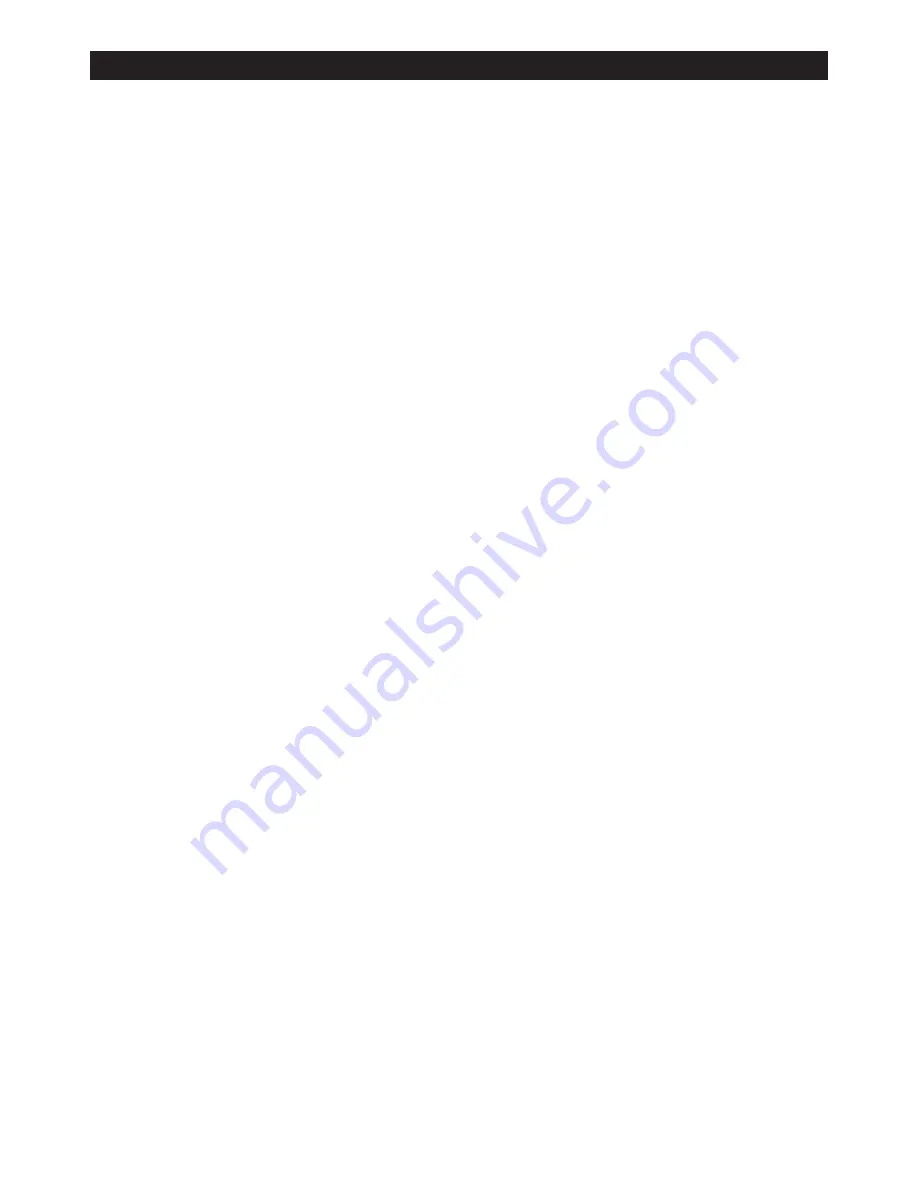
25
PARTS LIST
GEARBOX
OIL SEAL 25x40x7
BALL BEARING 6204
GEAR
CAP SCREW M6x25 (LH)
FLAT WASHER M6
FLANGE BOLT M6x12
BEARING 6201
GEAR
GEAR AND SHAFT
KEY A5x12
GEAR
KEY A5x10
GEAR 2-SPEED
OIL SEAL 11.8x2.65
FLAT WASHER M6
DOUBLE GEAR
GASKET
GEAR CASE
KEY A5x40
STEEL BALL M6
TENSION SPRING
SHAFT
OIL SEAL 25x47x7
LOCK WASHER M8
CAP SCREW M8x45
HEX BOLT M12x1.25x16
CAP SCREW M6x25
SHIFTER
430
432
433
434
501
502
503
504
505
506
507
508
509
510
511
512
513
514
515
516
517
518
519
520
521
522
523
524
525
DESCRIPTION
P23-150H-401
P23-150H-402
P23-150H-403
P23-150H-404
P23-150H-405
P23-150H-406
P23-150H-407
P23-150H-408
P23-150H-409
P23-150H-410
P23-150H-411
P23-150H-412
P23-150H-413
P23-150H-414
P23-150H-415
P23-150H-416
P23-150H-417
P23-150H-418
P23-150H-419
P23-150H-420
P23-150H-421
P23-150H-422
P23-150H-423
P23-150H-424
P23-150H-425
P23-150H-426
P23-150H-427
P23-150H-428
P23-150H-429
KEY
MFG. PART
NOTE:
Please reference the Manufacturer’s Part Number when calling for Replacement Parts.
For Parts under Warranty, the Serial Number of your machine is required.
401
402
403
404
405
406
407
408
409
410
411
412
413
414
415
416
417
418
419
420
421
422
423
424
425
426
427
428
429
DESCRIPTION
KEY
MFG. PART
SHIFTING SHAFT HANDLE
LOCK WASHER M6
OIL SEAL 9x1.8
ROLL PIN 5x25
SPROCKET
WASHER
CAP SCREW M6x16
FLAT WASHER M10
CHAIN TENSIONER
SHAFT
BRACKET
CHAIN 06B-1x48
SPROCKET
SPECIAL BOLT
CAP SCREW M6x10
KEY 5x15
FEED SPROCKET
SPRING
BRACKET
WASHER M8x28x3
CHAIN 06B-1x64
SHAFT
WASHER
EXT RET RING M15
CAP SCREW M6x40
LOCK WASHER
BRACKET
NUT M8
SPEED CHANGE HANDLE
P23-150H-430
P23-150H-432
P23-150H-433
P23-150H-434
P23-150H-501
P23-150H-502
P23-150H-503
P23-150H-504
P23-150H-505
P23-150H-506
P23-150H-507
P23-150H-508
P23-150H-509
P23-150H-510
P23-150H-511
P23-150H-512
P23-150H-513
P23-150H-514
P23-150H-515
P23-150H-516
P23-150H-517
P23-150H-518
P23-150H-519
P23-150H-520
P23-150H-521
P23-150H-522
P23-150H-523
P23-150H-524
P23-150H-525
GEARBOX & DRIVE ROLLER
Содержание 23-150H
Страница 19: ...19 NOTES Use this section to record maintenance service and any calls to Technical Support ...
Страница 20: ...20 PARTS DIAGRAM CUTTERHEAD ASSEMBLY ...
Страница 22: ...22 PARTS DIAGRAM PARTS DIAGRAM TABLE ASSEMBLY CABINET ASSEMBLY ...
Страница 24: ...24 PARTS DIAGRAM GEARBOX ASSEMBLY DRIVE ROLLER ASSEMBLY ...