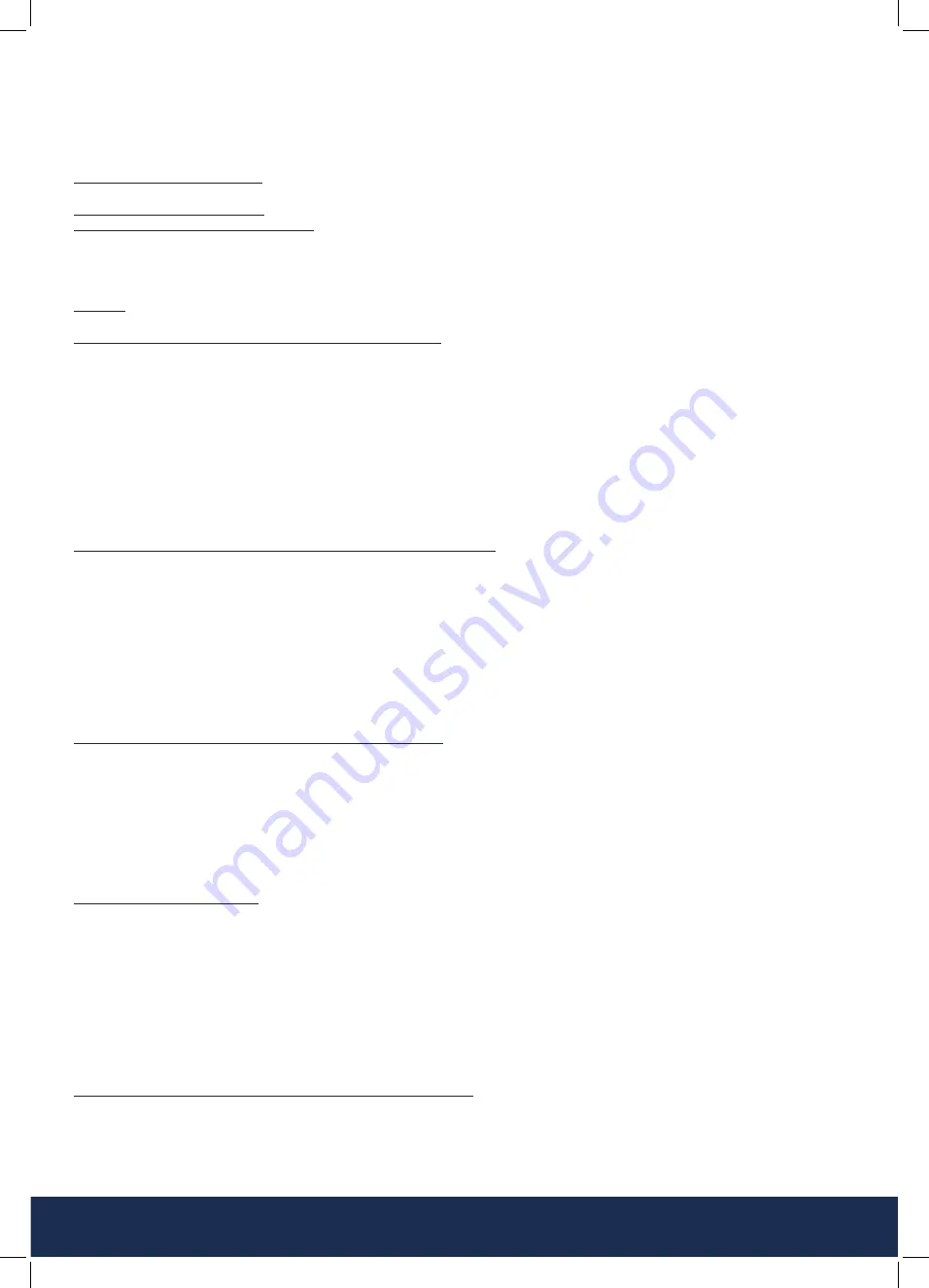
www.
reefe
.com.au
Ascento Group Australia
©
AI.062020
P: 1800 807 604
i) You can reset the function back to the beginning anytime by pressing the restart button.
j) If it is many days before it rains again (or you have your tank re-filled), turn off the power to the pump, at the power outlet
k) Occasionally when the pump re-starts after a run-dry event, some air might come through the lines, this will do no harm.
l) NOTE: if pipe from tank to pump is not straight it will most likely get air-locks in the pipe, and the pump might not shut down properly
when the tank is low, as it is getting some air, some water - this is not a fault – simply turn the pump off until the tank fills to have 500mm
depth or more.
TROUBLESHOOTING CHECKLIST
Check the following before requesting service or repair. A call out fee and labour cost may apply to field services.
PROBLEMS & POSSIBLE CAUSES;
20. Light Flashes “No Water” or “Failure”
1. This normally indicates that the pump has no water, either because the tank is empty or the pump has “lost prime” it has run dry.
2. The pump is fitted with an AUTOMATIC RESTART controller so it will attempt to re-start itself several times. This is normal, it does not
mean the pump is faulty. Refer to point 19 a) to k) of the instructions.
NOTICE:
tank level indicators are not always accurate!! Check inside the tank to be sure of the water level.
21. Pump does not run or motor runs for a short time, then stops
1. Circuit breaker or Safety Switch is off or fuse has blown > in a SAFE manner investigate why this has occurred, by process of elimination
> do not assume it is the pump > if you cannot do this safely, have a licenced Electrician check and rectify it.
2. Water level in the tank is too low > Top up or use alternative supply > turn pump off until the tank fills
3. Electrical components have been flooded > It is likely that the pump will need to be replaced > in a SAFE manner investigate why this
has occurred, by process of elimination > do not assume it is the pump > if you cannot do this safely, have a licenced Electrician check and
rectify it.
4. Pump plug is not connected properly, or has been flooded or wet > Isolate power at main switch, remove plug & allow to dry. If the
problem continues, contact a licenced electrician to check the cause.
5. If all of the above are OK, the pump might have overheated and triggered the thermal overload switch > Turn it off and wait 30 minutes
for it to cool down and turn it on again > If the pump does not operate normally, investigate why, it might be blocked with debris, or the
Y-Strainer/Prefilter might be blocked > flush clean and re-assemble.
22. Pump runs but does not deliver water or only a small amount of water
1. Check valve is installed backwards, arrow on valve should point in direction of flow > have the installer fix this.
2. Discharge shut-off valve/ball-valve / gate-valve may be closed > open the valve.
3. Impeller or volute openings are fully or partially clogged or it might be blocked with debris, or the Y-Strainer/Prefilter might be blocked
> flush clean and re-assemble > if it is the pump, disconnect from the power supply, and if you are competent to do so, disassemble the
pump and clean. If not, have a pump technician do it for you.
4. Pump is air-locked > Start and stop several times by turning it on and off with 20 seconds between. If this does not work, see below
regarding re-priming the pump
5. Vertical pumping distance is too high - Reduce distance or upgrade to a larger pump.
6. Foot valve blocked > Clean or replace the FOOT valve
7. Tank too low water level > Check the suction and water levels
23. Pump runs and does not stop or runs when no taps are in use
1. In most cases this situation it is due to a leak in pipework or leaking toilet cisterns or underground pipe leak (wet soil, muddy, grass
growing well!) > it is not a pump fault > ascertain by process of elimination what is leaking > the only sure way to check toilet cisterns is to
turn them off at the stopcock which is usually under the cistern as most of them will not run into the pan > close the ballvalve / gate-valve
on the discharge side of the pump, does the pump now stop > something is leaking it is not a pump fault.
2. There could be debris inside the Pump Controller > open all taps fully to try and flush it out > if this does not work disconnect from
the power supply and [a] remove the pipework off the top of the controller there is probably some debris in the brass “popit valve” that
is in the top of the controller, carefully remove the debris > if it is not that disassemble the pump controller and clean, or have a pump
technician do it for you.
24. Pump not pumping properly
1. Too high head or pump under specified > Check specifications.
2. Too low water level > Check the water level in the tank, tank level indicators are not always accurate
3. Loss of prime > Check foot valve (if fitted), re-prime the pump.
4. Leakage of inlet pipe > Check the inlet pipe is not taking in air, check all joints.
5. Inlet Pipe has rise and fall (Dips) or has too many elbows or is blocked > Fix suction pipe so it is both perfectly straight and level, OR
rises all the way to the pump, or turn the pump off and wait for the tank to fill more > NOTE: if the inlet pipe is not straight to the pump it
is most likely that you WILL get airlocks in the pipework especially when the tank has low water, this is NOT a pump fault > turn the pump
off until the tank fills to have 500mm depth or more.
6. If a check valve has been installed directly on the discharge of the pump controller, this may cause the pump controller to malfunction >
Move the check valve to a different position.
25. Safety Switch (RCD) or Circuit Breaker trips when the pump starts
1. Circuit is overloaded with too many appliances connected to it > contact a licenced electrician to install additional circuit
2. Power plug is wet > refer 21.
3. Pump has been flooded > refer 21.3
4. If none of the above, the Motor may be defective > have it checked by a qualified technician
If you have checked all the above trouble shooting points and it fails to rectify the problem, have it checked by a qualified technician
VSRE - Parts Breakdown.indd 9
VSRE - Parts Breakdown.indd 9
25/06/2021 1:32:52 PM
25/06/2021 1:32:52 PM