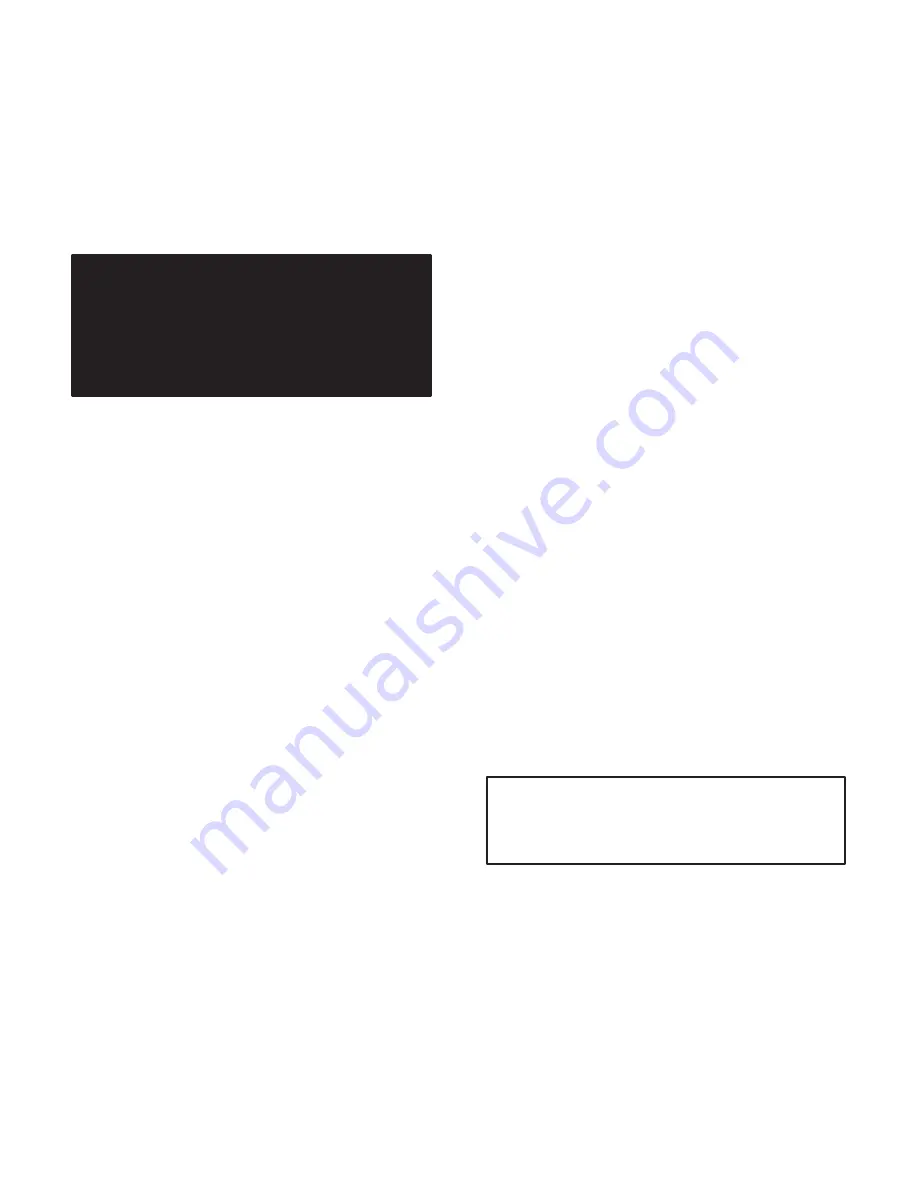
20
operator on the SPEED dial. The control range is 70 to
100% of rated speed.
The method for determining if the motor and driven
equipment are operating at an acceptable maximum
speed for the application is measure speed with a
tachometer.
Locate the Maximum Speed Potentiometer on the RegĆ
ulator Module. (Refer to Figure 4.4.) The letters MAX
SPD are printed on the Module. Note that CW rotation
represents an
increase
in speed. CCW represents a
decrease.
DANGER
WHEN PERFORMING THIS ADJUSTMENT PROĆ
CEDURE, DO NOT ALLOWTHE DRIVE MOTOR
TO EXCEED ITS RATED MAXIMUM SPEED, AS
LISTED ON THE NAMEPLATE. EQUIPMENT
DAMAGE AND SERIOUS PERSONAL INJURY
COULD RESULT.
On the Operator Station, increase the SPEED dial slowĆ
ly in the direction of 10, which is 100% of full travel. If, as
the SPEED dial is turned toward the 10 setting, the
speed exceeds the maximum acceptable speed,
imĆ
mediately
decrease the maximum speed on the
SPEED dial. Use a small insulated slot screwdriver.
In
some cases,
to avoid exceeding the maximum operĆ
ating speed, it may be necessary to turn the Maximum
Speed Potentiometer completely CCW before turning
the SPEED dial completely CW.
If the 10 setting on the SPEED dial is lower than the deĆ
sired speed, increase the setting on the Maximum
Speed Potentiometer to the necessary speed. To inĆ
crease the maximum speed, turn the potentiometer CW.
NOTE: A further adjustment may be needed but It
should be performed after completing Paragraph
4.3.3. Note that the maximum and minimum speed
adjustments are interactive; a change in one affects
the other.
4.3.3. Minimum Speed (Voltage)
- The Minimum
Speed Potentiometer on the regulator has been factory
preset for drive minimum speed, 5%. By means of adĆ
justment, this speed may be raised or lowered. The reĆ
sult is the lowest moving speed the operator can set on
the SPEED dial. The control range is 5% to 30% of rated
speed.
Again, the motor speed can be determined with a
tachometer.
With the SPEED dial at zero position and using a small,
insulated slot screwdriver, carefully turn the Minimum
Speed Potentiometer until the desired minimum is
reached. Note that CW represents an
increase;
CCW
represents a
decrease.
NOTE: Carefully recheck the maximum speed adĆ
justment for desired setting Since the maximum and
minimum speed adjustments are interactive, a
change in one affects the other. At times, it may be
necessary to work back and forth for precise adjustĆ
ments.
4.3.4 Acceleration and Deceleration Rates
- The AcĆ
celeration and Deceleration Rate Potentiometers on the
Regulator Module have been factory preset for a typical
linear acceleration rate of six seconds to maximum and
minimum speed. This time can be adjusted over a range
of 0.5 to 30 seconds from a fully stopped condition.
4.3.5 Current Limit
- Although it will probably not be
necessary to make any adjustment in the factoryĆset
current limit value of 150% of rated load, it is possible to
change this governing value. (Individual application
speed changes or load changes on sustained overĆ
loads may require readjustment. Also, applications reĆ
quiring torque limiting or accelerating of high inertia
loads may require a change from this value.)
To reduce the torque output of the drive, turn the Current
Limit Potentiometer CCW. Note, however, that turning
CCW too far may prevent the drive accelerating to the
desired speed.
4.3.6 IR Compensation
- IR (voltage) Compensation
is a feature which makes up for the armature resistance
of a motor that causes a drop in speed as the load is inĆ
creased. The IR Compensation Potentiometer is factoĆ
ryĆset at zero. The IR compensation feature can be adĆ
justed between O and 12% of rated load and is used
only for a voltage regulation mode.
When using a
tachometer feedback, the IR Compensation PotenĆ
tiometer must be turned completely CCW.
CAUTION:
If the IR Compensation Potentiometer
is set too high, motor speed rising characteristics
may result. Instability and oscillation in motor
speed will result.
Содержание MinPak Plus
Страница 1: ......
Страница 3: ......
Страница 9: ......
Страница 13: ......
Страница 17: ......
Страница 28: ......
Страница 29: ......
Страница 30: ......
Страница 31: ......
Страница 32: ...Figure 5 9 230 VAC Auxiliary Panel Assembly Schematics...
Страница 33: ...Figure 5 10 460 VAC Auxilliary Panel Assembly Schematics...
Страница 34: ......
Страница 35: ......
Страница 36: ......
Страница 37: ......
Страница 38: ......
Страница 39: ...Figure 5 13B Technical Data 230 VAC Three Phase MinPak Plus...
Страница 40: ......
Страница 41: ...Figure 5 14B Technical Data 460 VAC Three Phase MinPak Plus...
Страница 42: ......
Страница 43: ......
Страница 44: ......
Страница 45: ......
Страница 51: ......
Страница 53: ...Page TABLE OF CONTENTS ii 7 0 General 47...