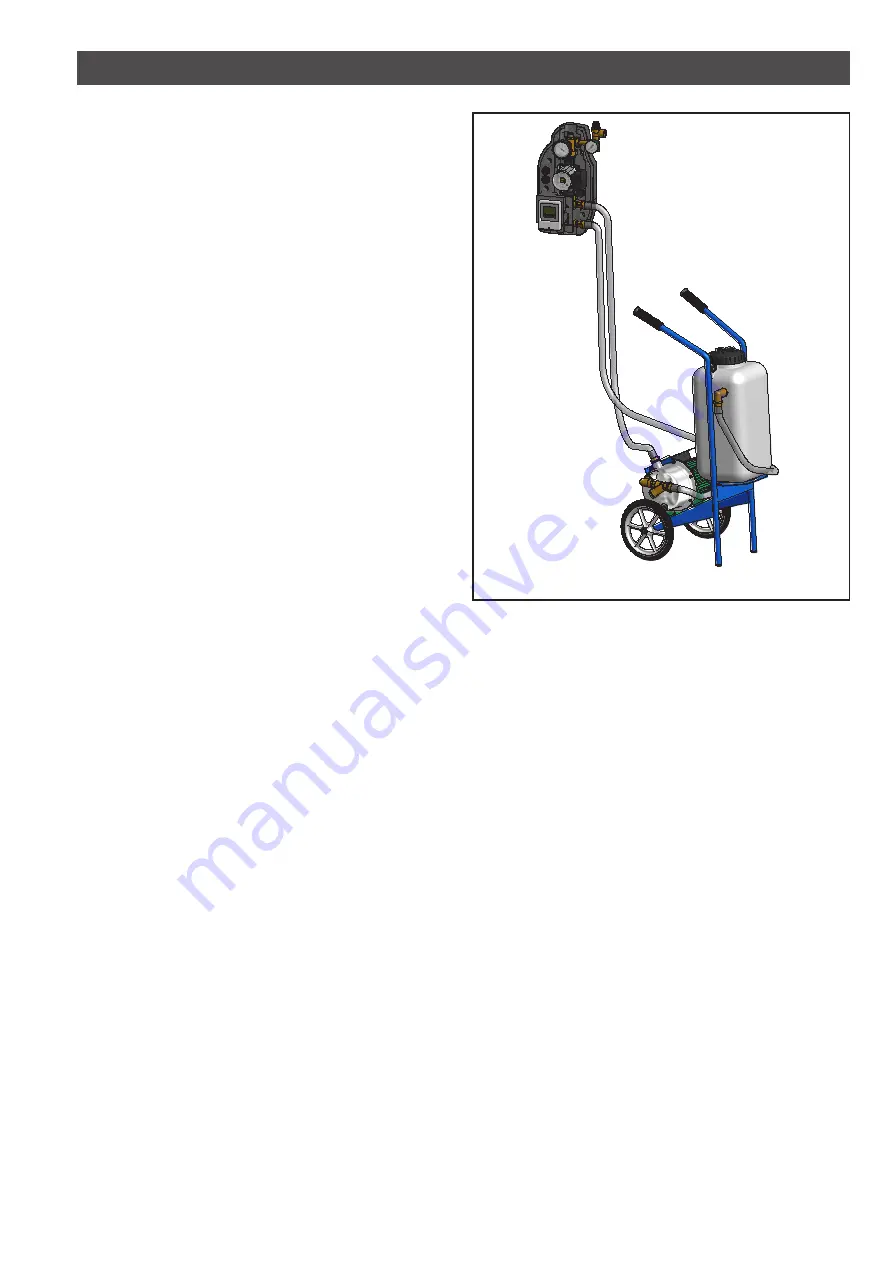
20
The below listed procedures are valid when a Regulus
pump station is used.
10.1 Filling
• for safety reasons, you should only fill the collectors
when there is no direct irradiation from the sun
(or cover the collectors)
• in order to fill the system, use a filling device with a
reservoir for solar liquid and a filling pump (see Fig. 31)
• attach the filling hose to the feed valve and open the
valve completely
• please use antifreeze solar fluid Regulus - Solarten
Super to fill the system
• attach the return hose to the bleed valve and open the
valve completely
• close the integrated ball valve in the flowmeter (the
groove in the flowmeter‘s adjusting screw must be
horizontal).
• open the check valve (valves - two for a twin-pipe
solar pump station) above the pump by turning the ball
valve by 45° (intermediate position between open and
closed)
• pour sufficient quantity of solar fluid into the reservoir
of the filling device, turn on the filling pump and fill the
solar system.
10.2 Flushing
• flush the solar system for at least 15 minutes using
the filling device. In order to bleed air and possible
impurities from the system perfectly, open shortly the
integrated ball valve of the flowmeter from time to time
(the groove vertically).
10.3 Air bleeding
• with the filling pump running, close the bleed valve and
increase the pressure up to about 5 bar
• close the feed valve and turn off the filling pump, open
the regulation screw on the flowmeter (groove horizon-
tally), do not disconnect the filling pump hoses!
• set the circulation pump(s) to the highest speed and
repeat switching on and off to air-bleed the system (an
air-free pump works almost noiselessly)
• watch the system pressure and when it starts falling,
increase it by turning on the filling pump and opening
the feed valve to 5 bar
• repeat air bleeding so long until the float in the flowme-
ter‘s regulation valve takes a steady position during
pump operation and bubbles stop appearing in the
flowmeter. After that, let the circulation pump run for at
least 5 minutes.
10. SYSTEM FILLING, FLUSHING, LEAK TEST AND AIR BLEEDING
• in case an automatic air vent/s is/are used anywhere in
the solar system, close this valve after air bleeding.
10.4 Leak test
• examine the whole system at 5 bar pressure (all con-
nections, solar collectors, valves etc.), no visible leaks
are allowed. Leave the system under pressure for at
least 2 hours, then examine the system once again
• consider the test result successful if no leaks appear
and/or no noticeable pressure drop appears in the
system
• set the working pressure by point 8.2 Calculation of
system working pressure
• set the pump to a suitable speed and set the flow by
the flowmeter and data in Tab. 1
• disconnect the hoses of the filling device and screw
caps on the feed and bleed valves
•
open entirely
the ball valve(s) above the pump
• after several days of operation, air-bleed the system
again.
Do not flush the system with water. Since it is impossible
to empty it completely, a risk of frost damage appears.
Fig. 31: Filling a solar system
Содержание KPS1
Страница 24: ...24 1036 25 90 45 2037 25 1922 ø22 15 CONNECTION DIMENSIONS ...
Страница 27: ...27 ...