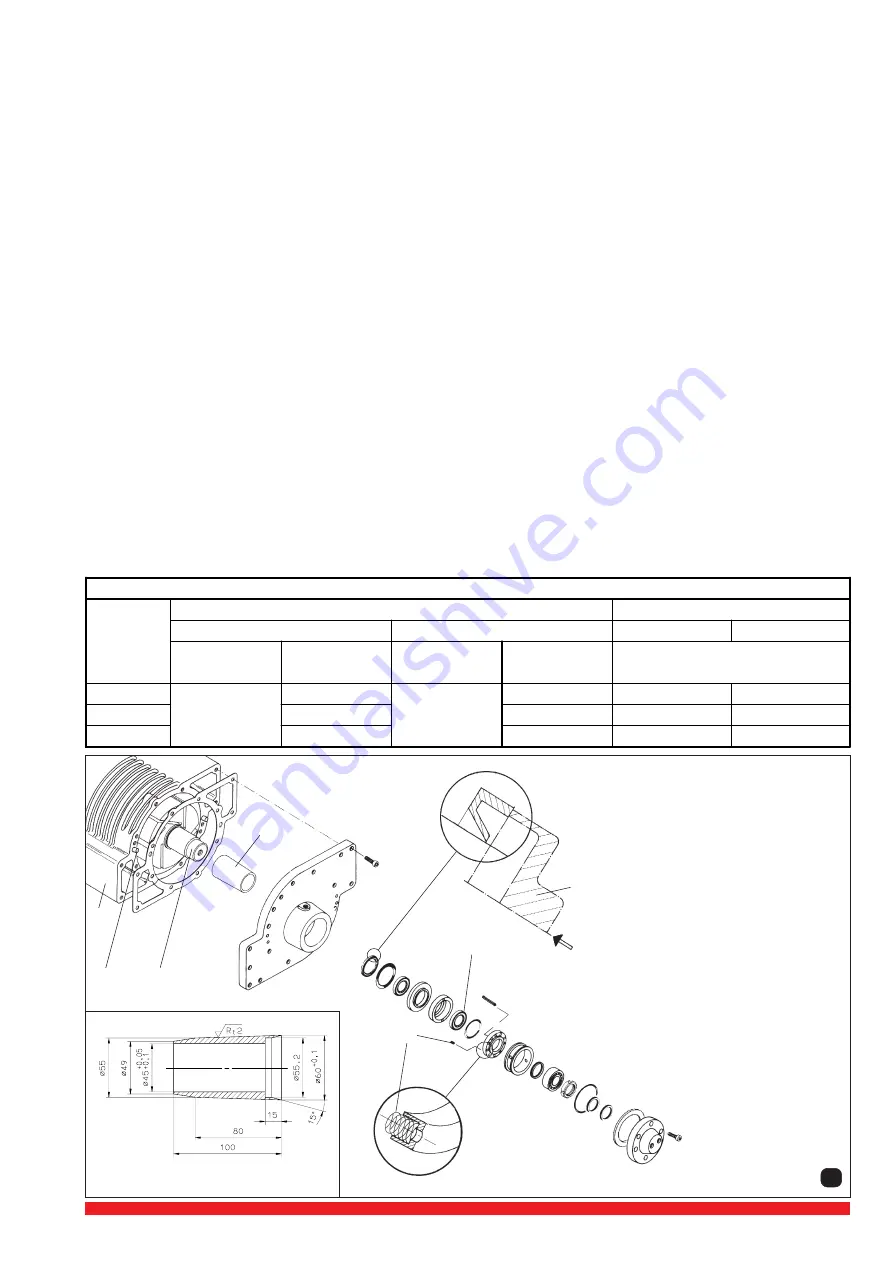
Page 13
5.2 Reassembly of Bearings and Seals (fig. 26)
• Before reassembly all parts should be removed from the end cover (25) or (55).
Check parts (Pos. 10, 11, 12, 13, 14, 15, 17, 23, 28, 48) and if necessary replace.
• Fit new oil seal (10) with assembly device (W
5
) into end cover (sealing lip see fig. 26).
• Place sleeve type I (W
1
) on shaft end (3) or (52) and lightly oil.
• Measure axial clearance between end cover and shaft according to the old seals (9) or (59) or calculate (length of housing
+ seals (9 or 59) - rotor = clearance). The axial clearance is set at works and fixed with dowels. If major work is necessary
on the housing, the tolerance given can be achieved by adjusting and pinning of housing and end cover.
• Important! To ensure correct and safe operation of the pump the data shown in the schedule below must be observed.
Please note different sizes of packing (9) or (59).
• Coat both sides of gasket (9) or (59) with anti-seize non-setting universal jointing material and position on end face of cylinder
housing (1) or (51).
• Push end cover over the dowels (2) and screw down loosely.
• Insert shaft seal (12) with sleeve in wearing disc (11).
• Insert wearing disc (11) together with o-ring (13) in bore of end cover with sleeve type I (W
1
).
• Insert shaft seal (12) with sleeve in sliding ring (15).
• Slightly oil seal surface of wearing disc (11) and sliding ring (15).
• Insert sliding ring (15) up to the wearing disc (11) and pull off sleeve type I (W
1
).
• Slightly oil spring (20) and insert in bore of transporting ring B (17).
• Place the transport ring B (17) over the shaft end, insert sleeves (19) in the bore of the sliding ring (15).
• Place spacer (43) if available next to transport ring B (17).
• Fit spacer ring (14) and bearing (26).
• Fit shaft nut (27) at shaft end (3) or (52) with necessary turning moment.
• Place spacer (42), if required, next to bearing (26).
• Bearing cover (29) with O-ring (23) slip carefully over the shaft and tighten down.
• Tighten end cover and re-connect oil lines.
• Re-fitting of stages and water jacket (see page 12).
Clearance data of stages [mm]
VWZ
Axialspalt
Radial clearance
LP-stage
HP-stage
LP-stage
HP-stage
B-side Fix
clear.
Total
clearance
B-side Fix
clear.
Total
clearance
(between rotor and housing)
702
0.
10
0.
70
0.
10
0.
60
0.20
0.30
1002
0.
90
0.
80
0.20
0.35
1202
0.
90
0.
80
0.20
0.35
26
Sleeve type I
[mm]
13
10
17
43
14
48
19
15
26
27
23
28
42
20
11
25
W
1
9
12
12
29
W
5
1
2
3