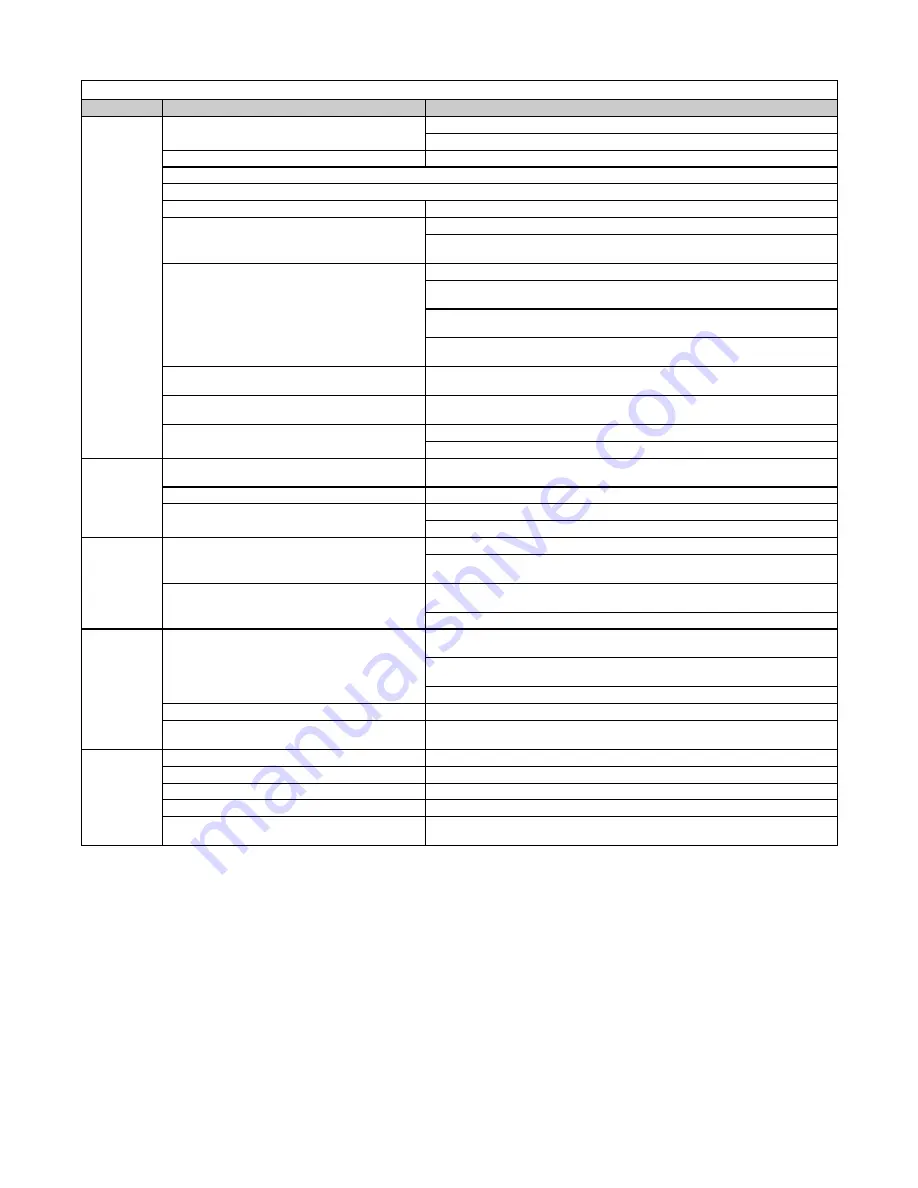
I-OH (01-20) PN120390R7
33
Table 14. Oil Burner Troubleshooting
Symptom
Probable Cause
Remedy
Burner motor
operates and
delivers oil
but there is
no flame
1. No spark
Check transformer, insulators, and electrodes
Transformer/ignition problems may be due to following causes:
a) Excessive gap on ignition electrodes
Ensure that gap is 1/8 inch
b) High ambient temperatures
c) High humidity
d) Carbon residue on the porcelain bushings Clean porcelain bushings
e) Low input line voltage
Measure voltage between transformer/primary lead and neutral connection
NOTE: The secondary terminals of a good transformer deliver 5000V
arc to ground for a total of 10,000V between the terminals.
f) Arcing between ignition electrodes and
transformer springs
Ensure that ignition electrodes and transformer springs have good contact
Measure arc with transformer tester or use well-insulated screwdriver to
draw arc across two springs; ensure that arc is at least 3/4 inch long
Check each secondary output terminal by drawing strong arc between
spring and base
If arc is erratic, weak, or unbalanced between two terminals, replace
transformer
g) Carbon residue, moisture, crazing, or pin
holes on insulators
Clean any carbon residue and replace any insulators that are questionable
h) Improper positioning of nozzle in relation
to radius of endcone
Check and correct nozzle position as necessary
i) Carbon residue on electrode parts
Clean any carbon residue
Replace electrodes when tips become worn or eroded
Burner starts
but flame
blows away
from nozzle
1. Excessive combustion air
Adjust air band and air shutter in accordance with
section
2. Excessive draft
Adjust draft regulator for 0.01 IN WC overfire draft
3. Poor atomization of oil
Adjust fuel feed pressure
Replace oil nozzle as necessary
Poor light
off and shut
down
1. Air pocket between pressure shutdown valve
and nozzle
Tighten unused intake port plug in fuel pump
Run burner, stopping and starting occasionally until pulsation, smoke, and
after-flame disappear
2. Insufficient draft over fire
Check venting for excessive length, insufficient pitch upward to chimney,
too many elbows, obstructed chimney, or too small chimney
Check for too high combustion air setting
Noise
1. Noisy motor
Check for alignment of shaft with coupling and tighten or slightly loosen
motor-to-burner-housing bolts in alternate sequence
Check for loose blower wheel, excessive radial shaft play, and loose start
switch parts
Check if thermocouple is laying on blower wheel
2. Clogged strainer
Remove and clean strainer
3. Burner vibrations transmitted through rigid
electrical conduit or oil lines
Ensure that tubing or conduit is not fastened to studs or beams so securely
that vibration is transmitted to floor or roof
Oil Odors
1. Oil leak(s)
Check fittings and valve seals
2. Poor burner shutoff
Check fuel shutoff valve and time delay relay
3. Smoky flame
Check nozzle spray, air gap, and air shutter setting
4. Oil carbonization on burner endcone
Check nozzle location relative to inside radius of endcone
5. Downdraft causing smoke to enter building
through barometric draft regulator
Increase draft by extending chimney height or by adding ventilating cap or
draft inducer
—Continued