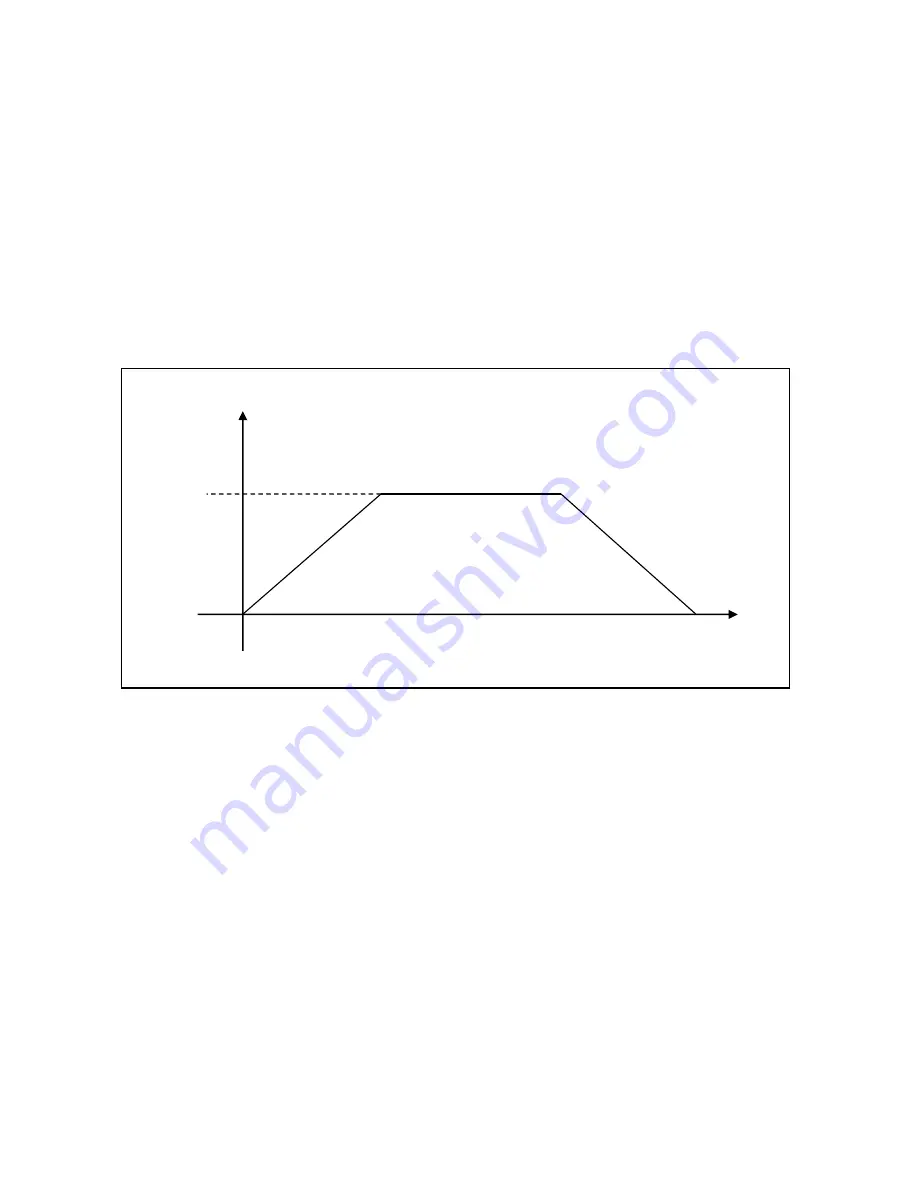
20-02245 REV E
7
1.
Mount equipment as close as possible to the output shaft. This minimizes
bearing drag forces on the axis.
2.
Mount the equipment so that the center of gravity is close to the center of
axis to minimize torque requirements. In some cases it is advantageous
to add counterweights to achieve a more balance configuration.
3.
When possible, minimize cross sectional area of the equipment that will be
exposed to hydrodynamic drag forces.
CONTROLLING THE UNIT
Refer to the communication protocol (21-30022) for controlling your pan-and-tilt.
Movement on each axis will follow a path similar to the figure above when ramping
commands are used. The user can send rotate or position commands to move each
axis. To operate the pan-and-tilt without stalling or slipping, the user should calculate
the amount of torque required to hold the load on each axis. Then, once this is known,
the user should refer to the torque curve to find the maximum velocity that can be
achieved without a stall occurring. For example, if the user knows their maximum load
is 20 lbs. at a foot (requiring 20 ft-lbs.), the axis should not move faster than 6.5
degrees/sec. The user should not send rotate commands faster than 6.5
degrees/second and the maximum velocity of the position speed profile should be
adjusted to 6.5 degrees/sec. This will limit the maximum velocity on position moves
only. The axis will brake at the last commanded braking value. Set the braking value
according to the torque curve. The user can also adjust the acceleration.
BRAKING
MAX
VELOCITY
VELOCITY
DECEL = ACCEL
ACCEL
DISTANCE
SPEED PROFILE