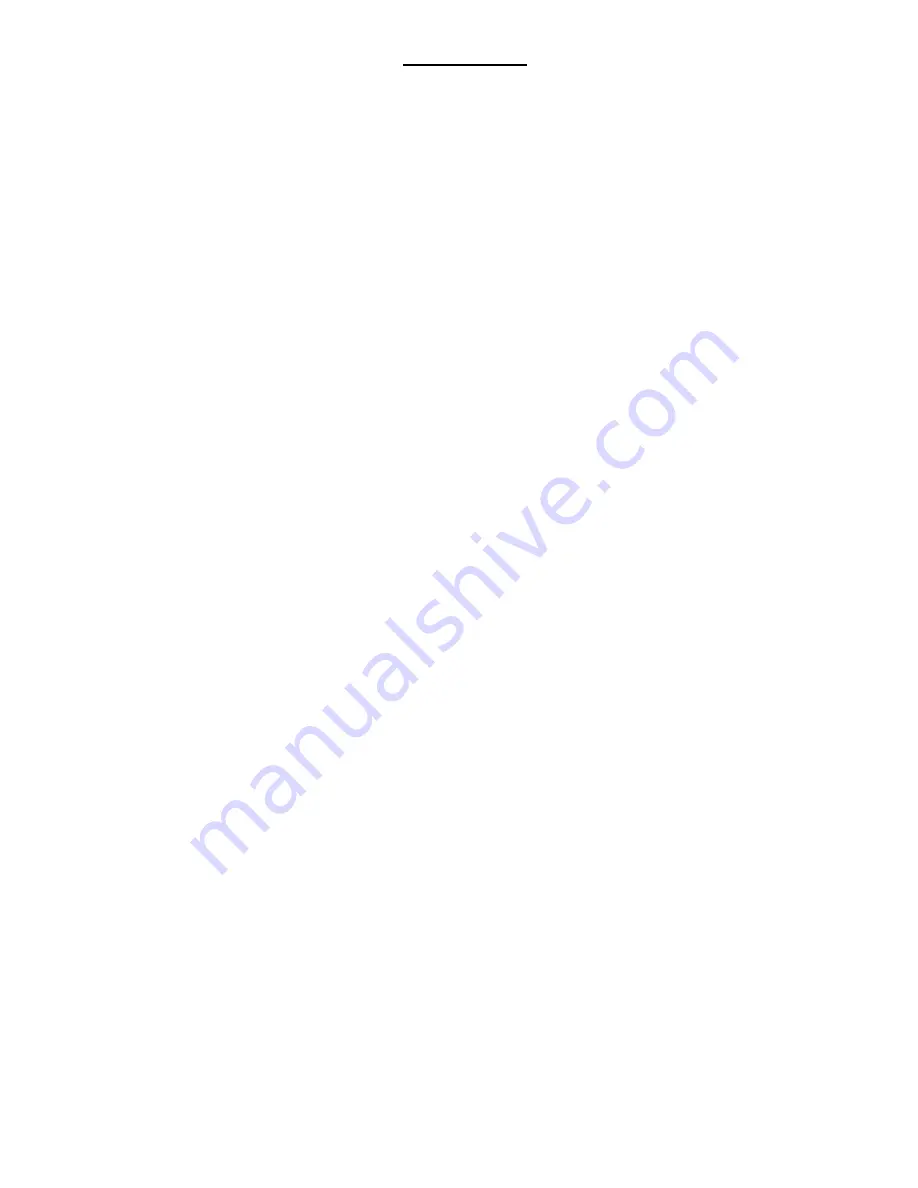
© 2017 CHARLES ROSS & SON COMPANY
10
OPERATION
A. HYDRAULIC LIFT.
1. The standard hydraulic lift is an air/oil hydraulic system that is raised and lowered using manually
operated controls.
2. The air/oil hydraulic reservoir is normally shipped empty and will have to be filled with the proper amount
of a non-foaming hydraulic oil and a clean dry source of 80-100psig compressed air. Refer to the
"INSTALLATION" section of this manual for specific details.
3. The manual lift controls consist of a 3-Way Air Control Valve which has three (3) positions, pressure,
neutral and exhaust. To raise the Mixer, set the 3-Way Air Control Valve to the pressure side, allow the
air/oil reservoir to pressurize and then while holding the 3-Way Air Control Valve in the “pressure” position,
with your other hand, actuate the Hand Valve (Oil Control Valve) to raise the Mixer. To lower the Mixer, set
the 3-Way Air Control Valve to the exhaust position, allow the pressure to be released, then while holding it
in the “exhaust” position, actuate the Hand Valve (Oil Control Valve). You can regulate the rate of travel via
the Hand Valve (Oil Control Valve).
B. MIX CAN.
Before starting the mixing operation the Mix Can must be securely attached to the Can Lock. The Mix Can is
positioned and held in place by two Locating/Locking Pins. Depending on the locking system, these pins are
either located between the back of the Mix Can (180-degrees) and the Hydraulic Cylinder or on Base
Extensions which are at the floor level. Appropriate grounding cables should also be attached to the Mix Can.
C. VARIABLE SPEED CONTROL.
1. The speed of the agitators can be controlled by using variable frequency speed controllers installed in the
Operator Control Panel or supplied as individual VFD’s. The Control Panel typically includes a color Touch
Screen Control and Display system. Refer to the Operator Control Panel and HMI Manual for specific in-
structions.
D. MIXING.
The art of "Mixology" is not always as simple as just putting all of the materials into the mixer and turning it
on. To achieve the best quality and consistency, proper selection of materials, formulation and equipment
must be matched with proper mixing technique. There are typically 3 stages to the "wet" mixing operation:
- Incorporation.
- Wetting.
- Breakdown of particle clusters (aggregates and agglomerates).
The typical "wet" mixing method is as follows:
1. Add the appropriate amount of the fluid materials, enough to cover the mixing blade(s) that will be
used during the initial mixing process.
2. Turn on the appropriate mixing blade(s) and run at a speed sufficient to allow incorporation of the
next material.
3. If the next material is a powder, meter the powder into the fluid a rate that will allow proper "wet-
ting" of the powders into the fluids. Dumping large lumps into the batch may cause damage to mix-
ing blades and will increase the mixing time.
4. Increase the mixer speed as needed, usually to maintain a vortex.
- Be careful not to "over-vortex" the batch which may allow unwanted air to be incorporated.
Содержание CDA-50
Страница 19: ...2017 CHARLES ROSS SON COMPANY 19 SIDE VIEW CDA 50...
Страница 20: ...2017 CHARLES ROSS SON COMPANY 20 DRIVE VIEW CDA 50...
Страница 21: ...2017 CHARLES ROSS SON COMPANY 21 VACUUM COVER VIEW CDA 50...
Страница 22: ...2017 CHARLES ROSS SON COMPANY 22 ANCHOR SHAFT BEARING HOUSING VIEW CDA 50...
Страница 23: ...2017 CHARLES ROSS SON COMPANY 23 ANCHOR BLADE W SCRAPERS VIEW CDA 50...
Страница 24: ...2017 CHARLES ROSS SON COMPANY 24 DISPERSER SHAFT BEARING HOUSING VIEW CDA 50...
Страница 25: ...2017 CHARLES ROSS SON COMPANY 25 MIX CAN VIEW...
Страница 26: ...2017 CHARLES ROSS SON COMPANY 26 APPENDIX VENDOR PRODUCT INFORMATION...