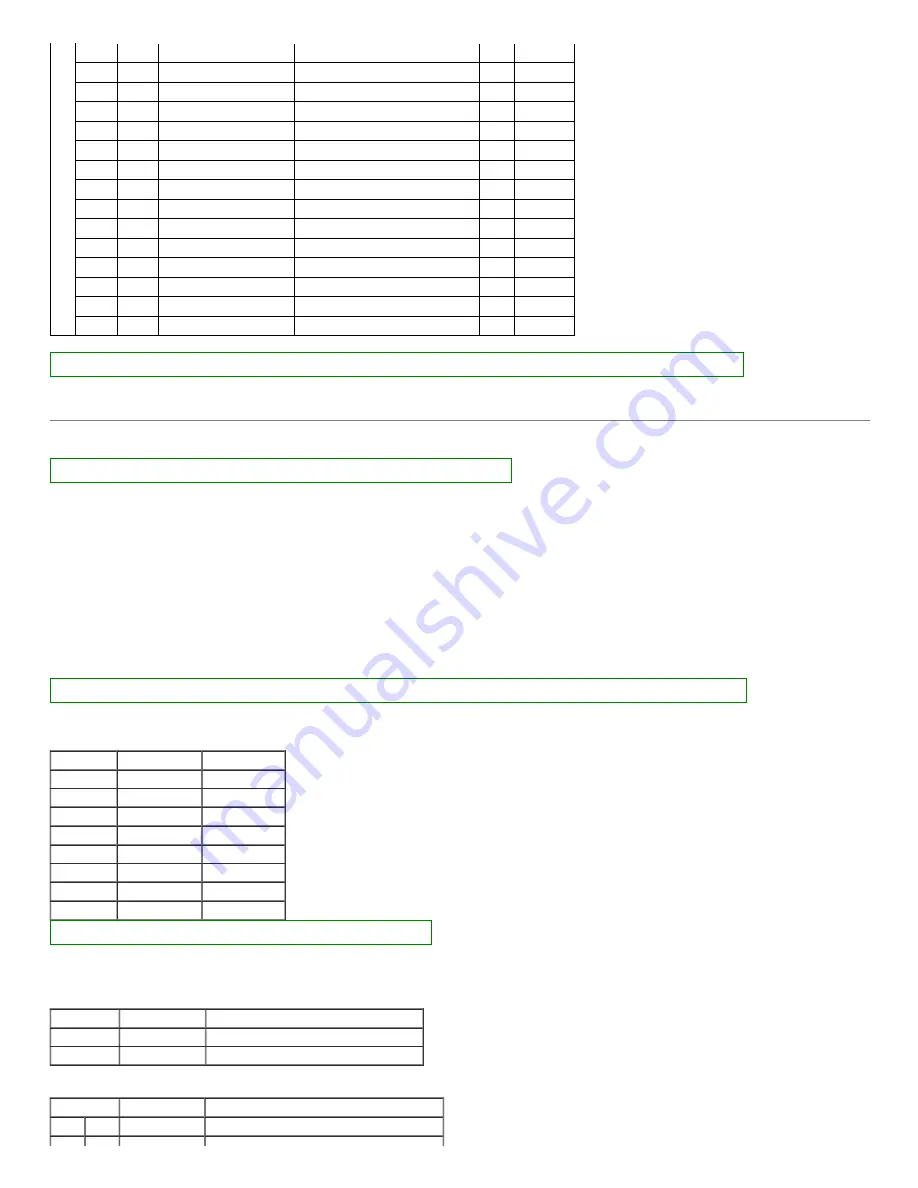
2/22/2018
XH430-W350
http://support.robotis.com/en/product/actuator/dynamixel_x/xh_series/xh430-w350_main.htm
4/15
251
1
Indirect Data 28
RW
0
578
2
Indirect Address 29
RW
634
580
2
Indirect Address 30
RW
635
582
2
Indirect Address 31
RW
636
…
…
…
…
…
628
2
Indirect Address 54
RW
659
630
2
Indirect Address 55
RW
660
632
2
Indirect Address 56
RW
661
634
1
Indirect Data 29
RW
0
635
1
Indirect Data 30
RW
0
636
1
Indirect Data 31
RW
0
…
…
…
…
…
659
1
Indirect Data 54
RW
0
660
1
Indirect Data 55
RW
0
661
1
Indirect Data 56
RW
0
Note : Protocol 1.0 does not support addresses greater than 256. Therefore, Indirect Address 29 ~ 56 and Indirect Data 29 ~ 56 can only be accessed with Protocol 2.0.
Address Description
EEPROM Area
Note : Any Data in EEPROM Area can only be modified when the value of Torque Enable(64) is cleared to ‘0’.
Model Number (0)
This address stores model number of the Dynamixel.
Firmware Version (6)
This address stores firmware version of the Dynamixel.
ID (7)
The ID is a unique value in the network to identify each Dynamixel with an Instruction Packet.
0~252 (0xFC) values can be used as an ID, and 254(0xFE) is occupied as a broadcast ID. The Broadcast ID(254, 0xFE) can send an Instruction Packet to all connected Dynamixels simultaneously.
Note : Please avoid using an identical ID for multiple Dynamixels. In order to change the ID in the EEPROM Area, Torque Enable(64) has to be cleared to ‘0’ in advance.
Note : Please avoid using an identical ID for multiple Dynamixels. In order to change the ID in the EEPROM Area, Torque Enable(64) has to be cleared to ‘0’ in advance.
Baud Rate (8)
Baud Rate determines serial communication speed between a controller and Dynamixels.
Baud Rate
Baud Rate[bps]
Margin of Error
0
9,600
0.000%
1(Default)
57,600
0.000%
2
115,200
0.000%
3
1M
0.000%
4
2M
0.000%
5
3M
0.000%
6
4M
0.000%
7
4.5M
0.000%
Note : Less than 3% of the baud rate error margin will not affect to UART communication.
Return Delay Time (9)
After the Dynamixel receives an Instruction Packet, it delays transmitting the Status Packet for Return Delay Time (9). For instance, if the Return Delay Time(9) is set to ‘10’, the Status Packet will be
returned after 20[μsec] when the Instruction Packet is received.
Values
Description
Unit
2[μsec]
-
Range
0 ~ 254
Default value ‘250’(500[μsec]), Maximum 508[μsec]
Drive Mode (10, Available after Firmware version 38)
Drive Mode
Definition
Values
Bit 7
0x80
-
Unused, always ‘0’