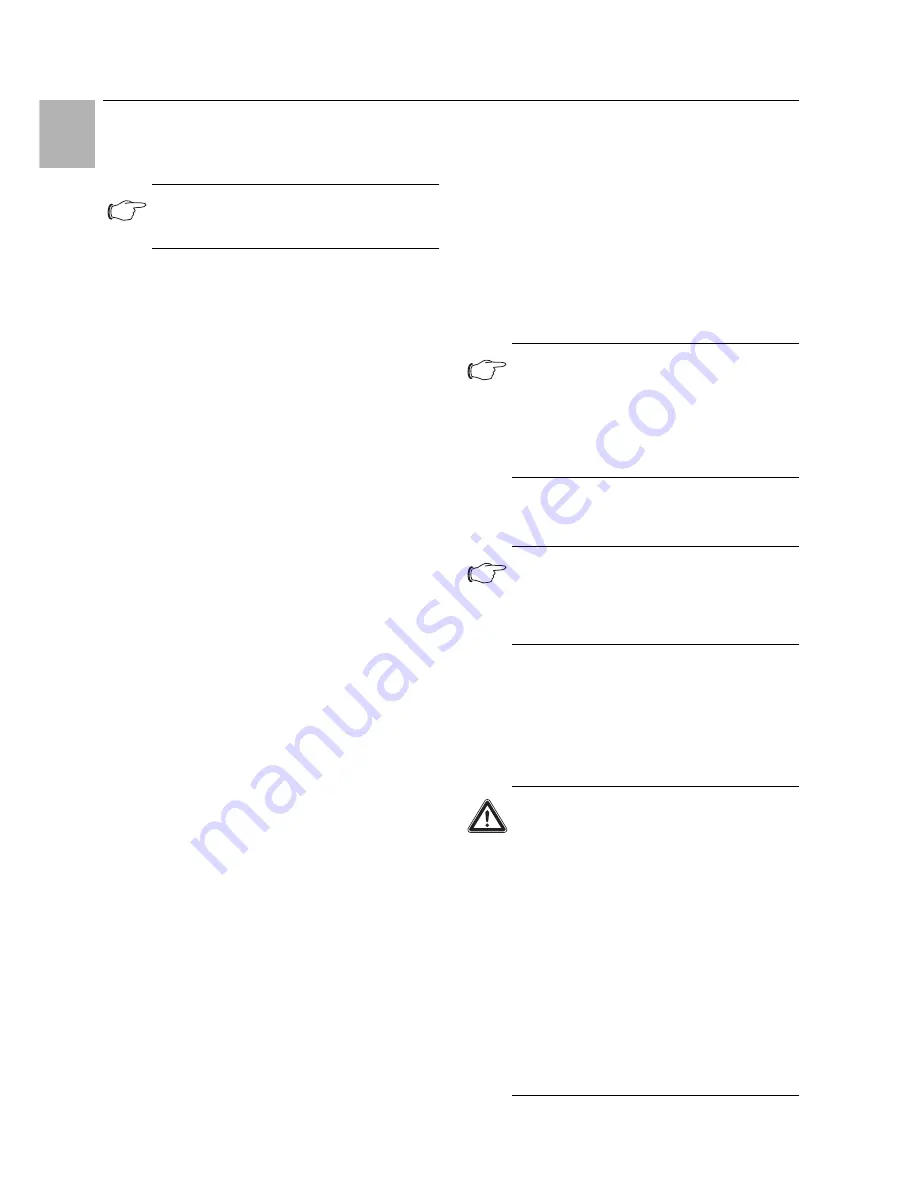
6 Installation
EN
18
Rittal LCU DX
Connections must be checked with a detector or using
a technique with a detection sensitivity as described in
EN 1779 with a bubble test (application of liquid) if the
test pressure is 1 x PS.
The manufacturer must verify that the test method used
complies with the aforementioned requirements.
EN 1779:1999 may be used as a basis for this test.
The detector must be calibrated at regular intervals as
per the manufacturer's instructions.
Any leak detected must be repaired and subjected to a
further leak test.
1. Systems with dry nitrogen should be tested at a
maximum overpressure of 28 bar. When doing so,
the shut-off valves on the external unit should remain
closed. The external unit is pre-filled with refrigerant
and this must not be allowed to escape.
2. Check the complete pipe network and the system
parts for leaks. We recommend using Nekal spray to
check every connection, including screw connec-
tions, for leak-proofness.
Evacuating
1. After checking for leaks, remove the air from the sys-
tem. To do so, connect a vacuum pump and evac-
uate to a pressure of < 0.3 mbar (absolute pressure).
2. Break the vacuum at least twice, refill the system
with nitrogen, and evacuate again. Where possible,
implement double-sided evacuation of the suction
side and the pressure side of the compressor, to
which end a test/measurement connection must be
made in the liquid line.
Filling with refrigerant
1. The external unit is prefilled in the factory, the fill vol-
ume is adequate for a 5 m line pair. For longer pipe
lengths, additional refrigerant should be added in
accordance with section 11 "Technical specifica-
tions".
2. The system must only be filled gravimetrically (i.e. by
weight) using refrigerant as the liquid in the liquid
line. Only liquid R410A should be added. After-
wards, switch on the device and whilst it is running,
continue carefully restricted filling via the intake side
of the external unit until the required fill volume has
been added.
3. The set volume of refrigerant is determined by
weighing the refrigerant bottle during the filling pro-
cess.
4. The additional fill volume or the new total fill volume
should be noted on the rating plate and operating
manual.
6.3
Connecting the condensate discharge
Any condensate which may develop is collected in the
condensate collecting tray of the internal unit. For univer-
sal use, the internal unit has two condensate collecting
trays which may be fitted on the left or right of the enclo-
sure, depending on the installation position.
Connect the discharge hose supplied loose (internal
diameter 12 mm) at the bottom connection (external
diameter 12 mm).
The tray at the top is not used.
Route the discharge hose to a drain with odour seal
provided by the customer, so that any condensate
can be discharged from the device.
6.4
Electrical connection
6.4.1
General
The electrical connection can only be made on the ex-
ternal unit. The internal unit is supplied with power via
the external unit. A 3-wire power cable should be used
for this purpose. The corresponding pilot wires from the
internal unit to the external unit should be laid with the re-
frigerant lines in accordance with section 11.7 "Circuit
diagram".
Note:
Lower test pressures are admissible, provid-
ed there is an equivalent detection sensitivity.
Note:
In order to ensure safe condensate dis-
charge, the following points should be ob-
served:
– Lay the discharge hose so that it always
runs downhill and without any kinks.
– Do not constrict the hose cross-section.
Note:
Please keep the wiring plan readily available
so that it is always on hand when needed.
This is the only authoritative documentation
for this unit.
Caution!
Work on electrical systems or equip-
ment may only be carried out by an elec-
trician or by trained personnel under the
guidance and supervision of an electri-
cian. All work must be carried out in ac-
cordance with electrical engineering
regulations.
Contact with live electrical parts may re-
sult in fatal injury.
The unit may only be connected after the
aforementioned personnel have read
this information!
Use only insulated tools.