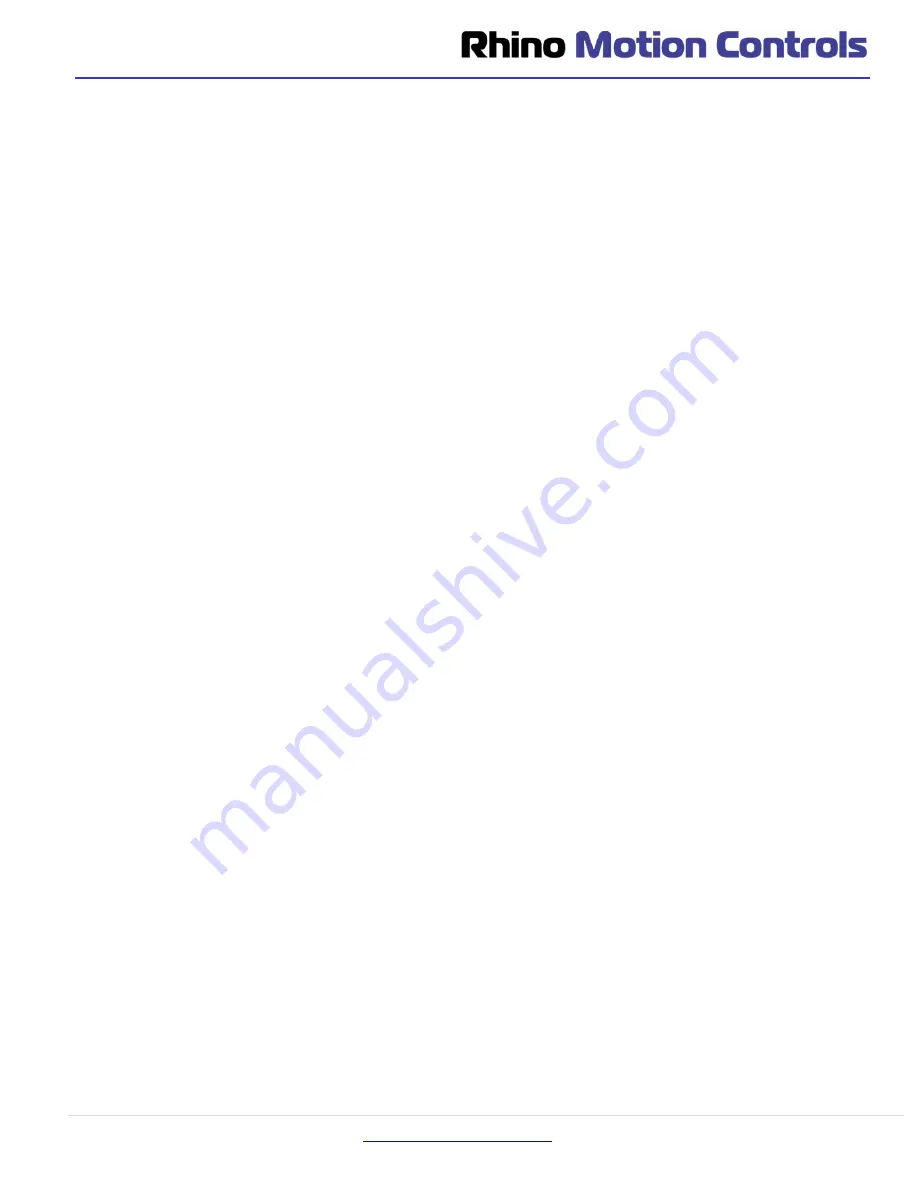
11 |
P a g e
Mode 0 Analog Open Loop Mode:
a. In this mode the speed of the Rhino BLDC motor can be controlled by using Potentiometer which is available at the
corner side of drive.
b. User can increase or decrease the speed manually based on requirement by using Potentiometer.
c.
The drive will provide full torque at all speeds within the range.
d. Also the Enable, Brake and Direction Inputs are available in this drive for this mode.
e. Need to connect Enable pin with 5V to run motor in analog control mode.
f.
Direction and brake can only be applied by connecting DIR or BRK pin to 5V.
Mode 1 Digital Closed Loop Mode:
a. In this mode the speed and direction of the Rhino BLDC Motor is settable / controllable via a Computer / Arduino
Controller board / any other Modbus RTU compatible device.
b. As in the analog mode here there is no compromise in the torque output of the motor irrespective of the operational
speed and voltage supply and control at higher speeds.
c.
This mode is used when multiple motors are to be used to run at exactly the same RPM and same torque.
d. Also in this mode the direction of the motor can be controlled digitally via modbus RTU commands to run the BLDC
motor in both directions
e. For industrial applications, brushless DC motors are primarily used in servo, actuation, positioning, and variable
speed applications where precise motion control and stable operation are critical for the satisfactory operation of the
manufacturing or industrial process. They are commonly used as: Linear motors, Servomotors, Actuators for
industrial robots, Extruder drive motors, Feed drives for CNC machine tools.
Mode 2 Digital Open Loop Mode:
a. In this mode user can increase or decrease speed of motor as per PWM setting.
b. This mode is PWM Controlled Mode.
c.
The use of pulse width modulation (PWM) to control a small motor has the advantage in that the power loss in the
switching transistor is small because the transistor is either fully “ON” or fully “OFF”.
d. As a result the switching transistor has a much reduced power dissipation giving it a linear type of control which
results in better speed stability.
e. Pulse width modulation is a great method of controlling the amount of power delivered to a load without dissipating
any wasted power.
Mode 3: Analog Closed Loop Mode:
a. In this mode the speed of the Rhino BLDC motor can be controlled by connected Potentiometer.
b. As this is closed loop mode no need to connect enable pin to 5v.
c.
The drive will provide full torque at all speeds within the range.
d. Brake can be applied through software setting.
e. Direction cannot be changed in this mode.
Mode 4: Analog Closed Loop Minimum Speed Control Mode:
a. In this mode user can set the
minimum speed
of the motor by software setting and the set speed will affect in analog
mode.
b. Basically user can define minimum speed of motor in this mode.
c.
The drive will provide full torque at all speeds within the range.
d. Direction cannot be changed in this mode.
Содержание RMCS - 3001
Страница 10: ...10 P a g e https www robokits co in...