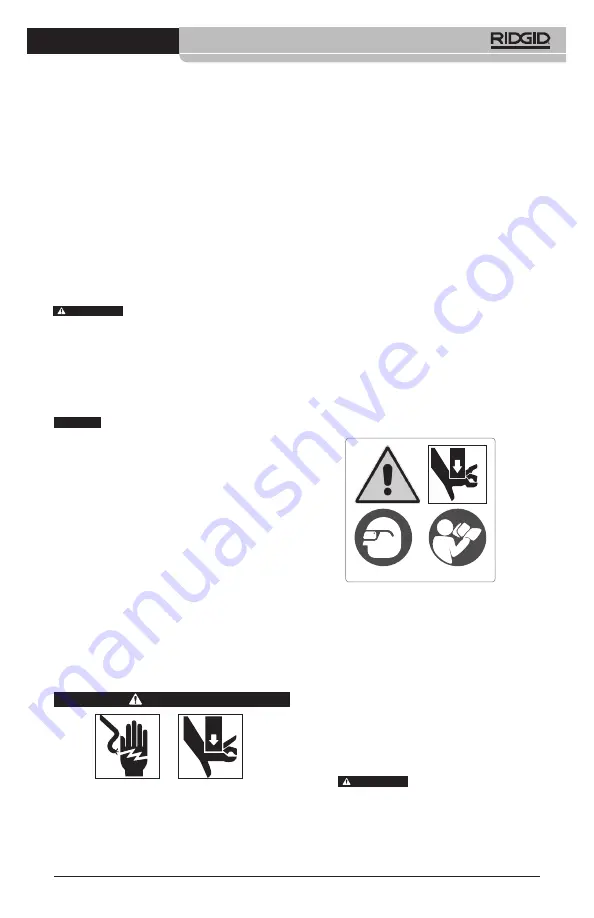
1. Remove battery from tool.
2. Clean any oil, grease or dirt from the
equipment, especially the handles and
controls. This aids inspection and helps
to prevent the tool or controls from slip-
ping from your grip.
3. Inspect the press tool for:
• Proper assembly, maintenance and
completeness.
• Any broken, worn, missing, misaligned
or binding parts. Confirm fabric loops
are in good condition.
• Smooth movement of attachment
mounting pin between the fully open
and fully closed position. Pin should
lock into each position. Confirm that
the run switch moves freely and does
not bind or stick.
• Presence and readability of warning
label
(Figure 1 or 6)
.
• Any other condition which may prevent
safe and normal operation.
Do not use the press tool until problems
have been repaired.
Figure 6 – Warning Label
4. Inspect the attachments:
• Closely inspect all attachments for any
cracked, broken, worn, missing, mis-
aligned or binding parts or any other
sign of damage that may prevent prop-
er and safe operation. Damaged parts
can cause the attachment to make
incorrect pressed connections or fail
during use and cause serious injury
or property damage. If any damage is
found, the attachment should be dis-
carded and replaced.
Always discard the com-
plete pressing attachment. Never re-
place individual components or ex-
change parts between assemblies.
Failure to replace the entire assembly
may result in component failure and
serious injury.
- Vibration levels may be used for comparison with
other tools and for preliminary assessment of expo-
sure.
- Sound and vibration emissions may vary due to your
location and specific use of these tools.
- Daily exposure levels for sound and vibration need
to be evaluated for each application and appropriate
safety measures taken when needed. Evaluation of
exposure levels should consider the time a tool is
switched OFF and not in use. This may significant-
ly reduce the exposure level over the total working
period.
# All specifications are nominal and may change as
design improvements occur.
Standard Equipment
Refer to the RIDGID catalog for details on
equipment supplied with specific tool cata-
log numbers.
Only use RIDGID Press Tools
and RIDGID press tool attachments when
specified by the fitting manufacturer for use
with their system. Use of incorrect press tools
and/or attachments for a system can cause
system leaks, damage the press tool or
attachment, void warranties or cause severe
personal injury.
Selection of a appropriate materi-
als and joining methods is the responsibil-
ity of the system designer and/or installer.
Before any installation is attempted, careful
evaluation of the specific service environ-
ment, including chemical environment and
service temperature, should be completed.
Consult Press Fitting System manufacturer
for selection information.
Contact the fitting manufacturer for specific
information on their system, including com-
patible tubing, materials, installation instruc-
tions, minimum distance between fittings,
seal material, inspection, testing, etc. Incor-
rect installation can cause system leaks and
extensive property damage.
Pre-Operation
Inspection
WARNING
Daily before use, inspect your press tool
and attachments. Correct any problems
to reduce the risk of serious injury from
electric shock, crushing injures, attach-
ment failure and other causes, and pre-
vent tool damage.
999-995-408.10_REV. A
7
RP 115 Press Tool
NOTICE
WARNING
HE.20079
WARNING