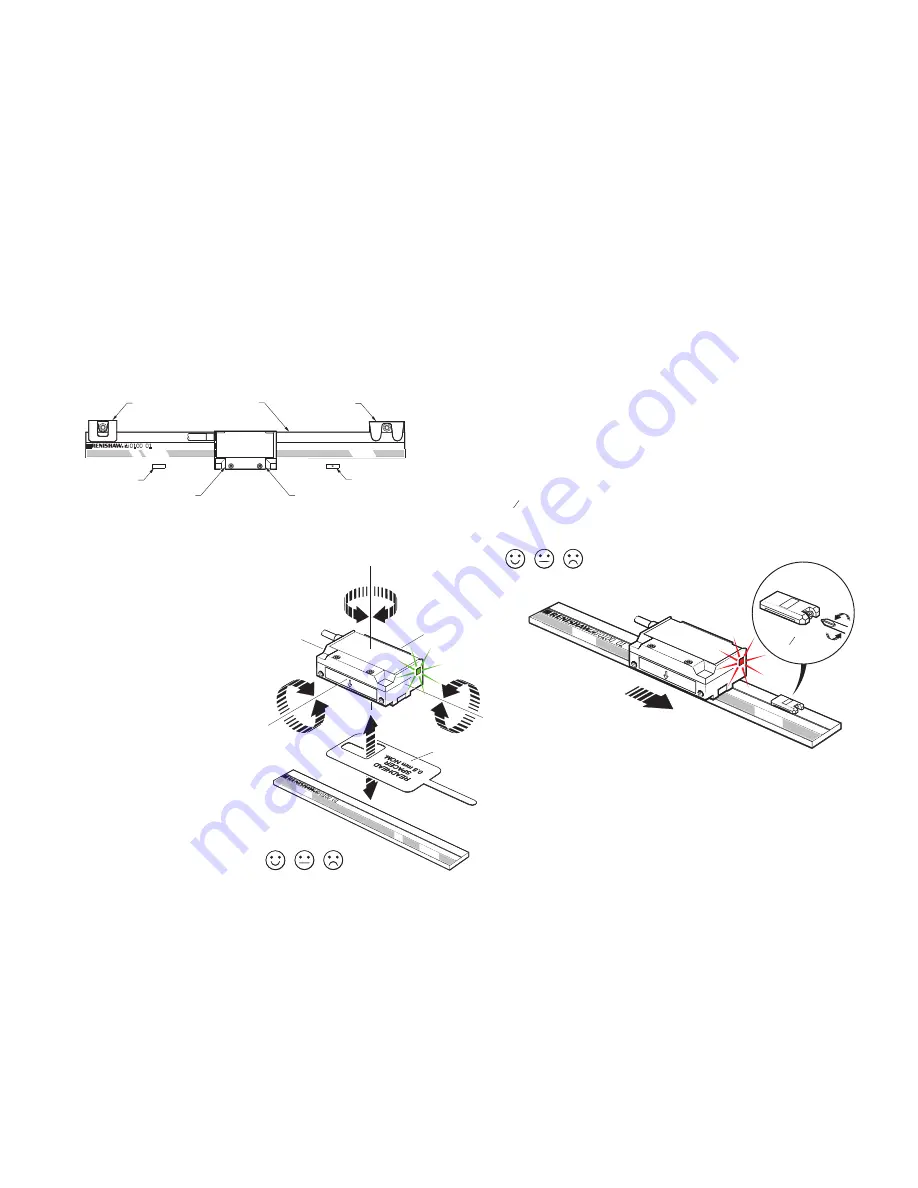
Yaw
0° ±1°
Pitch
0° ±1°
Roll
0° ±1°
Rideheight
0.8 ±0.15 mm
Blue spacer
Reference mark set-up
To ensure uni-directional repeatability, the reference mark requires phasing with the scale in
the direction of normal datuming operation.
A reference pulse is output in both directions, but repeatability is guaranteed only in the
phased direction.
Ensure readhead is set-up correctly with a Green LED indication over the full length of travel and
that the reference mark actuator is fitted correctly.
NOTE:
It is recommended that a datum procedure is performed as part of any power-up sequence
to ensure the correct datum position is recorded.
NOTE:
Reference mark output is synchronised with the incremental channels, giving unit of resolution
pulse width. For further details see ‘Output specifications’.
Phasing procedure
The readhead must be moved over the reference mark in the direction to be used for the datuming
operation. The reference mark is phased correctly when the set-up LED flashes Red for 0.25 seconds.
If it flashes Orange or goes blank, the reference mark adjuster screw should be turned anti-clockwise
by
1
8
turn and the procedure repeated until a Red flash is obtained.
1
8
turn
Red Orange Blank
Readhead set-up LED flash during
reference mark traverse only
RGH40 RGS40-G
installation guide
8
Adhesive P and Q limit magnets (A9531-0251) should be mounted using RGG-2 epoxy (A-9531-0342).
Ensure epoxy is thoroughly mixed prior to use. Allow 24 hours at 20
°C for full cure.
Optional bolted limit magnets available, see RGH40 installation drawing for details.
Readhead mounting and alignment
Mounting brackets
The bracket must have a flat mounting surface, enable conformance
to the installation tolerances, allow adjustment to the rideheight of
the readhead, and be sufficiently stiff to prevent deflection or
vibration of the readhead during operation.
For easier installation, adjust the roll and yaw of the bracket
with respect to the axis of readhead travel before the
RGH40 is attached. This can be done with a
clock gauge and a precision square.
Readhead set-up
To set nominal rideheight, position readhead spacer
with ‘L’ shaped aperature under the optical centre of
the readhead to allow normal LED function during
set-up procedure. Ensure that the scale, readhead
optical window and mounting face are clean and
free from obstructions.
NOTE:
Ensure readhead fixing screws are tightened
to 0.5 Nm – 0.7 Nm.
For reliable operation, the set-up LED should be GREEN
when readhead is moved along the full axis of travel.
An external set-up signal, X, is also available
on RGH40 readheads for use where the
LED is not visible.
See ‘Output specifications’ for details.
Datum clamp
Scale
Mounting clip
P limit magnet
P limit sensor position
Q limit sensor position
Q limit magnet
Reference mark actuator installation
Refer to RGH40 readhead installation drawing and RGS40-G scale installation drawings for actuator positioning.
Reference mark actuator (A-9531-0250) should be mounted using RGG-2 epoxy (A-9531-0342). Ensure epoxy is
thoroughly mixed prior to use. Allow 24 hours at 20
°C for full cure.
Limit switch installation
Screw mounted or adhesive mounted limit switch actuators are available. Refer to RGH40 readhead installation
drawing and RGS40-G scale installation drawings for actuator positioning.
Green Orange Red
Readhead set-up LED status
Limit switch
Limit switch detection is entirely independent of other readhead functions - the signal is only output
when the readhead is positioned over the limit switch actuator.