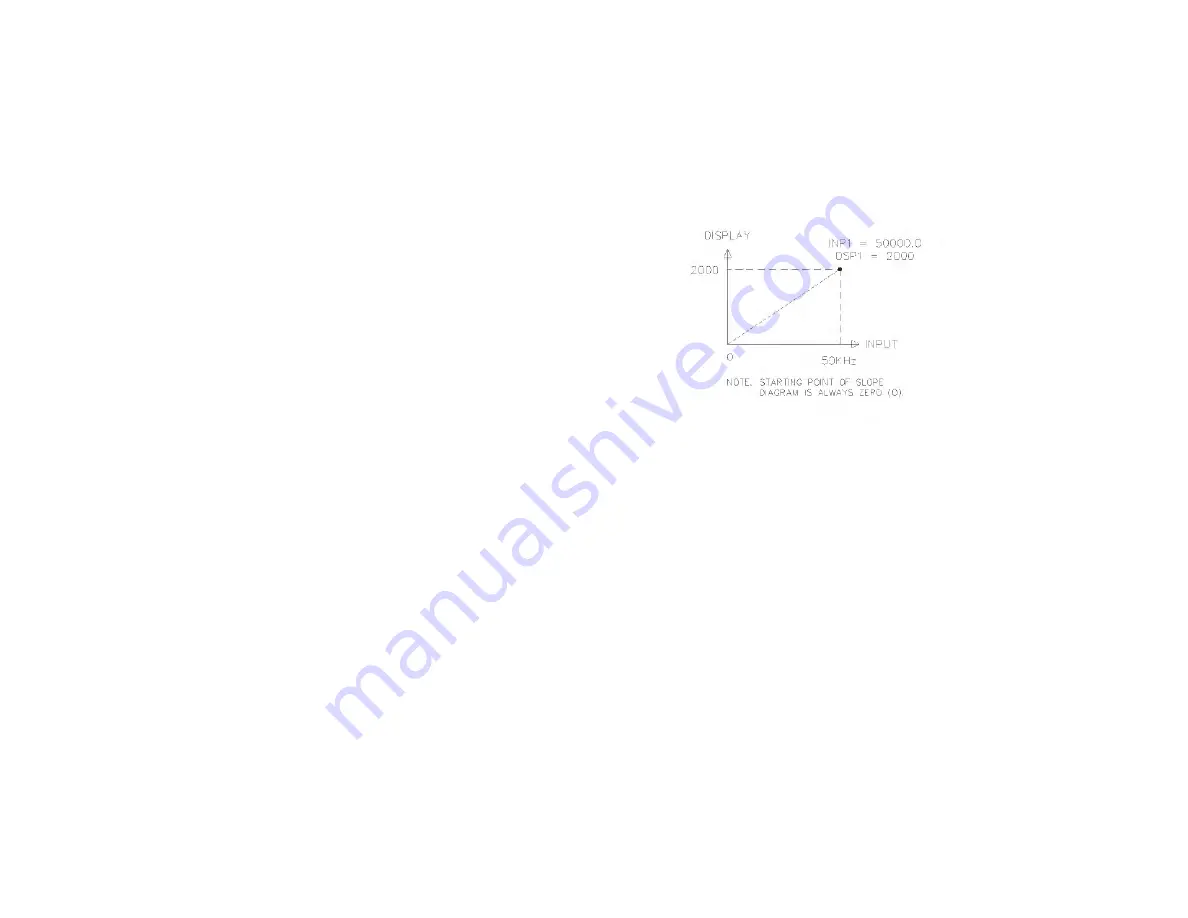
THEORY OF OPERATION
The IMH employs a microprocessor to perform the A/D conversion on the
input signal via a voltage-to-frequency converter. It digitally scales the result,
corrects for meter drift which may be present and then displays the result in a
6-digit display
(5 for input, 6 for totalizer)
. The inputs are filtered to enhance the
stability of the display. A non-volatile E
2
PROM memory device provides
permanent data retention for operating variables. The display consists of drivers
and 6-digit solid-state LEDs. The alarm option employs opto-isolators to isolate
the open collector devices from meter common. Operating in parallel, the relays
are type Form-C and are rated at 5 Amps. The analog option features a 12-bit
DAC and provides an output signal that is digitally scaled. The re-transmitted
output is isolated from meter common.
PROGRAMMING THE IMH
Prior to installing and operating the indicator, it may be necessary to change
the scaling to suit the display units particular to the application. Although the unit
has been pre-programmed at the factory, the set-ups will generally have to be
changed.
The indicator is unique in that two different scaling methods are available. The
operator may choose the method that yields the easier and more accurate
calibration. The two scaling procedures are similar in that the operator keys-in
two display values and either keys-in or applies a signal value that corresponds to
those display points
(see FIG. 2)
. The location of the scaling points should be
near the process end limits, for the best possible accuracy. Once these values are
programmed
(coordinates on a graph)
, the indicator calculates the slope and
intercept of the signal/display graph automatically. No span/zero interaction
occurs, making scaling a one-pass exercise. Basic scaling is complete after
decimal point selection, unit rounding
(dummy zeros)
and digital filtering level
selection. The following procedure should be followed to scale the indicator.
Before actually trying to program the indicator, it is advised to organize all the
data for the programming steps to avoid any possible confusion and to read the
programming procedure entirely before proceeding.
To set-up the indicator, connect AC power and signal wires as outlined in the
connections section
(Appendix “A”)
. Remove the jumper wire
(if installed)
from
TBA #3
(PGM. DIS.)
. This will allow the operator to enter and modify all of the
indicator’s parameters. Press the front panel button labeled
“P”
, momentarily.
Briefly, the display will show
“Pro”
alternately flashing with
“0”
. This is the
indicator’s programming mode. The programming mode is divided into sections,
numbered 0-9, each of which can be individually accessed. The front panel
“UP”
and
“DOWN”
arrow buttons can be used to select one of these numbers
and the
“P”
button used to enter the selected programming module. In all of the
programming modules,
“UP”
and
“DOWN”
are used to either select from a list
of choices or enter a value. The
“P”
button is used to save the new value and
progress to the next step within a module
(Note: the new value takes effect when
“P” is pressed)
. Upon completion of a module, the indicator returns to the
“Pro”
< >
“0”
. Pressing the
“P”
button at this point causes the unit to display
“End”
,
after which the unit returns to normal mode. The following table explains the
basic function of each step.
Note: < > This indicates that the display will alternate between the English
prompt and the actual data.
-4-
FIGURE 2: SLOPE DIAGRAM