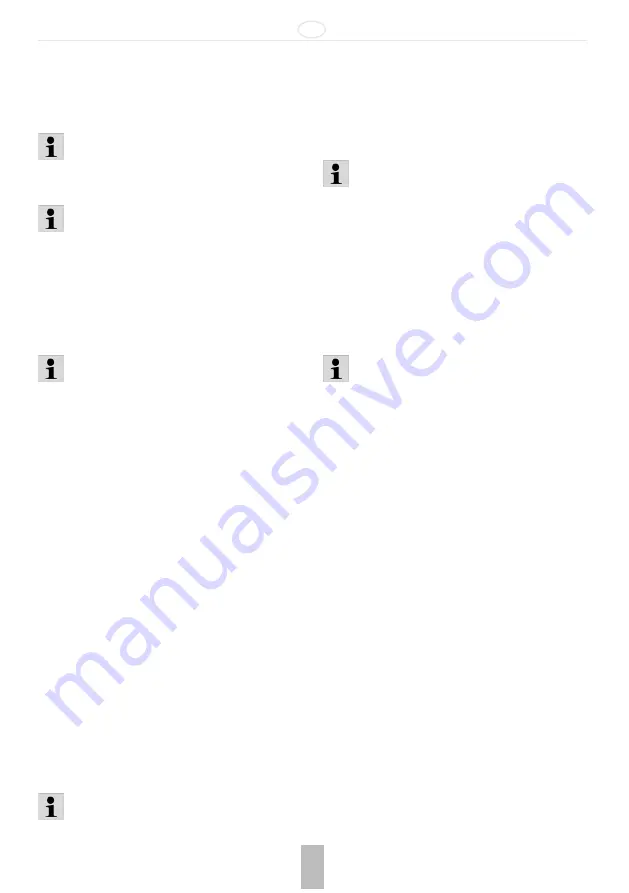
GB
MU1H-1178GE23 R0320
3
Date for next reverse rinsing can be set at the memory
indicator of the outlet pressure gauge.
To ensure convenient and regular adherence to the
reverse rinsing interval, we recommend installing an
automated reverse rinsing system Z11AS.
During reverse rinsing, an inlet pressure of at least
1.5 bar is required.
Filtered water can also be tapped during reverse
rinsing.
To avoid extra abrasion, we recommend to perform
the backwash at operating inlet pressures below 12
bar.
To ensure the proper backwash function also at
continuously higher media temperatures we advise to
follow the recommended service intervals. All the
internal parts should be checked to recognize
possible unusual abrasion.
5.1.1 Manual reverse rinsing
A collecting container must be positioned beneath
before reverse rinsing if there is not drainage system
available.
1.
Slowly open the ball valve
• The patented reverse rinsing system starts
2.
Close ball valve again after approx. 3-5 seconds.
Repeat procedure three times
• If the filter is extremely dirty, the procedure may
have to be repeated additional times
5.1.2 Automatic reverse rinsing with the
Z11AS
The automated reverse rinsing system Z11AS is available as
an accessory. The automated system reliably takes over
reverse rinsing of the filter at intervals which can be set
between 4 minutes and 3 months.
5.1.3 Differential pressure controlled
reverse rinsing with the DDS76 and
Z11AS
Also available as an accessory is the DDS76 differential
pressure switch. It provides fully automatic operation of the
reverse rinsing which is controlled by the differential pressure
across the filter. It actuates a reverse rinsing cycle when the
pressure differential between the inlet and outlet of the filter
reaches a predetermined value. If the pressure difference
exceeds the preset value, then the Z11AS reverse rinsing
actuator is operated via its volt-free input.
6
Maintenance
In order to comply with EN 806-5, water fixtures must
be inspected and serviced on an annual basis.
As all maintenance work must be carried out by an
installation company, it is recommended that a
servicing contract should be taken out.
In accordance with EN 806-5, the following measures must
be taken:
6.1 Inspection
An increased differential pressure between inlet and
outlet pressure gauge indicates a highly contaminated
filter.
•
The filter must be cleaned by reverse rinsing regularly,
at least every 6 months. (acc. to EN 806-5)
Our recommendation at least every 2 months!
•
Non-compliance can lead to the filter becoming
blocked This results in a drop in pressure and
decreased water flow
•
The filter meshes are made of stainless steel. A red
coating as a consequence of rust from the pipelines
has no influence on function or the way the filter works
Do not forget to do a visual check of the ball valve.
Replace if it is dripping!
6.2 Maintenance
6.2.1 Replace filter insert
1.
Close shut-off valve on inlet
2.
Release pressure on outlet side (e.g. through water
tap)
3.
Close shut-off valve on outlet
4.
Unscrew filter bowl
5.
Remove filter insert
6.
Insert new filter insert
• Put on the O-ring
7.
Put new O-ring on filter bowl
8.
Screw filter bowl in place
9.
Slowly open shut-off valve on inlet
10.
Slowly open shut-off valve on outlet
6.2.2 Replace filter mesh
1.
Close shut-off valve on inlet
2.
Release pressure on outlet side (e.g. through water
tap)
3.
Close shut-off valve on outlet
4.
Unscrew filter bowl
5.
Remove filter insert
6.
Dismount filter insert
7.
Replace filter mesh
8.
Mount the filter insert
9.
Put filter insert into filter bowl
10.
Put new O-ring on filter bowl
11.
Screw filter bowl in place
12.
Slowly open shut-off valve on inlet
13.
Slowly open shut-off valve on outlet
Содержание Braukmann F78TS
Страница 24: ...24 MU1H 1178GE23 R0320 4 2 6 2 1 4 3 6 2 2 ...