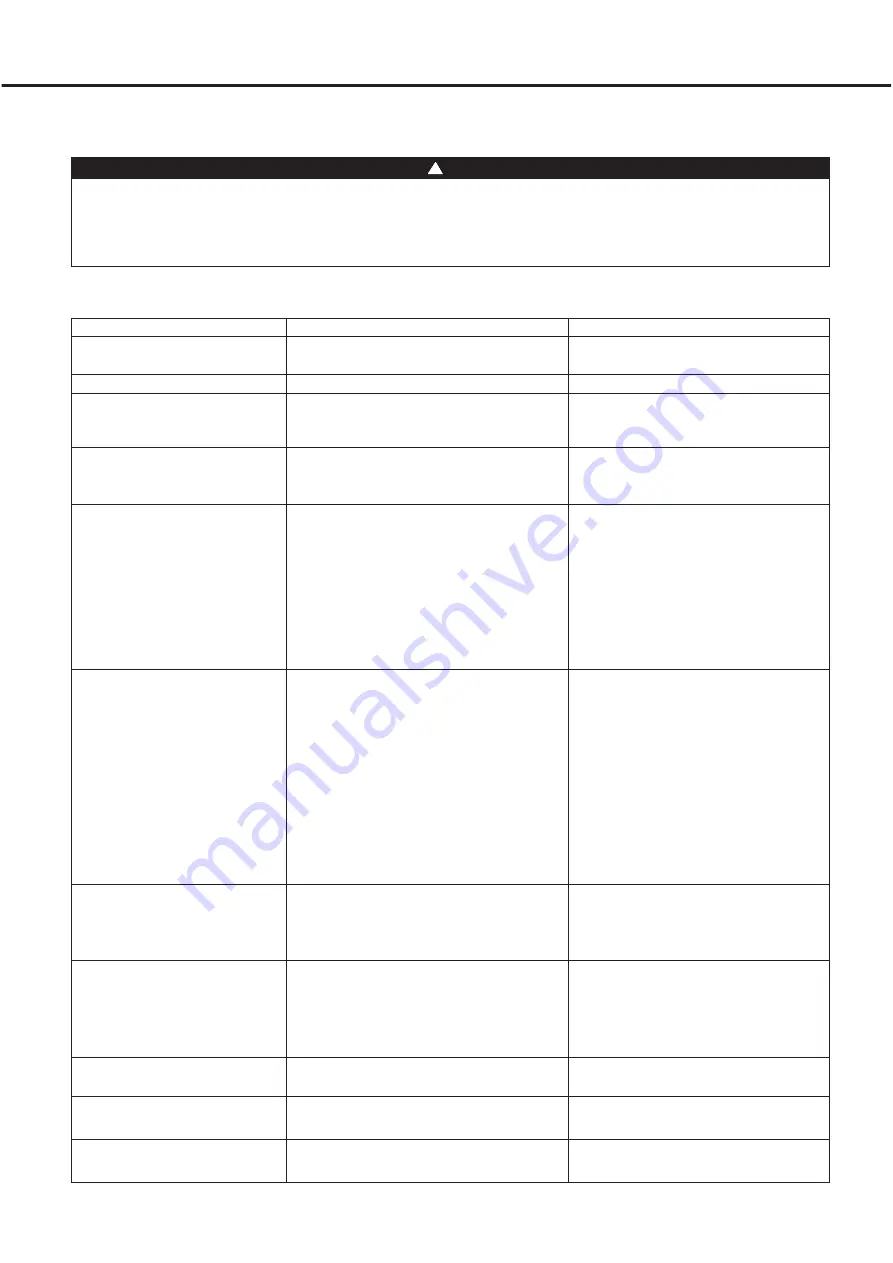
- 14 -
6. Before requesting repairs or servicing
㧍
WARNING
If there are any abnormalities with the unit, check the following and inform your distributor or our sales
department.
If any problems are not dealt with below, do not attempt to overhaul or repair the unit by yourself, but
call your distributor or our sales department.
If repairs are performed by untrained or unskilled personnel, optimum performance cannot be attained,
and accidents and injuries may occur.
The roller set doesn't match the pipe
ޓ
size.
Possible Causes
Corrective measures
Problem
The pipe has been cut at an angle.
The pressure of the resin guide roller
is too weak.
The pipe is elliptical in shape.
Speed of grooving is too fast.
Guide roller pressure is too strong.
The roller set differs from pipe size.
The pipe support is too high.
The speed of grooving is too fast.
The pipe shift angle is too large.
The pressure of the resin guide roller
ޓ
is too weak.
The pipe shift is in the opposite direction.
The threading machine is rotating in the
ޓ
wrong direction.
The pipe is too straight on the lower
ޓ
roller, or the angle of the shift is too
ޓ
small.
The pipe stand is too high.
The knurling on the lower roller is
ޓ
clogged up or worn.
The speed of grooving is too fast.
The width of the groove is too
ޓ
narrow or too wide.
The groove zigzags.
ޓ
The groove is not parallel with
ޓ
end of the pipe.
The diameter of the groove is
ޓ
not consistent around the
ޓ
whole of the pipe.
The pipe end flare is too great
ޓ
(bell mouth).
The pipe slips off the lower
ޓ
roller when grooving.
The pipe slips while it is being
ޓ
processed and doesn't rotate
ޓ
smoothly.
Operating the pump doesn't
ޓ
increase the depth of the
ޓ
groove.
Oil leaks from the hydraulic
ޓ
unit.
The adjusting nut is too tight.
The pump valve and/or packing are
ޓ
damaged, resulting in insufficient
ޓ
pressure.
The cylinder packing is damaged.
Replace roller set with one that
ޓ
matches the pipe size.
Cut the pipe at right angles.
Retighten the push knob and engage
the guide roller with the pipe a little
more strongly.
Make sure the pipe is perfectly
ޓ
circular.
Operate the pump a little more slowly.
Loosen the push knob so that it
contacts the guide roller more lightly.
Replace the roller set with one that
ޓ
matches the pipe size.
Adjust the height of the pipe support
ޓ
so that the pipe is 2
ࠑ
lower than the
ޓ
horizontal.
Operate the pump a little more slowly.
Adjust the pipe shift angle to 0.5
ࠑ
.
Re-tighten the push knob and attach
the guide roller to the pipe a little
more strongly.
Shift the pipe in the right direction.
Correct the direction of rotation.
Make the shift angle a little larger.
Adjust the height of the pipe support
so that the pipe is 2
ࠑ
lower than the
ޓ
horizontal.
Use a wire brush to clean up the
ޓ
knurling, or replace the lower roller
ޓ
as necessary.
Operate the pump a little more slowly.
Loosen the nut and process the pipe
ޓ
again.
Ask for repairs.
Ask for repairs.
ع
Troubleshooting
Groove depth is too shallow.
The pressure of the hydraulic unit is too
weak.
Ask for repairs.
Ask for repairs.
The upper roller doesn't go
right down.
The hydraulic unit doesn't have enough
oil.