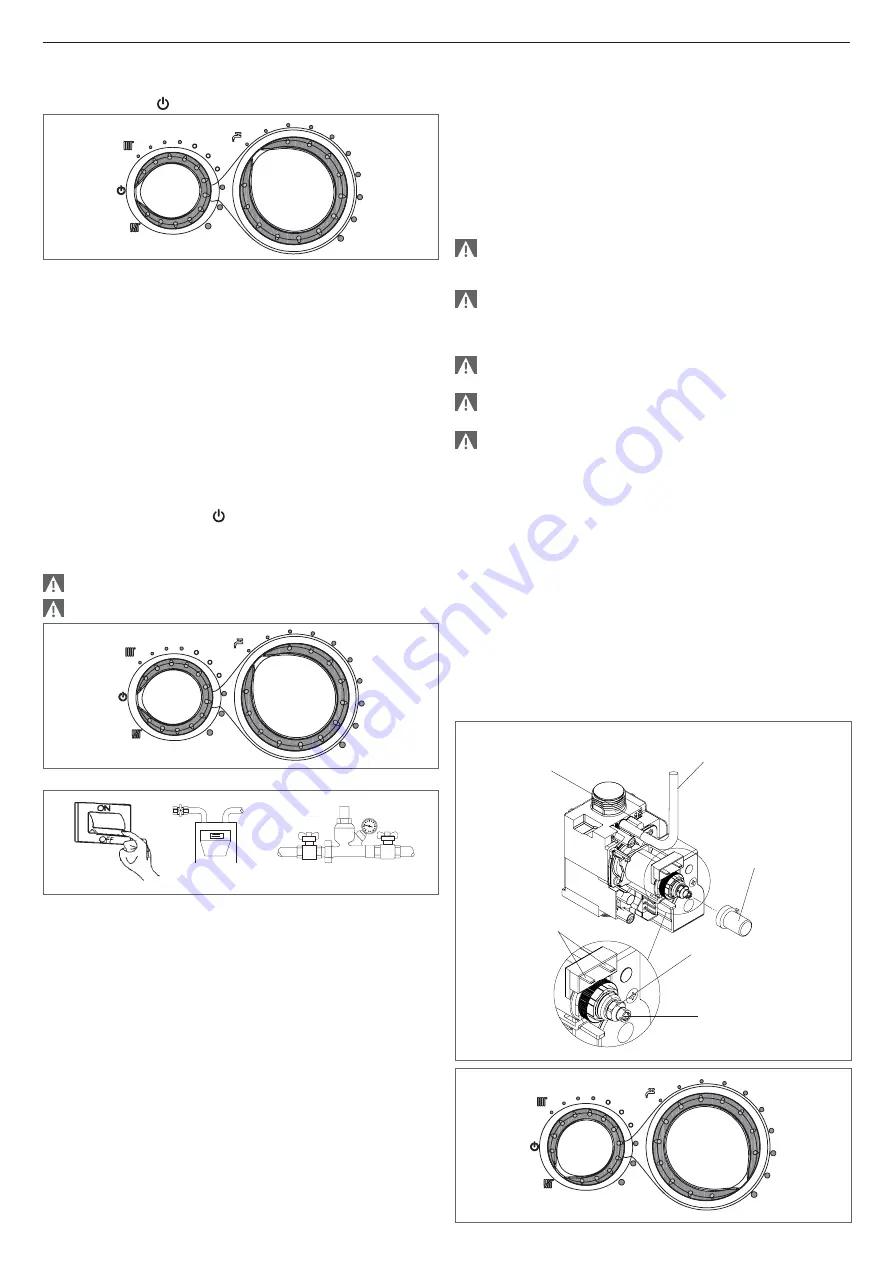
FASTECH KI - KIS
10
4.5
Temporary shutdown
During temporary absences, weekends, short holidays etc., set the
function selector to (OFF).
With the power mains ON and the gas supply active, the boiler is
protected by the systems:
-
Anti-freeze
This function is activated if the boiler water temperature falls below
5°C. The pump runs a 15 minute cycle every 2 hours as follows:
the pump stops when the boiler water temperature exceeds 10°C;
the burner is ignited to the minimum in heating mode when the
boiler water temperature falls below 5°C until the water temperature
reaches 30°C, after which a post-pump phase runs for 30 seconds.
-
Pump anti-block function
The pump is activated every 24 hours of standby and, in any event,
3 hours after the last DHW request.
4.6
Shutdown for long periods
If the
FASTECH
boiler will not be used for a long period of time:
- set the function selector to (OFF-unblock)
- turn the main system switch to “OFF”
- close the heating and domestic hot water system gas and water
cocks.
The anti-freeze and pump anti-block functions are disabled.
Empty the heating and DHW circuit if there is a risk of freezing.
4.7
Maintenance
Periodic maintenance is an “obligation” required by law and is essential
to the safety, efficiency and lifetime of the boiler.
It allows for the reduction of consumption, polluting emissions and
keeping the product reliable over time.
Before starting maintenance operations:
•
Perform the analysis of the combustion products to check the boiler
operation status then cut the electrical supply by turning off the
system’s general switch
•
Close the fuel and water taps of the heating and domestic hot water
system.
The appliance must be systematically controlled at regular intervals
to make sure it works correctly and efficiently and conforms to
legislative provisions in force.
The frequency of controls depends on the conditions of installation and
usage, it being anyhow necessary to have a complete check carried
out by authorized personnel from the Servicing Centre every year.
•
Check and compare the boiler’s performance with the relative
specifications. Any cause of visible deterioration must be immediately
identified and eliminated.
•
Closely inspect the boiler for signs of damages or deterioration,
particularly with the drainage and aspiration system and electrical
apparatus.
•
Check and adjust – where necessary – all the burner’s parameters.
•
Check and adjust – where necessary – the system’s pressure.
•
Analyze combustion. Compare results with the product’s
specification. Any loss in performance must be identified and
corrected by finding and eliminating the cause.
•
Make sure the main heat exchanger is clean and free of any residuals
or obstruction; if necessary clean it.
•
Check and clean – where necessary – the condensation tray to
make sure it works properly.
Always switch off the power to the appliance and close the gas by
the gas cock on the boiler before carrying out any maintenance
and cleaning jobs on the boiler.
After performing the necessary maintenance operations, the
original adjustments must be restored and the combustion
product analysis must be performed to check the correct
operation.
Do not clean the appliance or any latter part with flammable
substances (e.g. petrol, alcohol, etc.).
Do not clean panelling, enamelled and plastic parts with paint
solvents.
Panels must be cleaned with ordinary soap and water only
4.8
Adjustments
FASTECH
boilers are supplied for operation with natural gas and are
factory-set as specified on the technical data plate.
However, if it is necessary to repeat the adjustments, for example
after non-scheduled maintenance, replacing the gas valve or after
conversion from natural gas to LPG, or vice versa, proceed as
described below.
The minimum and maximum output and the maximum heating settings
must be set in the specified sequence and exclusively by qualified
technicians.
- Turn the main system switch to “OFF”.
-
Remove the case unscrewing the fixing screw.
- Unscrew the panel screw and turn the control panel forwards.
- Unscrew the tapping point screw downstream of the gas valve by
approximately two turns and connect a pressure gauge.
- Disconnect the compensation tube from the air chamber (only KIS
model).
Compensation
tube
Pressure
tapping point
downstream of
gas valve
Protection
cap
Maximum output adjust-
ment nut
Minimum DHW
adjustment Allen screw
Faston
connectors