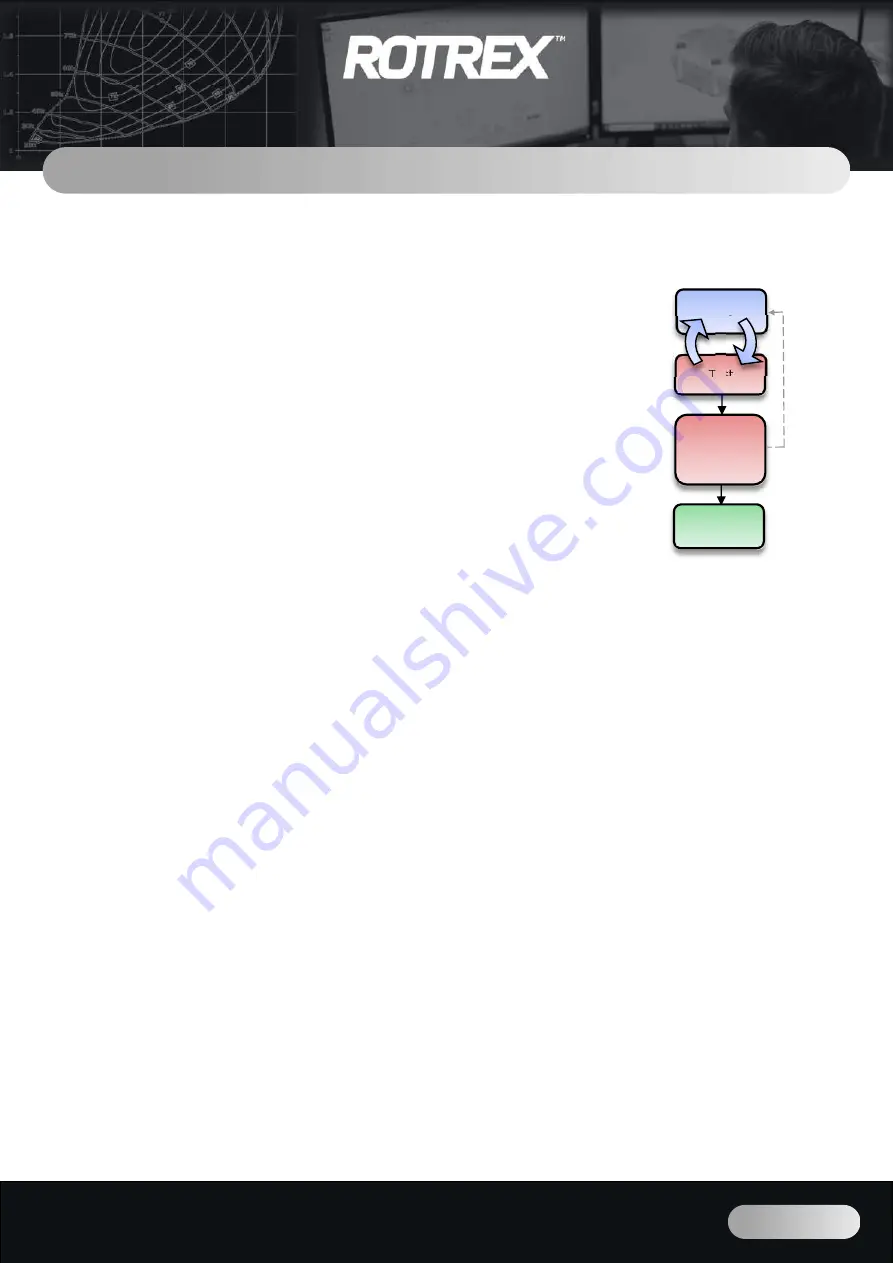
Technical Handbook
Rev. 1.6
WWW.ROTREX.COM
Page 27 of 41
Important notes and info sources
5. Important notes and info sources
5.1 Testing and verification
Once the application design process has come to the prototype phase
it is necessary to thoroughly test it before releasing it to verify the
system is working as expected and to rectify unforeseen issues. As
the diagram to the right indicates, it is important to separate iterative
development testing and verification testing. Iterative development
testing is all the “trial and error” testing done during the design
process and verification testing is the test program designed to verify
that the final design complies with minimum performance and
reliability target levels.
The intensity and strictness of the testing and verification process will
depend on a wide variety of factors (i.e., experience, system
complexity, cost-benefit criteria, resource constraints, etc.) and
therefore the best advice here is to apply common sense and follow
a conservative approach. Shortcuts never pay.
Rotrex recommends taking the following steps during the testing phase:
A.
Verify proper oil conditions: the exact amount of oil needed depends on the
components of the oil circuit chosen. Determine the appropriate oil amount needed
for the application during the testing phase. Remember to use the correct oil level
check procedure described in Section 4.4.2 of this document. Adjust oil accordingly
and document the amount needed since this information will be very important to
include in your application documentation (refer to Section 5.2). Once oil flow and
level are verified, it is necessary to check that the oil remains below the maximum
temperature during harsh climate and operating conditions. Dedicated desert/hot
climate testing is highly recommended. Rotrex recommends installing a
monitoring/logging system of the oil canister temperature during all testing, placing
the sensor as far down in the canister as possible. The temperature values
measured must not exceed 80°C (176°F) under any condition
B.
Verify vehicle performance: check that the vehicle performs as desired on the dyno
and in the field and double-check that the supercharger is running within the
allowed speed range. Keep a close eye on electronic control performance over time
and under different variables such as fuel grades and altitude. Rotrex recommends
building a monitoring/logging system into the test vehicles to make sure the most
important parameters are well within acceptable values. To ensure performance
uniformity, perform tests under the most typical configuration variations (i.e.,
common modifications such as air filters, exhaust system changes etc.)
C.
Belt routing and tension: despite all efforts to get a good routing during the design
phase you may need to make adjustments. A proper belt drive is very important
to prevent issues such as boost loss due to belt slippage, short belt drive life and
noise. During the test phase mentioned above you can check for evidence of
misalignment or wrong tension by listening, smelling, and watching the
supercharger operate at different points. Burned rubber smell, belt “dust”, belt
oscillation and unstable boost are typical signs of a problem. Excessive belt tension
and misalignment can eventually cause a failure in the belt and/or supercharger
pulley
Design
Test
Design
Verification
Testing
(DVT)
Approval
and release
Содержание C15-16
Страница 1: ...WWW ROTREX COM...