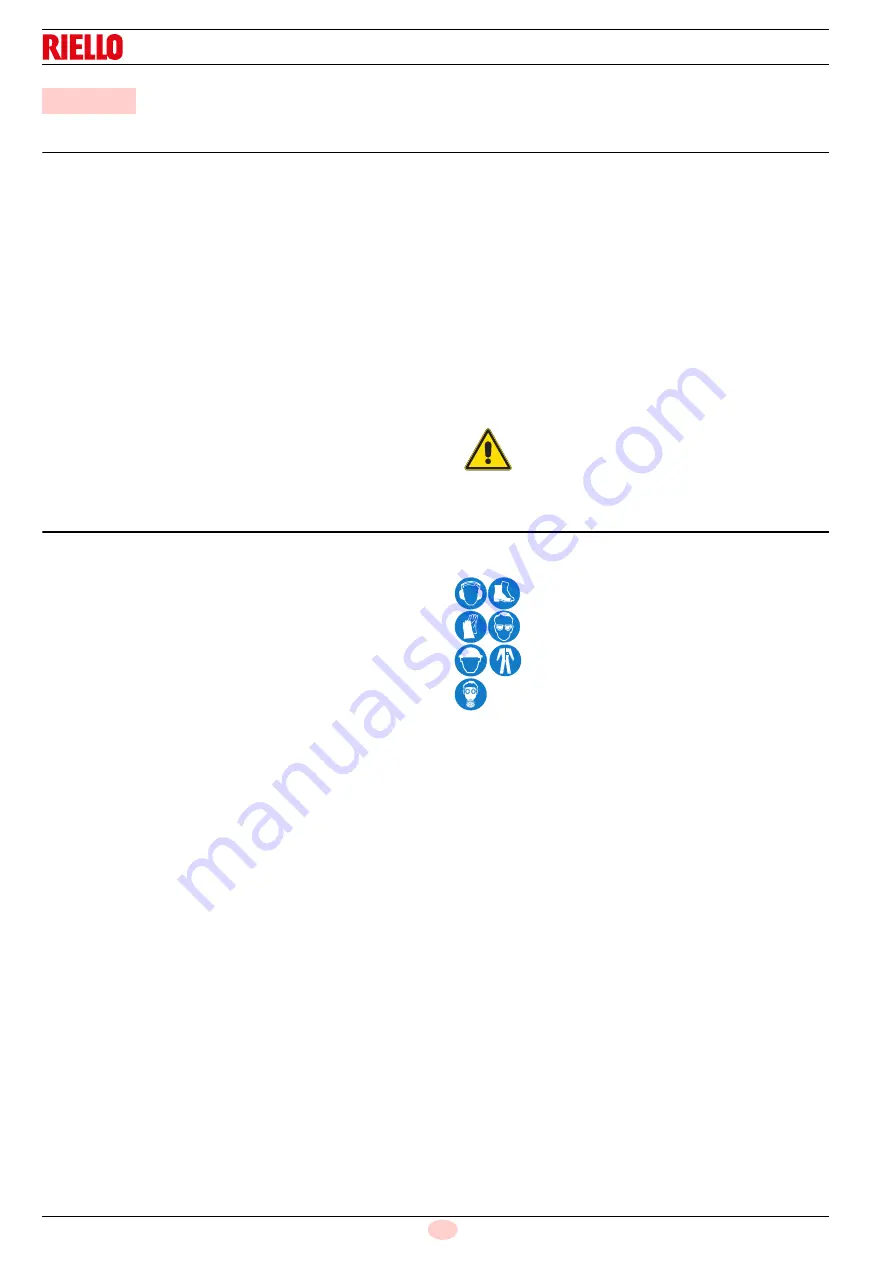
20163413
6
GB
Safety and prevention
3.1
Introduction
The burners have been designed and built in compliance with
current regulations and directives, applying the known technical
rules of safety and envisaging all the potential danger situations.
It is necessary, however, to bear in mind that the imprudent and
clumsy use of the equipment may lead to situations of death risk
for the user or third parties, as well as the damaging of the burner
or other items. Inattention, thoughtlessness and excessive confi-
dence often cause accidents; the same applies to tiredness and
sleepiness.
It is a good idea to remember the following:
The burner must only be used as expressly described. Any
other use should be considered improper and therefore dan-
gerous.
In particular:
it can be applied to boilers operating with water, steam, diather-
mic oil, and to other users expressly named by the manufacturer;
the type and pressure of the fuel, the voltage and frequency of the
electrical power supply, the minimum and maximum deliveries for
which the burner has been regulated, the pressurisation of the
combustion chamber, the dimensions of the combustion cham-
ber and the room temperature must all be within the values indi-
cated in the instruction manual.
Modification of the burner to alter its performance and desti-
nations is not allowed.
The burner must be used in exemplary technical safety con-
ditions. Any disturbances that could compromise safety must
be quickly eliminated.
Opening or tampering with the burner components is not
allowed, apart from the parts requiring maintenance.
Only those parts envisaged by the manufacturer can be
replaced.
3.2
Personnel training
The user is the person, body or company that has acquired the
machine and intends to use it for the specific purpose. He is re-
sponsible for the machine and for the training of the people work-
ing around it.
The user:
undertakes to entrust the machine exclusively to suitably
trained and qualified personnel;
undertakes to inform his personnel in a suitable way about
the application and observance of the safety instructions.
With that aim, he undertakes to ensure that everyone knows
the use and safety instructions for his own duties;
Personnel must observe all the danger and caution indica-
tions shown on the machine.
Personnel must not carry out, on their own initiative, opera-
tions or interventions that are not within their province.
Personnel must inform their superiors of every problem or
dangerous situation that may arise.
The assembly of parts of other makes, or any modifications,
can alter the characteristics of the machine and hence com-
promise operating safety. The manufacturer therefore
declines any and every responsibility for any damage that
may be caused by the use of non-original parts.
In addition:
3
Safety and prevention
WARNING
The manufacturer guarantees safety and proper
functioning only if all burner components are intact
and positioned correctly.
the user must take all the measures neces-
sary to prevent unauthorised people gaining
access to the machine;
the user must inform the manufacturer if
faults or malfunctioning of the accident pre-
vention systems are noticed, along with any
presumed danger situation.
Personnel must always use the personal pro-
tective equipment envisaged by legislation
and follow the indications given in this man-
ual.
Содержание 20155875
Страница 2: ...Translation of the original instructions...
Страница 43: ...41 20163413 GB Appendix Electrical panel layout...
Страница 44: ...20163413 42 GB Appendix Electrical panel layout 0 0 1 0 1 2 0 3 0 1 0 1 1 0 0 0 0 0 40 4 4 0 0 1 2 0 1...
Страница 45: ...43 20163413 GB Appendix Electrical panel layout 0...
Страница 47: ...45 20163413 GB Appendix Electrical panel layout 0 0 1 2 2 2 2 2 2 2 0 0 2 0 2 0 1 2...
Страница 48: ...20163413 46 GB Appendix Electrical panel layout 0 1 2 1 3 4 56 4 6 4 6 5 4 786 9 3 1 2 78 0 0 2 2 2...