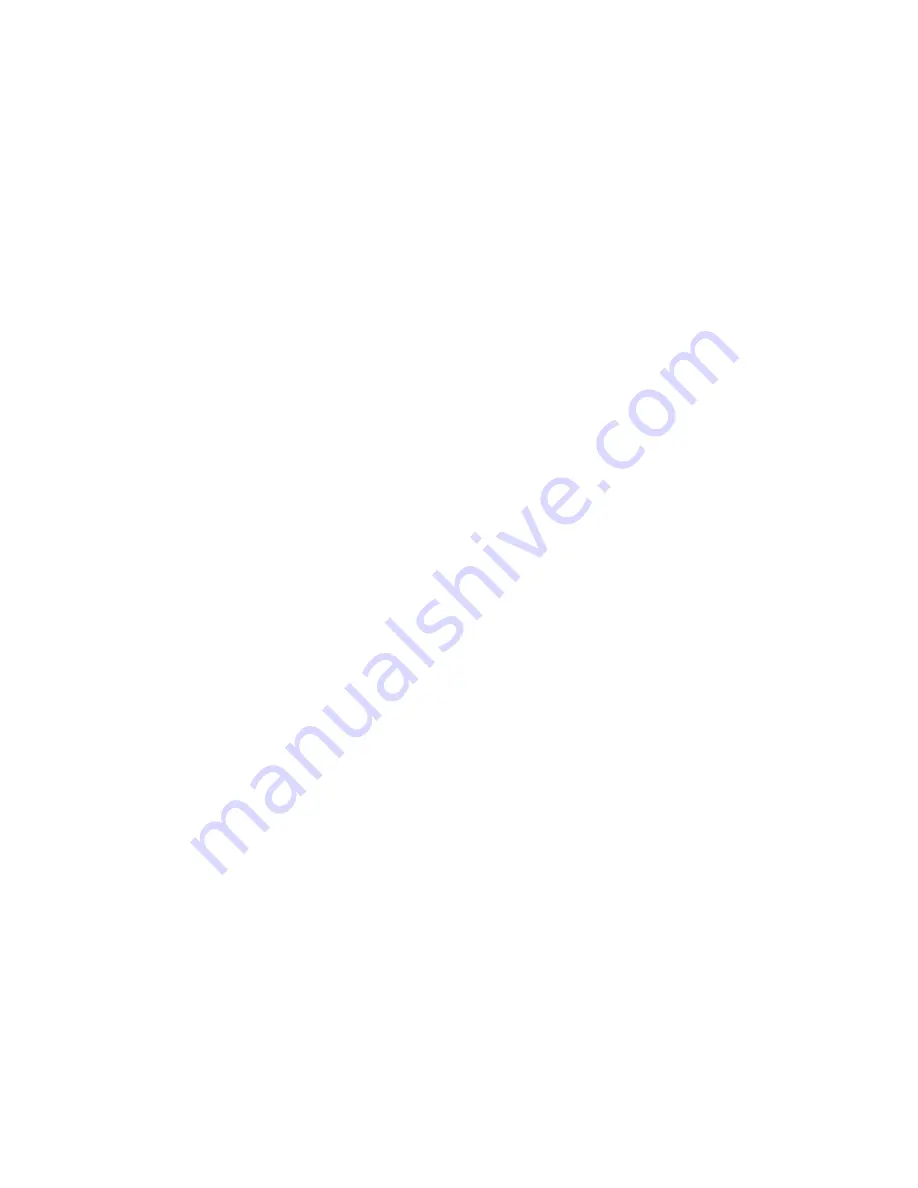
© 2017 CHARLES ROSS & SON COMPANY
8
4. Rotating the Anchor Blade by hand will confirm the Anchor Blade is properly centered and no contact is
being made with the Mix Can ID.
5. Apply Vacuum pressure to the Mixer to test the seal, rotate the Anchor Blade again to reconfirm clearance.
D. POWER REQUIREMENTS, ELECTRICAL INSTALLATION.
1. The CDA is designed to operate on a power supply of either 230 volts or 460 volts, 3 phase, 60 Hertz.
Check all electrical components for the correct power supply before connecting any power source.
2. All electrical installations should be performed by a licensed electrician and conform to the national, state
and local electrical codes.
3. Refer to the electrical schematics specific to the control panel for detailed installation requirements.
4. A disconnect equipped with breakers or fuses should be installed between the power source and the control
panel.
5. Install all the required ground leads and/or grounding cables.
6. To avoid possible damage to the equipment or personal injury, the electrical installation and all electrical
systems must be checked and tested prior to starting the equipment.
a. With the emergency stop button depressed, apply power to the system.
b. Check the line voltage on each leg.
c. If the line voltage is /-10% of the rated voltage, apply power to the controls by turning the
disconnect to the "ON" position and/or pulling out the emergency stop button.
d. All systems should have power at this time.
e. DO NOT START THE DRIVES OR MOTORS AT THIS TIME!
f. Check the operation of all limit switches, proximity sensors and other electrically operated safety
devices.
g. Check the rotation of the shaft by
"jogging"
the drive/motor. Correct shaft rotation will be clock-
wise. If the direction is reversed, Lockout all power to the controls and reverse the connection of any
two of the three main (hot) power leads. Check the direction again before start-up.
h. Check all systems and drives for proper operation and rotation.
CAUTION:
Shafts with product lubricated bushings or single/double mechanical seals should not be run dry. Dry
running will cause premature failure of the bushing or mechanical seal.
E. LUBRICATION
1. Before starting the mixer, all oil/fluid levels for the mechanical seals, bearings, hydraulic lift system and
gear reducer must be checked and properly filled.
2. The oil level in the gear reducer must be checked and properly filled along with the vent plug removed and
reinstalled correctly. Follow the lubricating instructions on the nameplate of the reducer or in the
manufacturer’s literature. A suitable oil is AGMA Lubricant 7EP or 8EP, ISO-ASTM viscosity grade 460-
680. If the mixer is to operate in an unusually high temperature room, over 90 degrees F, a synthetic or heavy
duty oil must be used. Do not mix synthetic and petroleum based oils.
3. The fill plug is on the top of the gear reducer, the level plug is on the side and the drain plug in on the bottom
of the reducer. Refer to the gear reducer catalog in the Vendor Literature section.
4. Hydraulic Oil Reservoir (Air/oil tank).
a. The hydraulic oil reservoir is normally shipped “full” of oil but may require a small amount of oil to bring
it to the required level. If the reservoir is shipped empty it will have to be filled with the proper amount of a
non-foaming hydraulic oil prior to connecting compressed air and operating the hydraulic system. Fill the
reservoir to half way between the high/low marks on the dip stick.
Содержание CDA-10
Страница 18: ...2017 CHARLES ROSS SON COMPANY 18 SIDE VIEW CDA 10...
Страница 19: ...2017 CHARLES ROSS SON COMPANY 19 VACUUM COVER BEARING HOUSING VIEW CDA 10...
Страница 20: ...2017 CHARLES ROSS SON COMPANY 20 HSD BLADE VIEW CDA 10...
Страница 21: ...2017 CHARLES ROSS SON COMPANY 21 MIX CAN VIEW CDA 10...
Страница 22: ...2017 CHARLES ROSS SON COMPANY 22 THERMOCOUPLE ASSEMBLY LOW PROFILE 1 8 FLUSH MOUNT...
Страница 23: ...2017 CHARLES ROSS SON COMPANY 23 APPENDIX VENDOR PRODUCT INFORMATION...