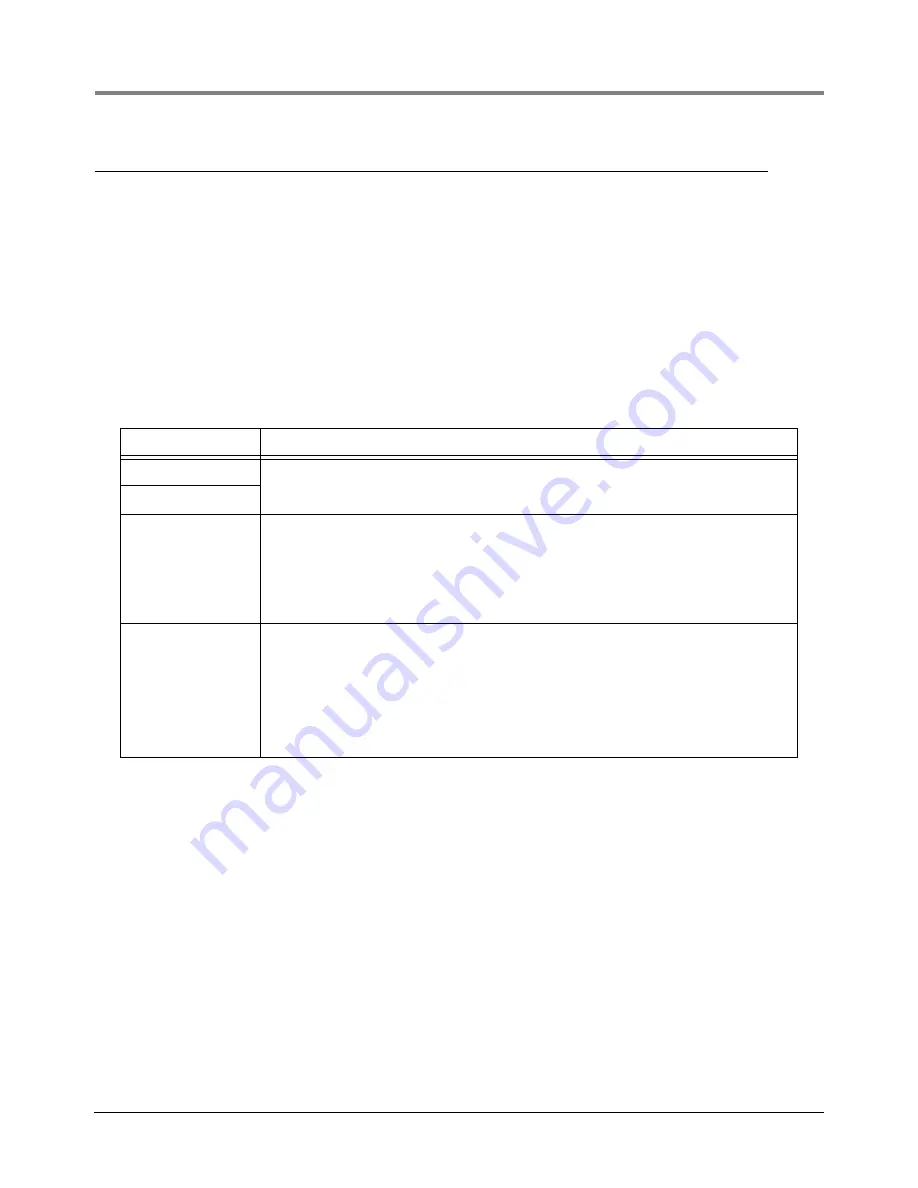
Introduction
System Protection
14
System Protection
Red Jacket recommends a complete system built around the pump to ensure safety, reliability, stability, and
performance. If the entire system is calculated and built according to accepted specifications, the installation will
operate for many years without requiring any form of maintenance.
There are two pump characteristics that can be checked if performance deteriorates:
1. Its output - flow rate versus pressure.
2. Its electrical connections and amperage consumed under load.
Potential Problems
Red Jacket submersible LPG pumps are multi-stage centrifugal pumps. The advantage of the multi-stage
technology is maximum performance by a minimum of energy, respectively 2.25 kW (3 hp) for the 21 stage
Premier pump, 2.25 kW (3 hp) for the 17 stage Premier MidFlow pump and 3.75 kW (5 hp) for the 24 stage
Premier HiFlow pump. During operation the pressure increases with approximately 50 kPa (7.25 psi) per stage up
to the maximum design pressure of the pump respectively 1000 kPa (145 psi) for the Premier pump, 880 kPa
(127 psi) for Premier MidFlow pump and 1220 kPa (180 psi) for Premier HiFlow pump.
For all types of Red Jacket submersible LPG pumps the minimum differential pressure can never be below 400
kPa (58 psi). This minimum required differential pressure is to guarantee that during operation all respectively 17,
21 or 24 stages are submerged in the LPG liquid. Another basic rule for a centrifugal pump is that there must be
sufficient liquid available by the inlet of the pump. The pump can only build differential pressure when the first
stage of the pump is completely submerged in the liquid. This so-called NPSH (Net Positive Suction Head) is 127
mm (5 inches) above pump inlet opening for all types Red Jacket submersible LPG pumps.
Cavitation is when the liquid flows with a velocity high enough to reduce the local pressure below vapor pressure
forming small gas-filled bubbles. These gas-filled bubbles exhibit complex dynamics and erosive action on nearby
surfaces.
Table 5. Potential Performance Problems
Problem
Solution
Dry run
A control box with low pressure detection can detect both of these performance prob-
lems.
Cavitation
Equalization line in
the manifold is too
small
The Red Jacket LPG pump has an internal by-pass. A certain amount of LPG passes
and cools the motor (self-maintaining principle) and exits the pump at the internal by-
pass. The motor’s heat is transferred to the liquid and is therefore warmer than the liq-
uid in the tank. Also this liquid has a higher vapor pressure than does the liquid in the
tank. The equalization line between the manifold and the tank is to balance both liquid
levels. If this equalization line is too small or even closed, the manifold can be emptied
through the manifold inlet and it can cause a dry run or even cavitation.
Dirt in the tank
Small parts of LPG dust or iron oxide, which can normally be found in LPG, will not
hurt the system. During operation those particles can, however, block the breather
plugs at the inlet of the pump-motor, but when the pump is switched off a small amount
of liquid will be pressurized back in the tank. This amount of liquid will clean the
breather plugs again.
Of course, any form of dirt should be avoided and shortens the expected lifetime of the
pump. It is recommended to install a strainer (100-micron) at the inlet of the storage
tank to avoid dirt entering the tank during deliveries.
Содержание LPG Premier
Страница 1: ...Manual No 051 327 1 Revision N Installation Guide LPG Premier LPG Premier MidFlow LPG Premier HiFlow...
Страница 38: ......
Страница 39: ......
Страница 40: ...For technical support sales or other assistance please visit www veeder com...