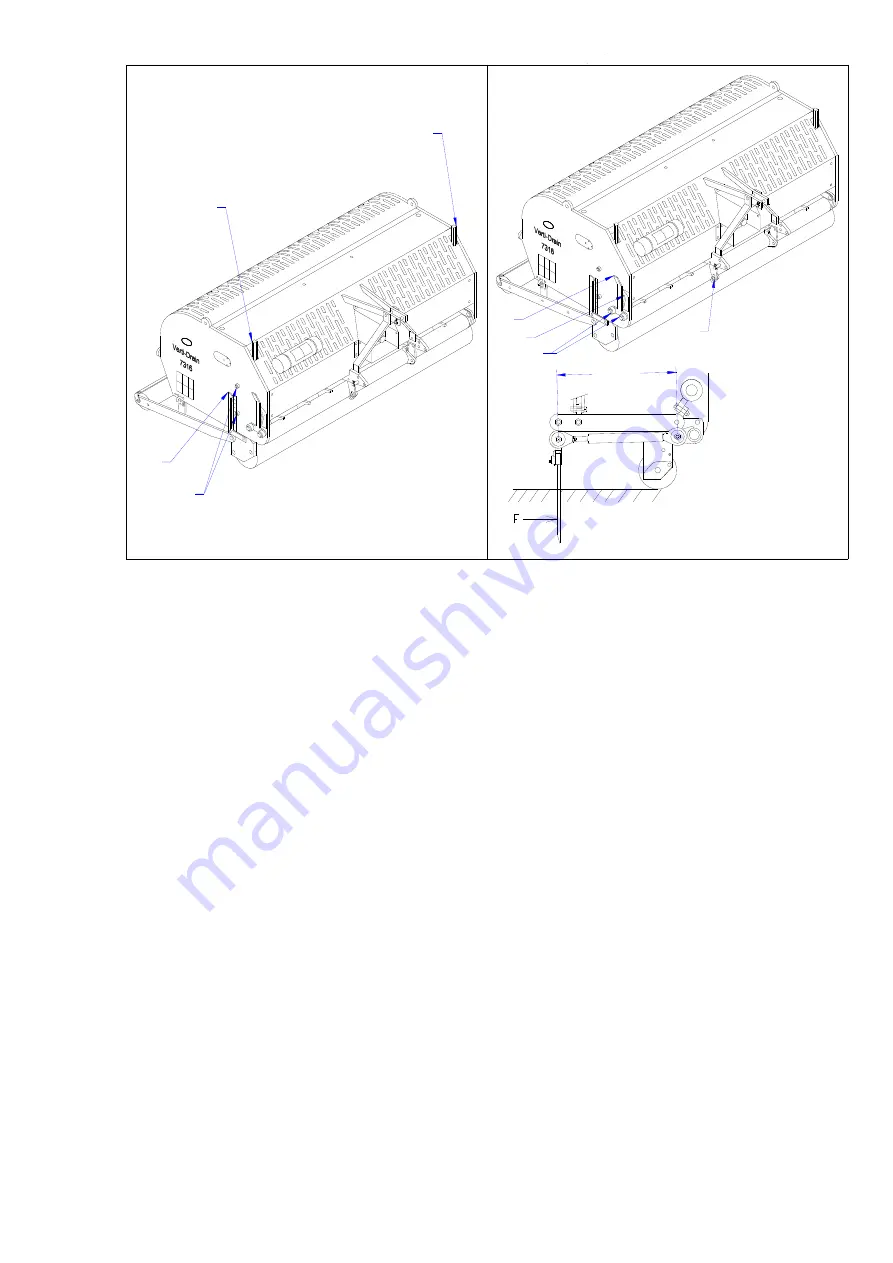
10
5.0 WORKING DEPTH ADJUSTMENT.
The working depth can be adjusted when the machine is lifted from the ground as follows, see fig. 4:
Unscrew nuts 1 at each side of the machine one turn. Screw spindle 3 in or out. Every revolution is 4
mm (0.160"). The decal 2 at each side of the machine shows the actual depth. When the correct depth
is reached, tighten the nuts 1 at each side.
@ Never adjust one side more than 4 turns. Compensate the other side first before proceeding.
@ The adjustment can be done with a special tool in the machine tool box.
@ The value at the decals is only true when 300 mm (12") long tine are used. When shorter tines are
used, deduct the length difference to the 300 mm (12") from the actual decal reading.
@ Clean and spray the spindle and nut with anti-sticking grease oil every 100 hours, to prevent dirt
sticking on the nut.
6.0 TINE ANGLE ADJUSTMENT
.
The adjustment of the angle of all tine holders is centrally located at the right side of the machine, see
fig.5..
Raise the machine above the ground, slacken the nuts 2 at each side of the machine and nuts 3 at the
centre of the machine, one turn each.
Adjust the tine angle by rotating the lever 1. The angle-value can be read from the decal 4 next to the
handle.
After the correct angle is set, tighten all nuts.
@ An angle of 90 degrees means almost no tine movement in the ground. This is required for hollow
coring tines and advised for thinner tines.
@ From 90 to 75 degrees means more "kick action". This is advised for solid tines, depending on
ground conditions, tine size and customer requirements.
Fig.5.
1.
2
Fig.4.
3
3
430.6
.2
1
4
3