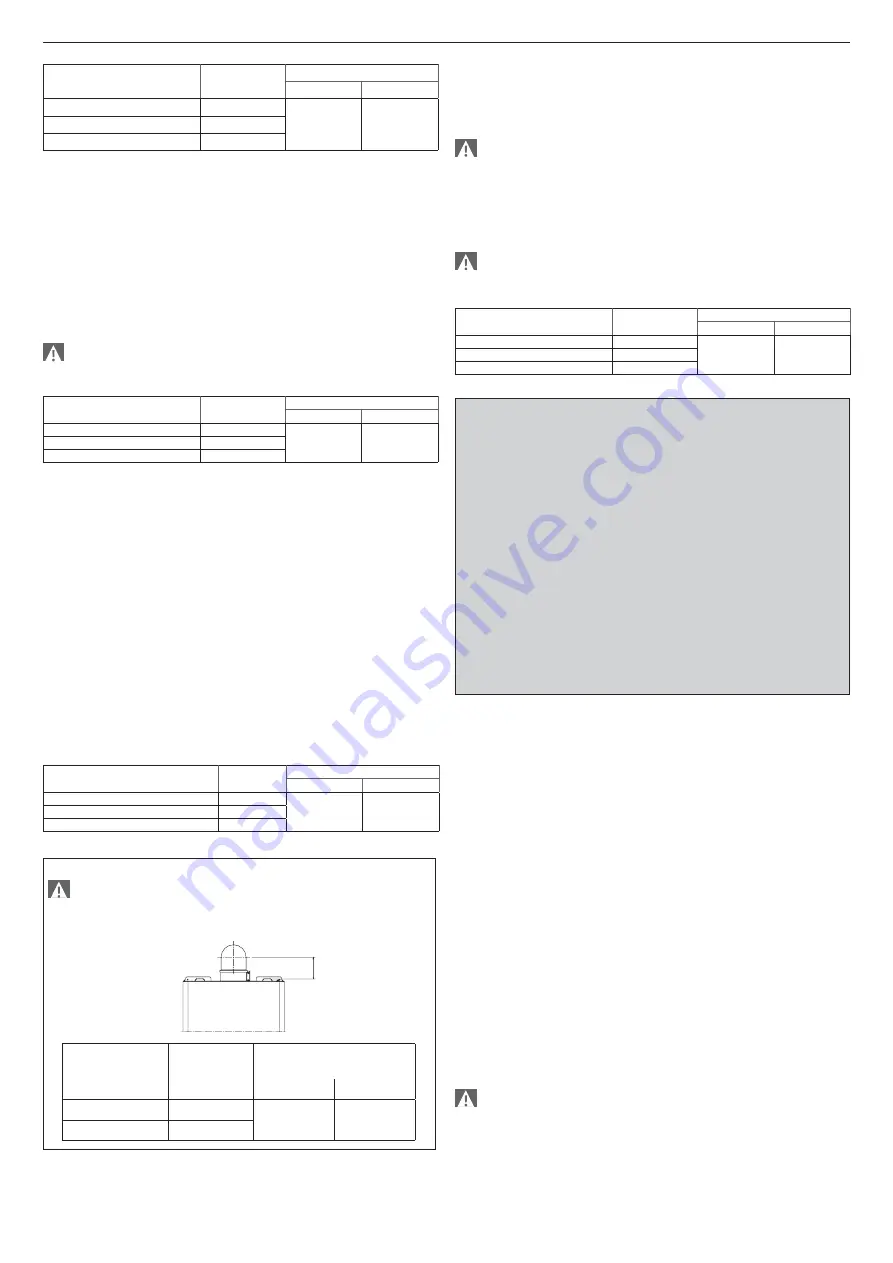
FASTECH KI - KIS
6
(*) fitted in boiler
Max length fumes
outlet duct Ø 80 mm
Flue gas
flange (ø)
Load losses
45° bend
90° bend
up to 2
42
1,2m
1,7m
from 2 to 8
44 (*)
from 8 to 25
not installed
“SEALED” INSTALLATION (TYPE C)
The boiler must be connected to concentric or twin fumes discharge
and air intake ducts which must both be taken outside. Do not use
the boiler without them.
Concentric outlets (ø 60-100, fig. 10d)
The concentric outlets can be placed in the most suitable direction
according to room requirements.
For installation, follow the instructions supplied with the kit.
When necessary, the flue gas flange (
A
), must be removed or replaced
using a screwdriver as a lever.
It is appropriate to install a condensate collector and specific
pipes. In this case realize an inclination of 3° to the condensate
collector.
(*) fitted in boiler
Max linear length concentric
duct Ø 60-100 mm
Flue gas
flange (ø)
Load losses
45° bend
90° bend
up to 0,85
42
1m
1,5m
from 0,85 to 2,35
44 (*)
from 2,35 to 4,25
not installed
Concentric outlets (ø 80-125, fig. 10e)
The boiler has been designed to be connected to concentric outlet/
suction pipes and with the opening for air suction closed.
The concentric outlets can be placed in the most suitable direction
according to room requirements, complying with the maximum lengths
indicated in the table.
For installation, follow the instructions supplied with the kit.
To go through the wall, drill a hole of Ø 130 mm.
According to the length of the pipes used, it is necessary to insert a
flange selecting from those contained in the boiler.
Pay special attention to external temperature and pipe length. Refer
to the diagrams in order to establish if it is compulsory or not to use
a condensation collector. In case of operation at temperature lower
than 60 °C, it is compulsory to use a condensation collector. If a
condensation collector is used, provide a slope of the flue exhaust
pipe of 3° towards the collector.
Connect the condensation trap syphon to a white water outlet pipe.
Non insulated outlet pipes are potential sources of danger.
(*) fitted in boiler
Max linear length concentric
duct Ø 80-125 mm
Flue gas
flange (ø)
Load losses
45° bend
90° bend
from 0,96 to 3,85
42
1,35m
2,2m
from 3,85 to 7,85
44 (*)
from 7,85 to 12,4
not installed
Fastech 24 KIS - reduced concentric bend
86,5
If it is necessary to install the boiler on systems already existing (replacement
types Caldariello KIS), there is a “reduced concentric bend kit” available that
allows positioning the boiler by keeping the same flue gas hole.
Pipe length with
reduced bend
(m)
Flue gas
flange (A)
Load losses fort esch
bend (m)
45°
90°
up to 1,85
Ø 44 (**)
1
1,5
from 1,85 to 4,25
not installed
Twin outlets (ø 80, fig. 10f)
Twin outlets can be placed in the most suitable direction according to
the room requirements.
Remove the closure plug secured with the screws and use the specific
adaptor for the combustion air intake pipe (
E
).
The air inlet adaptor ø 80 (
E
) must be correctly directed, it is
necessary to fasten it with the appropriate screws, so that the
positioning flap does not interfere with the shell.
When necessary, the flue gas flange (
A
), must be removed using a
screwdriver as a lever. The table indicates the permitted linear lengths.
According to the length of the pipes used, it is necessary to insert a
flange, selecting one from those contained in the boiler.
It is appropriate to install a condensate collector and specific
pipes. In this case realize an inclination of 3° to the condensate
collector.
(*) fitted in boiler
Max length
twin duct Ø 80 mm
Flue gas
flange (ø)
Load losses
45° bend
90° bend
up to 2 + 2
42
1,2m
1,7m
from 2 + 2 to 6 + 6
44 (*)
from 6 + 6 to 16 + 16
not installed
POSSIBLE OUTLET CONFIGURATIONS (fig. 10a)
B22P-B52P
Suction indoors and discharge outdoors.
C12-C12x
Discharge via concentric wall outlet. The pipes may
leave the boiler independently, but the outlets must be concentric
or sufficiently close together to be subjected to similar wind condi
-
tions (within 50 cm).
C22
Discharge via concentric outlet in common smoke pipe (suc-
tion and discharge in the same pipe).
C32-C32x
Discharge via concentric roof outlet. Outlets as for C12.
C42-C42x
Discharge and suction in common separate smoke
pipes, but subjected to similar wind conditions.
C52-C52x
Separate discharge and suction lines on wall or roof
and in areas with different pressures. The discharge and suction
lines must never be positioned on opposite walls.
C82-C82x
Discharge via single or common smoke pipe and wall
suction line.
C92-C92x
Discharge on roof (similar to C32) and air suction from
a single existing smoke pipe.
3.11 System filling and emptying
(fig. 11)
Once the hydraulic connections have been made, the system can
be filled.
FILLING
- Open the automatic air vent valve cap by two or three turns (
A
).
- Ensure that the cold water inlet valve is open.
-
Open the filling tap (
B
) until the pressure on the hydrometer is
between 1 and 1.5 bar.
-
Close the filling tap.
NOTE:
air in the boiler is bled automatically via the automatic air vent
valve on the pump. Ensure that the valve of the air vent valve is open.
EMPTYING
Before emptying, disconnect the electric power supply by switching
the main system switch to “OFF”.
Close the cold water inlet valve.
a) Heating system:
- Close all shut-off devices of the heating circuit.
- Connect the pipe supplied as standard to the discharge valve (
C
).
- Loosen the discharge valve (
C
).
b) DHW system:
- Open the hot and cold water utility valves and empty from the
lowest points.
The safety valve outlet (
D
) must be connected to a suitable
disposal system. The manufacturer declines all liability for any
flooding caused by the safety valve.