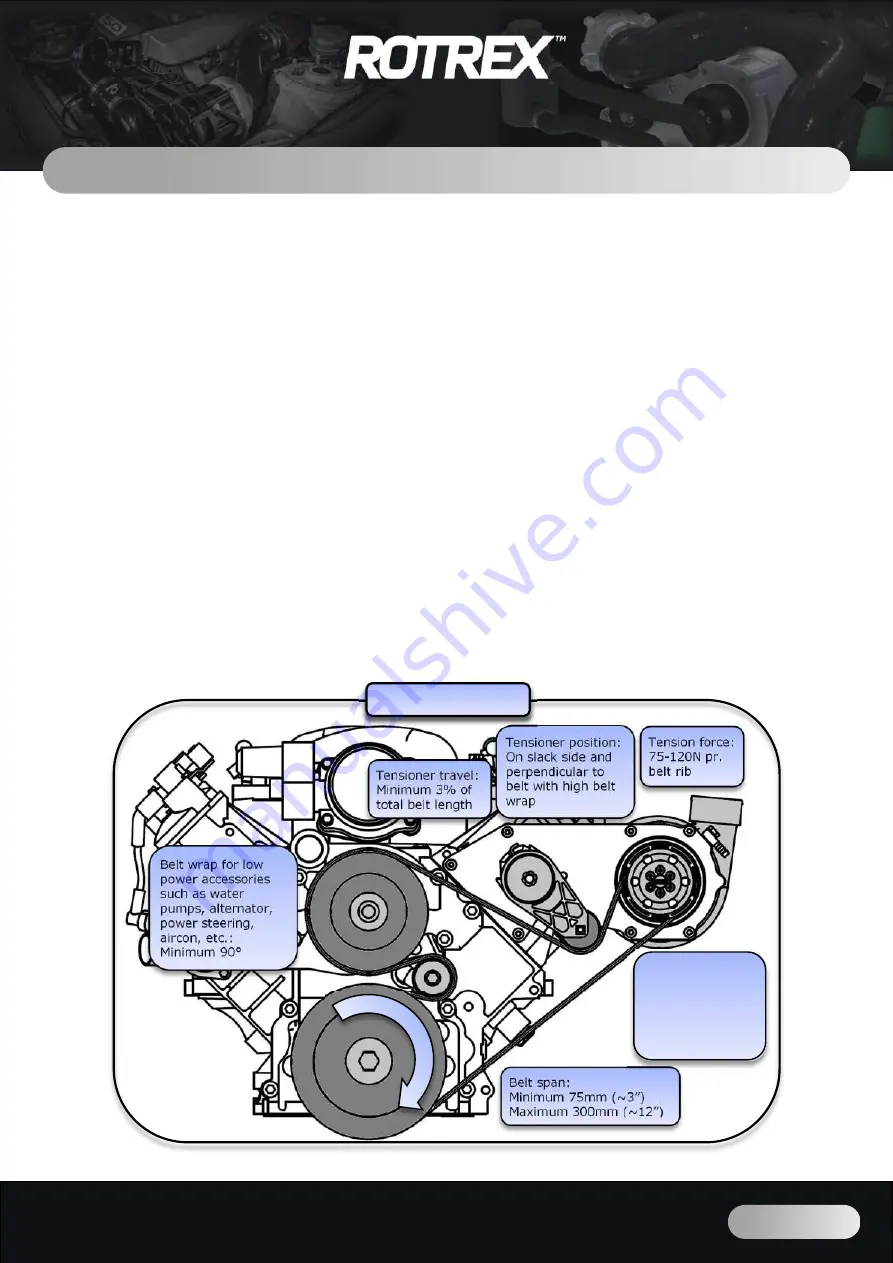
Technical Handbook
Rev. 1.6
WWW.ROTREX.COM
Page 12 of 41
Designing and handling interfaces
4.2 Belt drives
4.2.1 Belt routing
Due to the apparent simplicity of the belt drive, installers and designers tend to disregard
its importance. The single most frequent source of supercharger installation problems can
be traced back to the belt drive or design and manufacturing of belt drive components
such as brackets, tensioners, pulleys and mounting points.
Paying special attention to the
belt drive can improve performance, durability, service life and ease of service
significantly.
To analyse a belt drive properly you should contact a belt manufacturer with detailed
information of all the components in the drive and the conditions it will be run under. From
this, an estimated lifetime and frequency analysis can be made to give a reasonable
evaluation of the durability of the belt drive.
A more simplistic approach can be taken for prototype work. These guidelines are rule of
thumb only and must be accompanied by many hours of extensive testing on multiple
installations to get a true picture of the rigidity of the belt drive.
It is advisable to run the supercharger from a separate belt and crank pulley. Leaving the
vehicle’s existing belt drive untouched reduces the risk of wear and failure of the belt and
subcomponents. For twin charger applications we advise to run each supercharger on a
separate belt to maximize durability.
Belt wrap for low
power accessories
such as water
pumps, alternator,
power steering,
aircon, etc.:
Minimum 90°
Belt span:
Minimum 75mm (~3”)
Maximum 300mm (~12”)
Tensioner position:
On slack side and
perpendicular to
belt with high belt
wrap
Tension force:
75-120N pr.
belt rib
Tensioner travel:
Minimum 3% of
total belt length
Clockwise
example
Belt wrap for high
power pulleys
such as crank and
supercharger:
Optimum 180°
Minimum 120°
Содержание C15-16
Страница 1: ...WWW ROTREX COM...