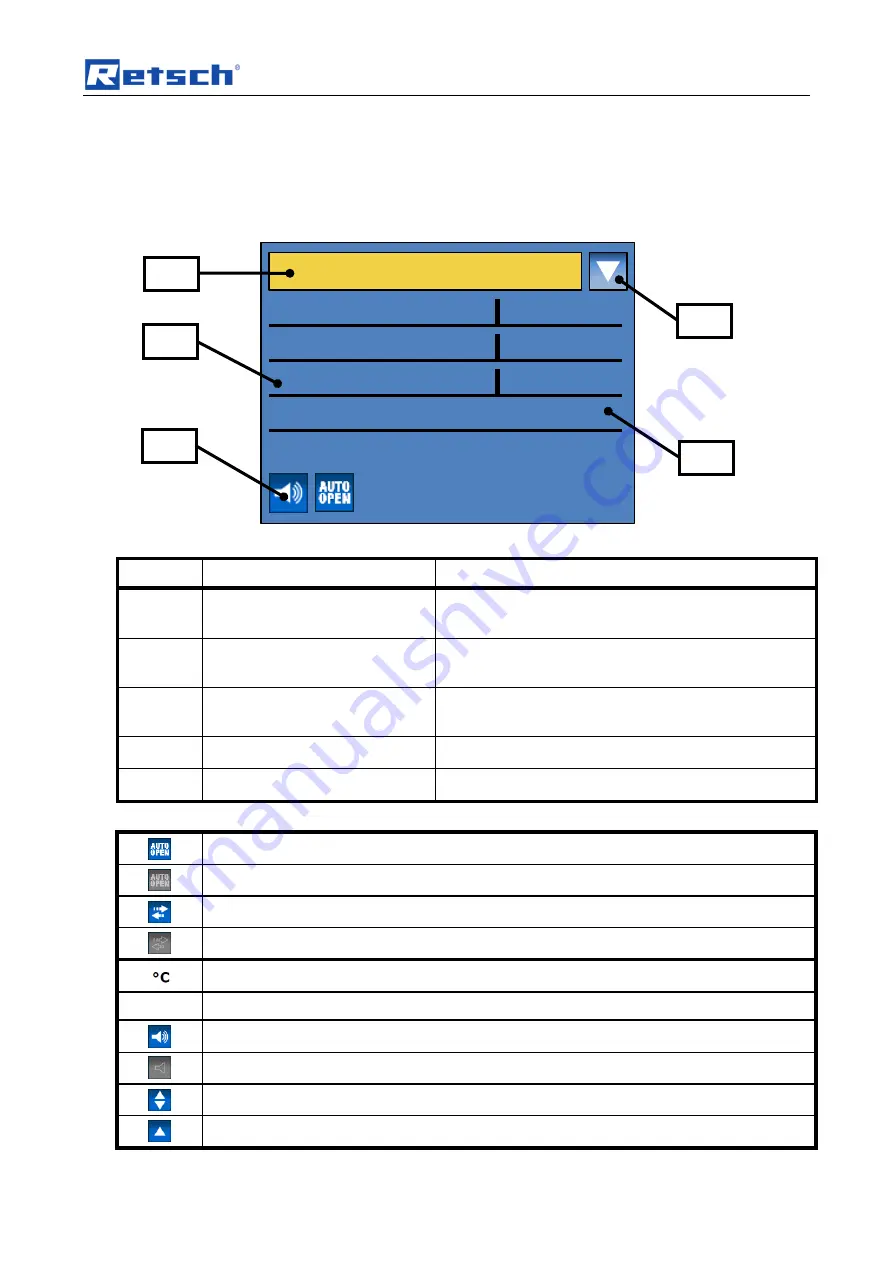
Display and operation
39
6 Display and operation
6.1 Symbols in the Display Unit
Fig. 28: View of the menu on the display unit
Element
Description
Function
C1
Menu navigation
Switching between manual operating mode, program
and basic settings
C2
Specification of grinding
parameters
Displaying and setting grinding parameters
C3
Icons for device functions
Displaying the function statuses of sound, automatic
opening and grinding jar recognition
C4
Icon for scrolling direction
Displays the possible scrolling directions
C5
Grinding parameters
Display of values
Automatic opening switched on
Automatic opening switched off
Direction reversal switched on
Direction reversal switched off
Motor or frequency converter too hot
Power
Grinding output display
Acoustic warning signal on
Acoustic warning signal off
Scrolling upwards or downwards possible
Only scrolling upwards possible
C4
C1
C5
C2
C3
Содержание PM400
Страница 2: ...2 Copyright Copyright by Retsch GmbH Haan Retsch Allee 1 5 D 42781 Haan Federal Republic of Germany ...
Страница 3: ...3 ...
Страница 23: ...Operating the machine 23 Fig 9 View of the back of the device S T U V W X Y ...
Страница 58: ......
Страница 59: ......
Страница 60: ...Copyright Copyright by Retsch GmbH Haan Retsch Allee 1 5 D 42781 Haan Federal Republic of Germany ...