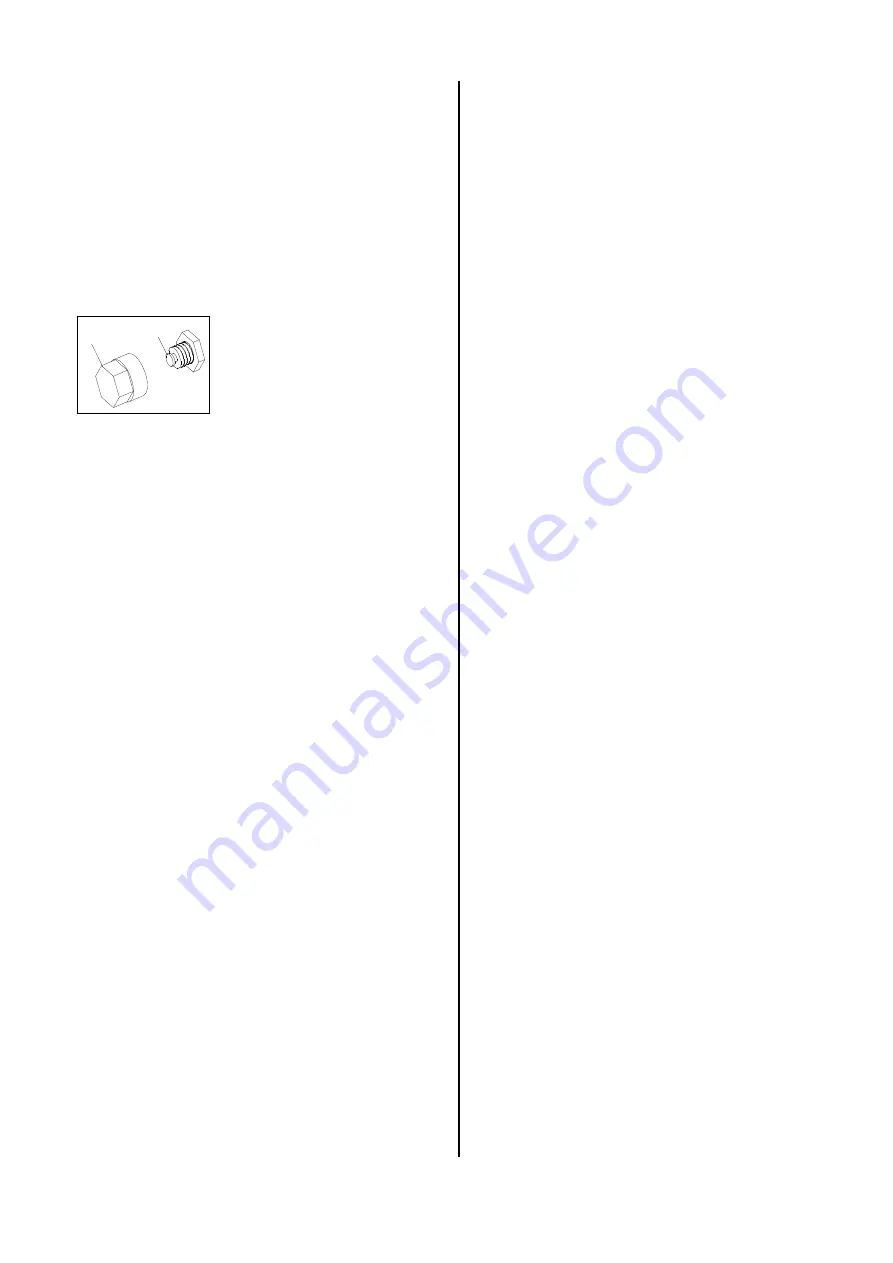
5
Safety temperature limiter (STB)
The safety temperature limiter (STB) interrupts the
burner operation in the event of overheating and locks
all unit functions.
If the safety temperature limiter has triggered, the cause
of the disturbance must first be localised and elimi-
nated. Resetting via the "RESET" key is only possible
after the sensor has cooled to below ca. 90 °C.
The safety temperature limiter is unlocked by pressing
the reset key.
1. Detach the protection cap
1
.
2. Press the reset key
2.
3. Replace the protection cap.
1
2
Provision for Air Heaters
For the deployment of the unit, the relevant guidelines
must be observed
1. Operating personnel
1.1 The unit must only be operated by persons who
have been trained in its operation.
2. Installation
2.1 The unit must be installed so that it can stand in a
stable position.
2.2 The unit must be installed and operated in such a
way that the employees are not exposed to the
danger of exhaust gases and radiant heat and that
the occurrence of fires is ruled out.
2.3 The unit may only be installed and operated in
rooms if a quantity of air sufficient for the combus-
tion is supplied to the unit and the exhaust gases
are removed to the exterior.
A natural air supply sufficient for the combustion is
present if e.g.
The room contents in m² correspond with at least
10 times the nominal heat load in kW of all the
units operating in the room and if windows and
doors ensure a natural change of air.
2.4 In deviation from point 2.3, the unit can be oper-
ated without an exhaust system in rooms if these
rooms have a sufficient air supply and are well ven-
tilated and if materials harmful to health do not
reach an unhealthy concentration.
2.5 A good natural air supply and ventilation is the case
if e. g.
The room contents in m² correspond with at least
30 times the nominal heat output of all units operat-
ing in the room and a natural change of air is en-
sured through windows and doors, or
openings which are not lockable are present in the
region of ceiling and floor for the air supply and for
out going air and the size of these openings in m²
corresponds with at least 0.003 times the nominal
heat output in kW of all units operating in the room.
2.6 The unit must not be installed or operated in rooms
and areas where the danger of fire or explosion ex-
ists.
3. Room drying
3.1 In deviation from point 2.3, in order to dry rooms
with an air supply sufficient for the combustion,
heating units can be operated without the exhaust
gases being removed to the exterior. In these
rooms, the permanent presence of persons is for-
bidden. Signs on the entrances to the rooms must
indicate that this is forbidden.
4. Examination
4.1 The unit must be tested by an expert as to its work
safety specific condition in accordance with the re-
quired deployment conditions but at least once an-
nually.
4.2 The exhaust values of the burner must be checked.
5. Monitoring
5.1 When starting work, the persons commissioned
with the operation of the unit must check the unit
for obvious defects or deficiencies on the opera-
tional and safety mechanisms and check that the
safety mechanisms are present.
5.2 If defects or deficiencies are discovered, the super-
visor must be informed.
5.3 In the case of defects or deficiencies which en dan-
ger the operational safety of the unit, its operation
must be terminated.
6. Installation in closed, well aerated rooms with-
out connection to a chimney
6.1 The operation of the units is admissible when the
minimum air quantity needed for combustion and
mentioned in point 2.5 is supplied.
6.2 A safe exhaustion of the waste gases is to be en-
sured to exclude inadmissible pollution.
Fresh air
is fed from
below
;
waste gases
are exhausted towards the
top
.
7. Correct usage
7.1 The unit are to be used only for heating purpose in
industrial or commercial application because of their
construction and equipment.
7.2 If specification of the manufacturer or legal regula-
tions, are not followed or if unauthorised changes
are made on the unit, the manufacturer is not liable
for resulting damages.