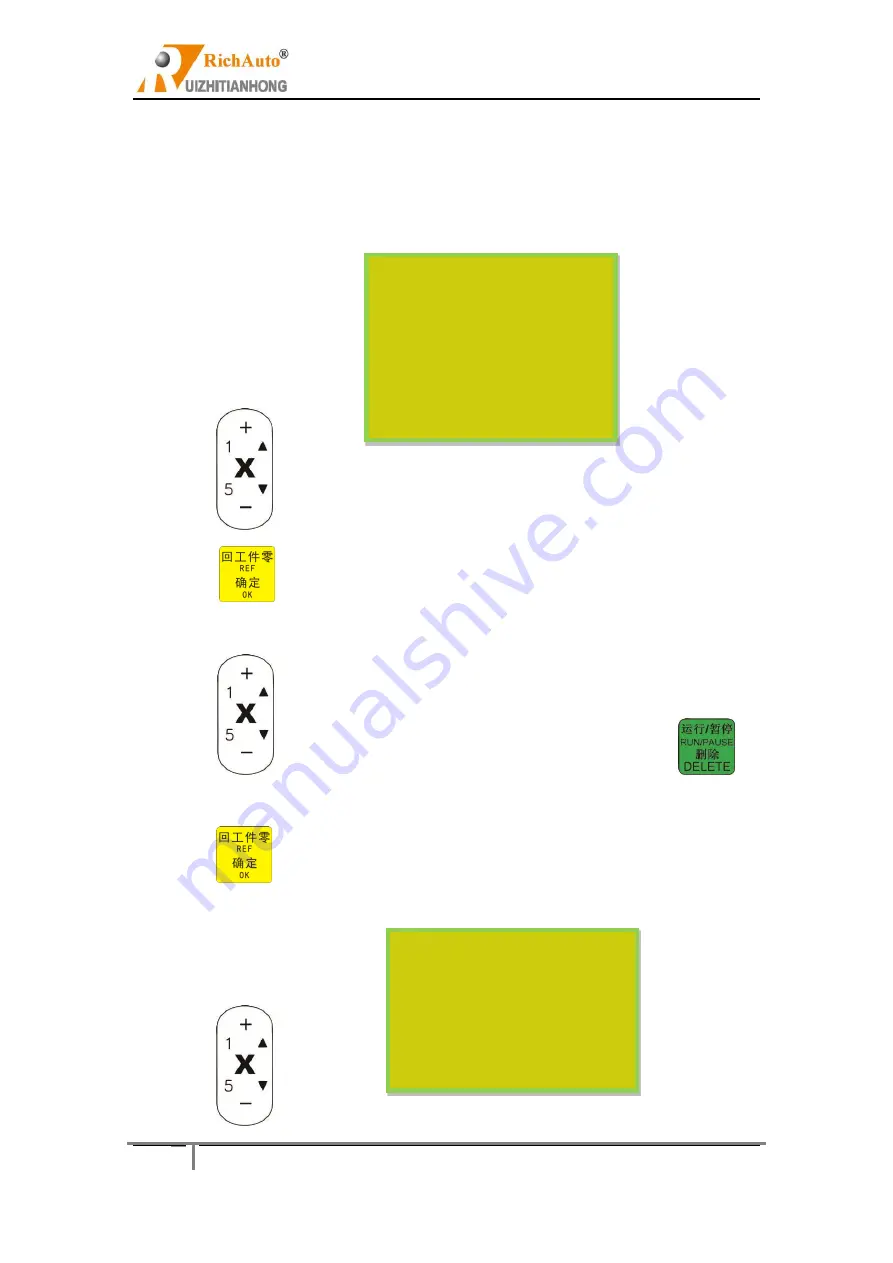
北京锐志天宏科技股份有限公司
Beijing RichAuto S&T Co., Ltd
Forging ahead, create future together!
48
5.7.3
Mill Plane
Include two types: scan mill and encircle mill.
Rectangle Mill
1)
Press “
”to move cursor to choose the mill type.
2)
Press “
” to enter the scan mill set, it includes: Scan type, Width, Height,
Diameter, Depth, Z Step, T Ratio.
3)
Press “
”to move cursor on the option which need modify, press “
” to
choose mill type(X Scan or Y Scan), also press this button to modify the parameters.
Press “
” after modified all the parameters to save them.
Circular Mill
1)
Press “
”to move cursor to choose the mill type.
Mill Plane Param
X Mill 100
Y Mill 100
Depth 5
Layer D 2
Dia
10
Plunge R 0.800
Mill Plane Param
Mill RAD 50
Depth 5
Layer D 2
Dia 10
Plunge R 0.800