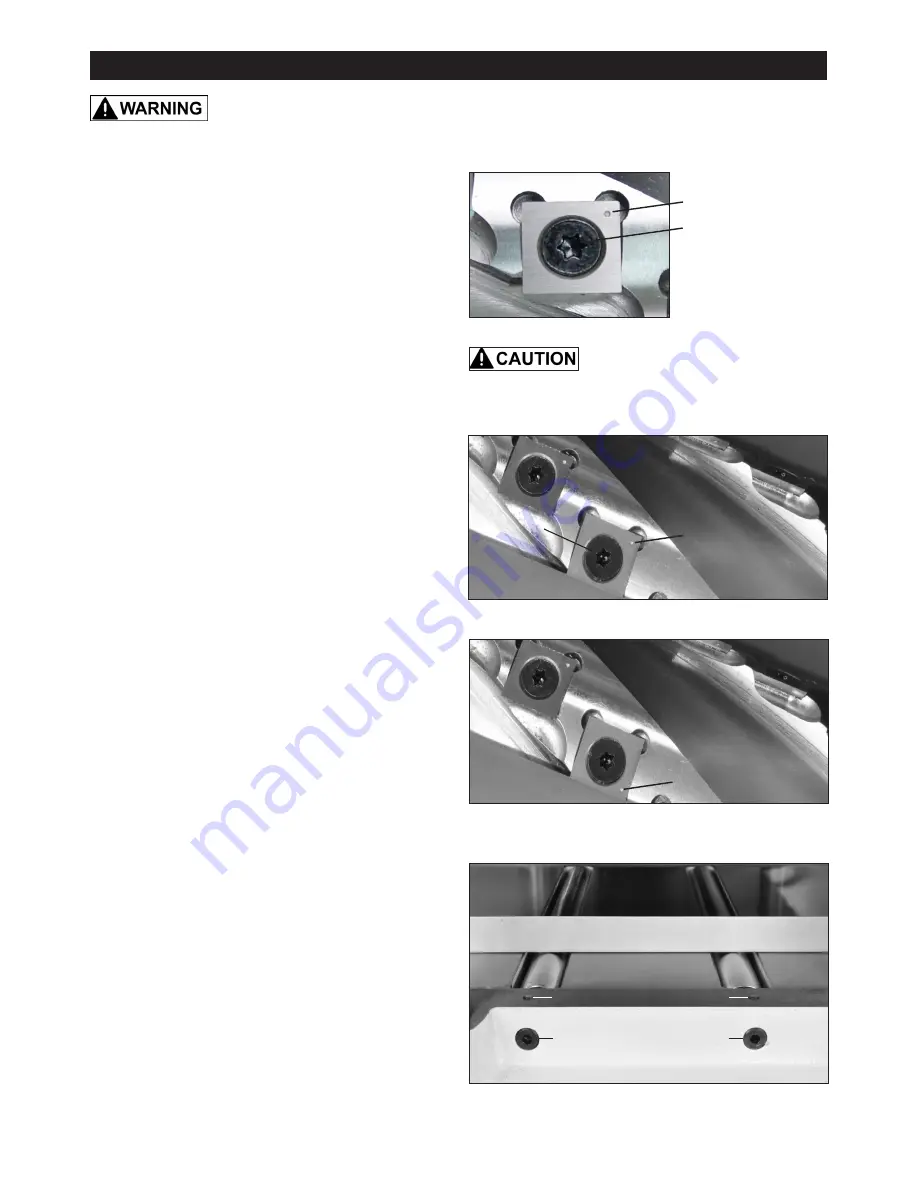
12
ADJUSTMENTS
ROTATING OR REPLACING KNIFE INSERTS
This machine has a helical cutterhead with four rows of
carbide knife inserts. Each of the 72 inserts on the
cutterhead are indexed and have four sharpened sides.
If the knives become dull, or one becomes nicked, simply
loosen the retaining screws with the supplied star head
screwdriver, lift up and rotate the inserts to a new sharp-
ened edge. No setting is required, as the cutterhead has
been machined to automatically index and set the inserts
in proper position for use. When all four sides of an insert
are dull, the insert can be easily removed and a new
carbide insert placed in the location.
To rotate or remove a carbide insert knife:
1. Unplug power cable.
2. Remove the Upper Cover (#1) and Dust Port (#2).
3. Remove the Screw (#37), that holds the Insert in the
cutterhead, and the Insert knife (#35). FIG. 15.
4. While the insert is removed, clean any resin buildup or
trapped dust from the surfaces of the cutterhead
with a suitable solvent. A tooth brush works well for
safe cleaning around the sharp inserts. Any accumu-
lated dust can affect the seating of the insert in the
cutterhead.
5. Rotate the insert so that a new sharpened edge is in
position. The inserts have a indication mark on their
top surface corner, so that you can reference the po-
sitioning of the insert's dulled or sharpened edges.
FIG. 15 -16.
6. Tighten the insert's set screw to lock the insert back
in position. DO NOT overtighten the screw or damage
to the insert may result. Torque to 50-55 in/lbs.
7. Plug in the power cable when you are ready to
resume planing.
FIG. 15
FIG. 14
CARBIDE INSERT
KNIFE HAS 4
SHARP EDGES
INDEX MARK
STAR HEAD
SET SCREW
THE MACHINE MUST NOT BE PLUGGED IN AND THE POWER SWITCH
MUST BE IN THE OFF POSITION UNTIL ADJUSTMENTS ARE COMPLETE.
Wear gloves when changing knife
inserts to avoid the risk of personal injury by cuts that
may result from touching the sharp edges!
FIG. 16
TABLE ROLLER ADJUSTMENT
The table rollers have been factory set before shipping.
Proper height adjustment can help eliminate snipe. They
should be set (0.001" to .003") (.03mm to .08mm) above
the table surface. The table rollers should also be parallel
with the table surface.
1. Place a straight edge across the bed rollers. With a
feeler gauge meaure the under the straight edge to the
table surface.
2. To adjust, loosen the small set screw (A-Fig. 17)
through the top of the table. Turn the outer large screw
(eccentric) (B-Fig. 17) until the desired height is
reached. Repeat for opposite side of rollers.
FIG. 17
INDEX MARK
INDEX MARK
SCREW
A
A
B
B
STRAIGHT EDGE
Содержание 23-150H
Страница 19: ...19 NOTES Use this section to record maintenance service and any calls to Technical Support ...
Страница 20: ...20 PARTS DIAGRAM CUTTERHEAD ASSEMBLY ...
Страница 22: ...22 PARTS DIAGRAM PARTS DIAGRAM TABLE ASSEMBLY CABINET ASSEMBLY ...
Страница 24: ...24 PARTS DIAGRAM GEARBOX ASSEMBLY DRIVE ROLLER ASSEMBLY ...