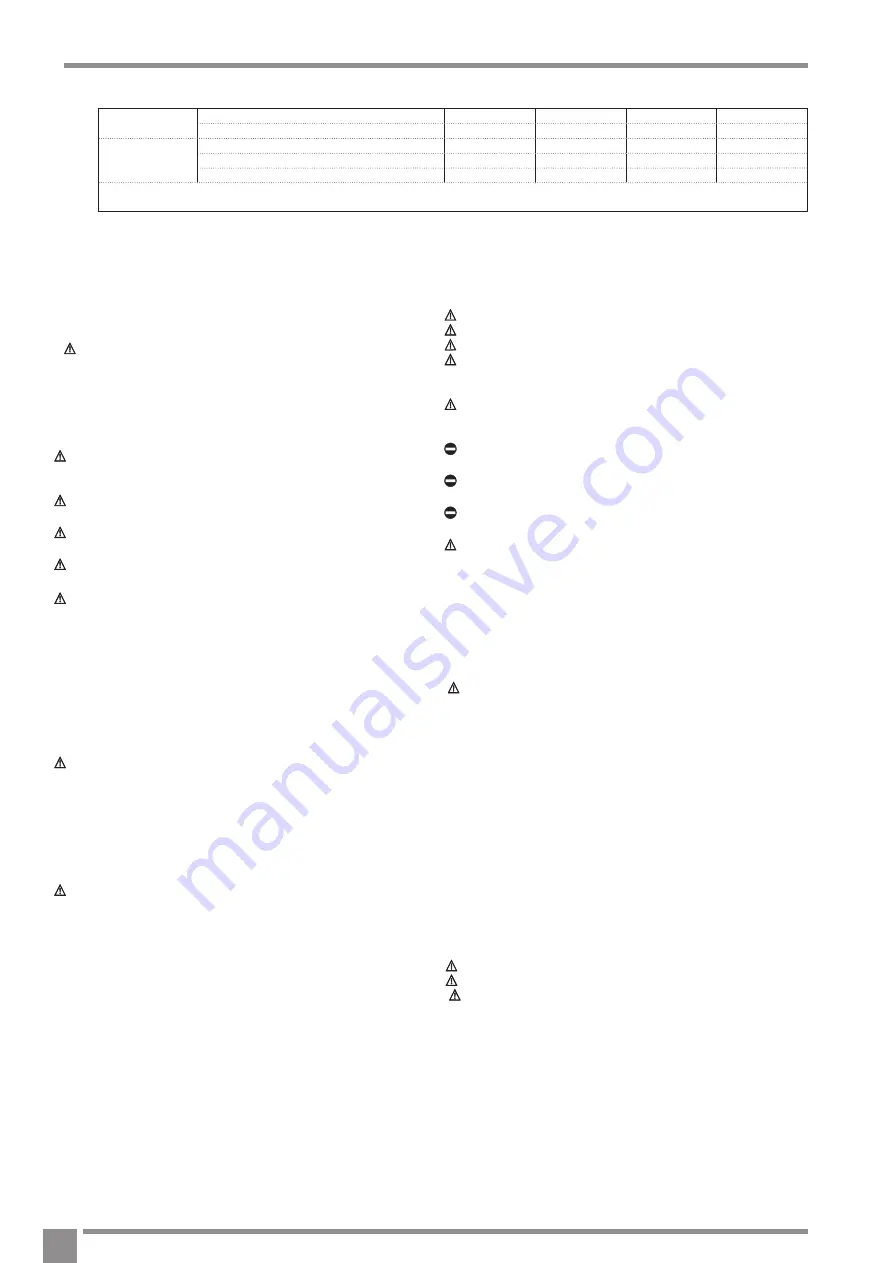
System’s drainage
- Position the system’s main switch in the “off” position.
- Check that the system’s charging tap is closed.
- Open the water discharge tap outside the machine.
Any antifreeze liquid contained in the system should not be discharged
freely as it is a pollutant.
Ordinary maintenance
Preliminary instructions
Regular maintenance is essential in order to keep the unit in top
condition, and must be carried out at least once a year by the Technical
Service or by skilled technicians.
Plan the maintenance schedule according to the characteristics of
installation and the use of the unit.
For units installed in a seaside environment, the maintenance intervals
shall be halved.
After carrying out the necessary maintenance actions, the original
conditions must be restored.
Do not open the access covers and carry out technical or cleaning
activities before disconnecting the unit from the power grid by
positioning the system’s main switch in the “off” position.
Cleaning
Do not open the access covers and carry out technical or cleaning
activities before disconnecting the unit from the power grid by
positioning the system’s main switch in the “off” position.
- The only necessary cleaning activity to be carried out by the system’s
user concerns the unit’s external cabinet, which must be cleaned using
exclusively a cloth wet with soapy water.
- In case of tough stains, wet the cloth with a mix of 50% water and
denatured alcohol or with specific detergents.
- After washing, dry the surfaces carefully.
Do not use sponges with scouring products or powdered detergents.
Operations
The annual maintenance plan includes the following checks:
Mesh filter cleaning
Supply voltage
Fastening of electric connections
Status of the hydraulic joints
Water circuit charging
Pump operation check
Presence of air in the hydraulic circuit
Safeties efficiency
Compressor’s remote control switch status
Plate heat exchanger’s resistor efficiency
Compressor’s resistor efficiency
Cleaning of fan grids
Preliminary instructions
Check that the main power supply line is disconnected.
Use tools appropriate for the refrigerant used.
It is strongly suggested to use safety goggles and gloves.
In case of partial leak of refrigerant gas, the circuit must be completely
emptied before being recharged, and the refrigerant must be
recovered.
Any gas leaks indoors can generate toxic gases if they come into
contact with naked flames or high temperature bodies, in case of
leaks, please air the rooms thoroughly.
Do not charge the refrigerating circuits with a different refrigerant from
the prescribed one.
Do not use oils that are different from the prescribed one. The use of
different oils may seriously damage the compressor.
Do not use oxygen or acetylene or other flammable or poisonous
gases in the refrigerating circuit, as they can cause explosions.
Operating conditions different from the nominal ones may yield values
that differ considerably.
Compressor
The compressor is installed on the unit already charged with oil and
sealed.
In case of breakages, if the compressor can be repaired, use only original
ester oil. The oil used in the compressor is ESTER OIL VG74 (VG68 for
the 12kW).
Do not use oils that are different from the prescribed one. The use of
different oils may seriously damage the compressor.
Extraordinary maintenance
% Inhibited ethylene glycol
10%
20%
30%
40%
Freezing temperature (*)
-4°C
-9°C
-15°C
-23°C
Correction factor
Capacity
0,996
0,991
0,983
0,974
Input power
0,990
0,978
0,964
1,008
Pressure drop
1,003
1,010
1,020
1,033
(*) Note : the temperature values are approximate
Always refer to the temperature values indicated for the specific model
Refrigerant charge
Proceed as follows:
Empty and dry the whole refrigerating circuit using a vacuum pump
connected to the low pressure port, until the value displayed on the
vacuum gauge is about 10 Pa.
Wait for a few minutes and check that said value does not go up
again.
Connect the refrigerant gas cylinder or a charging cylinder to the low
pressure line port (the charge connection position can be seen on the
refrigerant circuit diagram).
Charge the required quantity of refrigerant gas, as shown in the unit’s
technical tag
In case of a partial leak, the circuit must be completely emptied before
being recharged.
The refrigerant must be charged into the unit only in its liquid state.
Do not use refrigerants and lubricants different from those specified.
Do not compress the air (Avoid the presence of air, caused by leaks,
in the refrigerant circuit).
Always check the overheating and undercooling values which, in the unit’s
nominal operating conditions, must fall between 5 and 10° C in the refri-
gerators and 4 and 8°C in the heat pumps, respectively.
Once the appliance has been serviced, the benchmark Service Record
must be completed.
For UK only: It is important that the Benchmark Service Record is correctly
completed and handed to the user. Failure to install and commission the
appliance to the manufacturers instructions will invalidate the warranty.
26