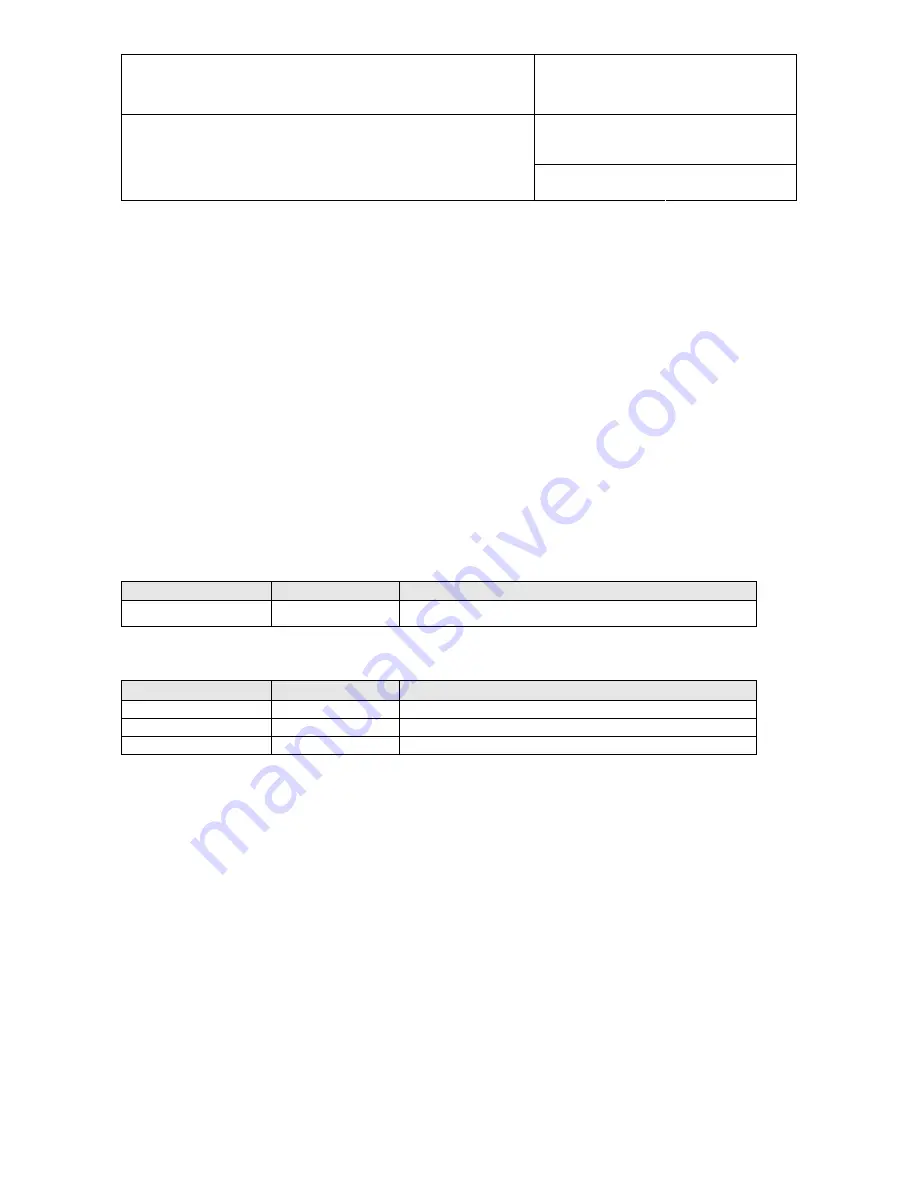
IN-E-HyFlex-V4_10
Rotronic AG
Bassersdorf, Switzerland
Document code
Unit
Instruction Manual
Document Type
HygroFlex transmitter version 4: instruction
manual
Document title
Page
60
of 61
© 2006; Rotronic AG IN-E-HyFlex-V2_10.doc
should be run parallel and as near as possible to the data cable, preferably in the same conduit.
The shield of the data cable should under no circumstances be used as equalization cable! The
conductors of the potential equalization cable should ideally be stranded in order to be effective
also in case of high- frequency interference.
The following point should also be observed:
•
Close the parasitic circuit
•
Connect all devices to the potential equalizing cable as often as possible. Electrical
conductors such as machine elements, metal tubes or supporting constructions should be
integrated into the system.
•
Protect the potential-equalization cable and connections against corrosion.
•
Select the cross-section of the potential equalization cable according to the maximum
equalization current.
If these different measures do not correct the problem, a galvanic separation according to ISO9549
may have to be installed. You may also want to consider the use of fiber-optic cables.
20 Document releases
Doc. Release
Date
Notes
_10
Dec. 6, 2006
See Hardware and firmware changes release 10
Hardware and firmware changes covered in document release-10:
Firmware Version Date
PCB-No.
4.0
Dec. 5, 2005
66.0738.0502
4.1a Sep.14,
2006
66.0738.0602
4.1b
Dec. 6, 2006
66.0738.0602
- Starting with PCB number 66.0738.0502 all models are equipped with a SMD power fuse
(250 VAC 1 A).
- Starting with PCB number 66.0738.0602:
The default factory setting for the probe supply voltage is 5 VDC. HygroClip EX probes require
15 VDC power supply. A third party analog probe may also require a supply voltage of more than
5 VDC (HygroFlex 2 and HygroFlex 3). Move jumper B20 to B19 to supply all probes with 15 VDC.
There is no connection between signal ground and terminal 3 of the power terminal block (TB1). If
so desired, a connection can be established by closing solder pad B18, next to TB1. On previous
versions of the PCB, the signal ground and terminal 3 of TB1 were always tied together.
- Firmware version 4.1a corrects an issue found when the ROTRONIC HW4 software (version
1.2.2 or higher) is used to adjust a HygroClip probe attached to the HygroFlex.
- Firmware version 4.1b allows ordering the HygroFlex 2 or HygroFlex 3 with both an Ethernet
(TCP/IP) and a RS-485 interface. When equipped with this option, the HygroFlex 3 does not have
an external Test connector.