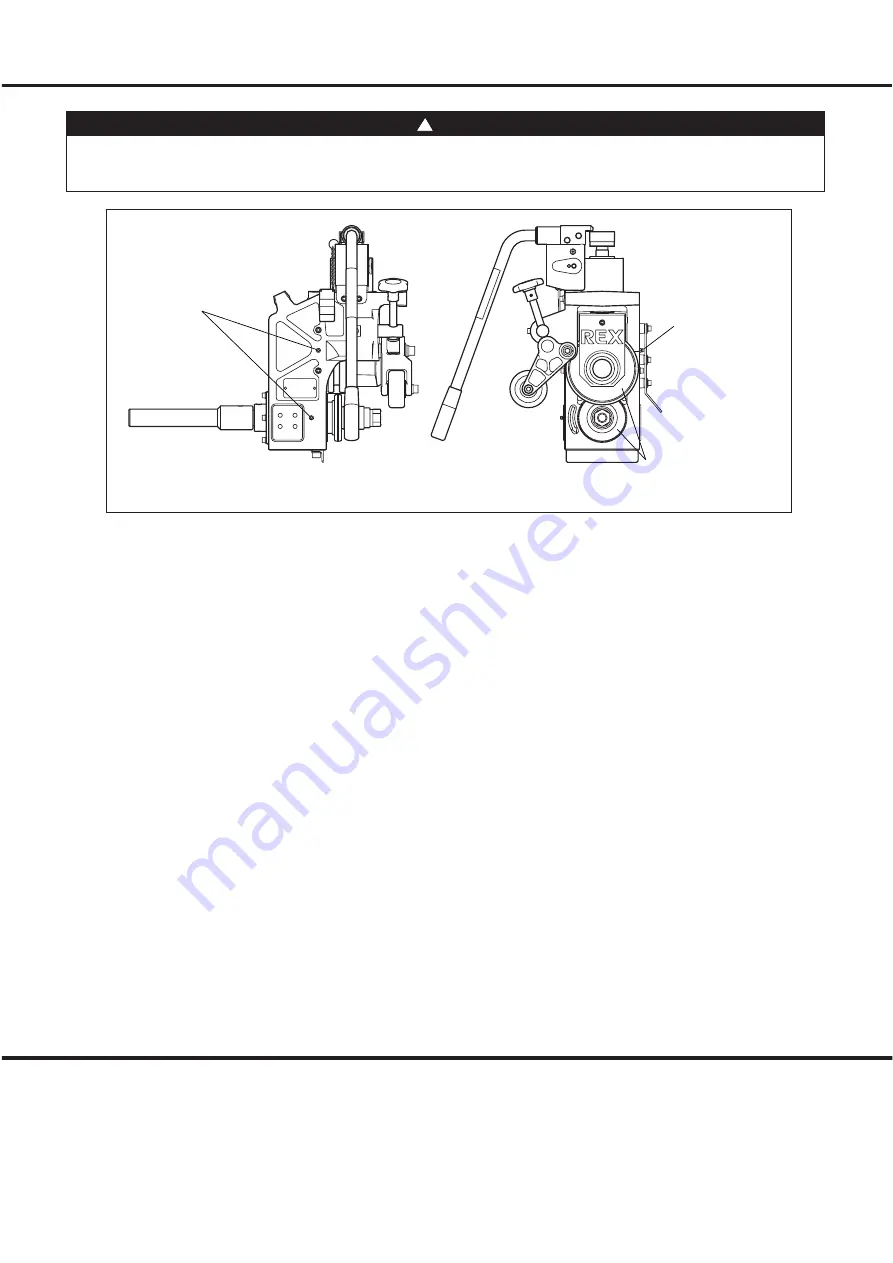
- 15 -
7. Daily inspection, maintenance
㧍
WARNING
8. Requesting repairs
Fig. 28
A. Overall inspection
1) Inspect the fitting screws (A)
ޓޓ
Inspect screws and nuts on each part of the machine, and retighten if loose.
ޓޓ
Among other things, check the screws on the upper roller and the nuts on the lower roller.
If the screws are loose, the roller will be damaged.
ޓޓ
Check that the screws on the mount kit are tightly fastened.
2) Inspect the threading machine's electrical connections and cables (B)
ޓޓ
Check for damage to the plug and power cord, and replace if necessary.
ޓޓ
To prevent electrical leakage and shock, ensure the machine is properly grounded.
3) Inspect the rollers (C)
ޓޓ
Check that the rollers match the type of pipe being processed or normal grooving will not be possible.
ޓޓ
Check for chips or cracks in the rollers. If they are damaged or broken, they will not perform correctly
ޓޓ
ޓ
and the machine will be damaged. Replace them if necessary.
4) Periodical lubrication (C)
ޓޓ
To prevent burning or galling, be sure to lubricate regularly.
ޓޓ
When replacing rollers, apply grease to the entire circumference of the upper roller shaft and to the
ޓޓޓ
ޓ
inside of the lower roller.
ޓޓ
Remove the upper roller every two weeks and replenish the bearings with grease.
ޓޓ
Apply grease to the grease nipple on the side of the machine.
5) Clean after use (A)
ޓޓ
To prolong the life of the machine, be sure to clean the machine and the rollers each time after you use it.
ޓޓ
Before carrying out any inspections or machine maintenance, make sure you unplug the threading machine.
If the machine suddenly starts to operate while checking it, it may lead to accidents and injury.
ޓ
This machine is produced with great precision; therefore, should the machine fail to operate normally, do not
repair it by yourself, but call us for repairs.
ޓ
If parts are required or if you have any questions, please contact us at your earliest convenience.
B
.
Inspection of rollers
C. Grease nipple
C. Grease nipple