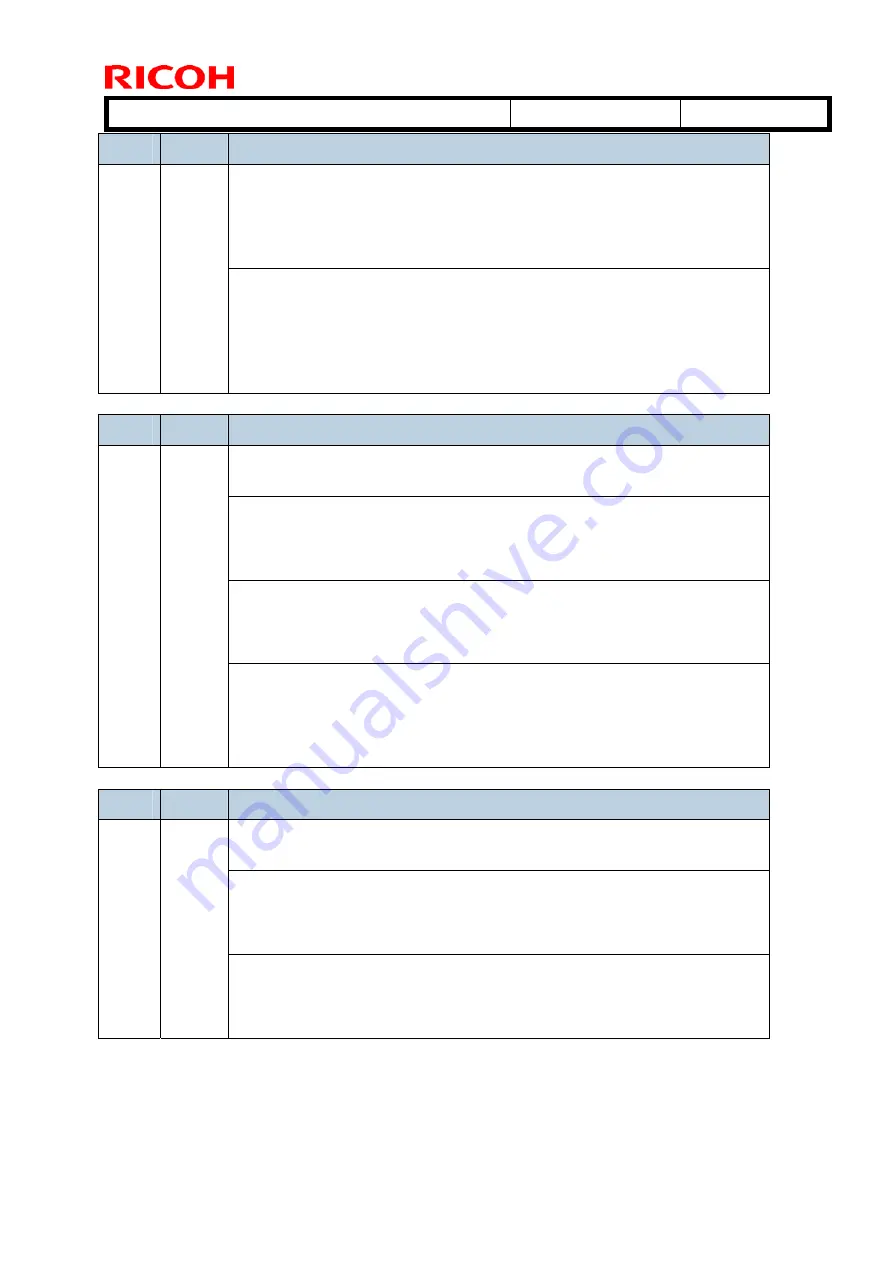
T
echnical
B
ulletin
PAGE: 38/44
Model:
Aries-P1.5/C1.5
Date:
17-Feb-11
No.:
RM077018
No.
Type
Details (Symptom, Possible Cause, Troubleshooting Procedures)
Motor overload
Loose connection of the stapler home position sensor
Loose connection of the stapler movement motor
Defective stapler home position sensor
Defective stapler movement motor
203. Check or clear obstacles around the motor drive
mechanism.
204. Check the harness connection.
205. Replace the stapler home position sensor.
206. Replace the stapler movement motor.
207. Replace the finisher main board.
No.
Type
Details (Symptom, Possible Cause, Troubleshooting Procedures)
Booklet Stapler Motor Error 1: Front Motor (Booklet Finisher
D434
)
The booklet stapler - front does not start operation within the
specified time.
The 1st detection failure issues a jam error, and the 2nd failure
issues this SC code.
Booklet stapler motor (front) harness loose, broken, defective
Booklet stapler motor (front) overloaded due to obstruction
Booklet stapler motor (front) defective
Booklet finisher control board defective
743 B
208. Check or clear obstacles around the motor drive
mechanism.
209. Check the harness connection.
210. Replace the booklet stapler motor - front.
211. Replace the finisher main board.
No.
Type
Details (Symptom, Possible Cause, Troubleshooting Procedures)
Booklet Stapler Motor Error 2: Rear Motor (Booklet Finisher
D434
)
The booklet stapler - rear does not start operation within the
specified time.
The 1st detection failure issues a jam error, and the 2nd failure
issues this SC code.
744 B
Booklet stapler motor (rear) harness loose, broken, defective
Booklet stapler motor (rear) overloaded due to obstruction
Booklet stapler motor (rear) defective
Booklet finisher control board defective
Содержание pro c901
Страница 38: ...Technical Bulletin PAGE 2 44 Model Aries P1 5 C1 5 Date 17 Feb 11 No RM077018 Correction Page 117 to 131...
Страница 50: ...Technical Bulletin PAGE 14 44 Model Aries P1 5 C1 5 Date 17 Feb 11 No RM077018 Page 133 to 149...
Страница 63: ...Technical Bulletin PAGE 27 44 Model Aries P1 5 C1 5 Date 17 Feb 11 No RM077018 Page 182 to 203...
Страница 101: ...Technical Bulletin PAGE 21 28 Reissued 07 Aug 2012 Model Aries P1 5 C1 5 Date 18 Feb 11 No RM077019g Appendixes...
Страница 132: ...Technical Bulletin PAGE 2 3 Reissued 15 Jun 11 Model Aries P1 5 C1 5 Date 12 May 11 No RM077028a Victoria...
Страница 133: ...Technical Bulletin PAGE 3 3 Reissued 15 Jun 11 Model Aries P1 5 C1 5 Date 12 May 11 No RM077028a Columbia...
Страница 266: ...Technical Bulletin PAGE 2 2 Model Aries P1 5 C1 5 Date 26 Jan 12 No RM077059...
Страница 290: ...Technical Bulletin PAGE 2 2 Model Aries P1 5 C1 5 Date 13 Feb 12 No RM077064...
Страница 441: ...Technical Bulletin PAGE 2 2 Model Aries P1 5 Date 12 Dec 13 No RM077101...
Страница 549: ...Technical Bulletin PAGE 5 35 Reissued 6 Jun 15 Model Aries C1 5 P1 5 D095 M077 Date 17 Jun 14 No RM077114a...