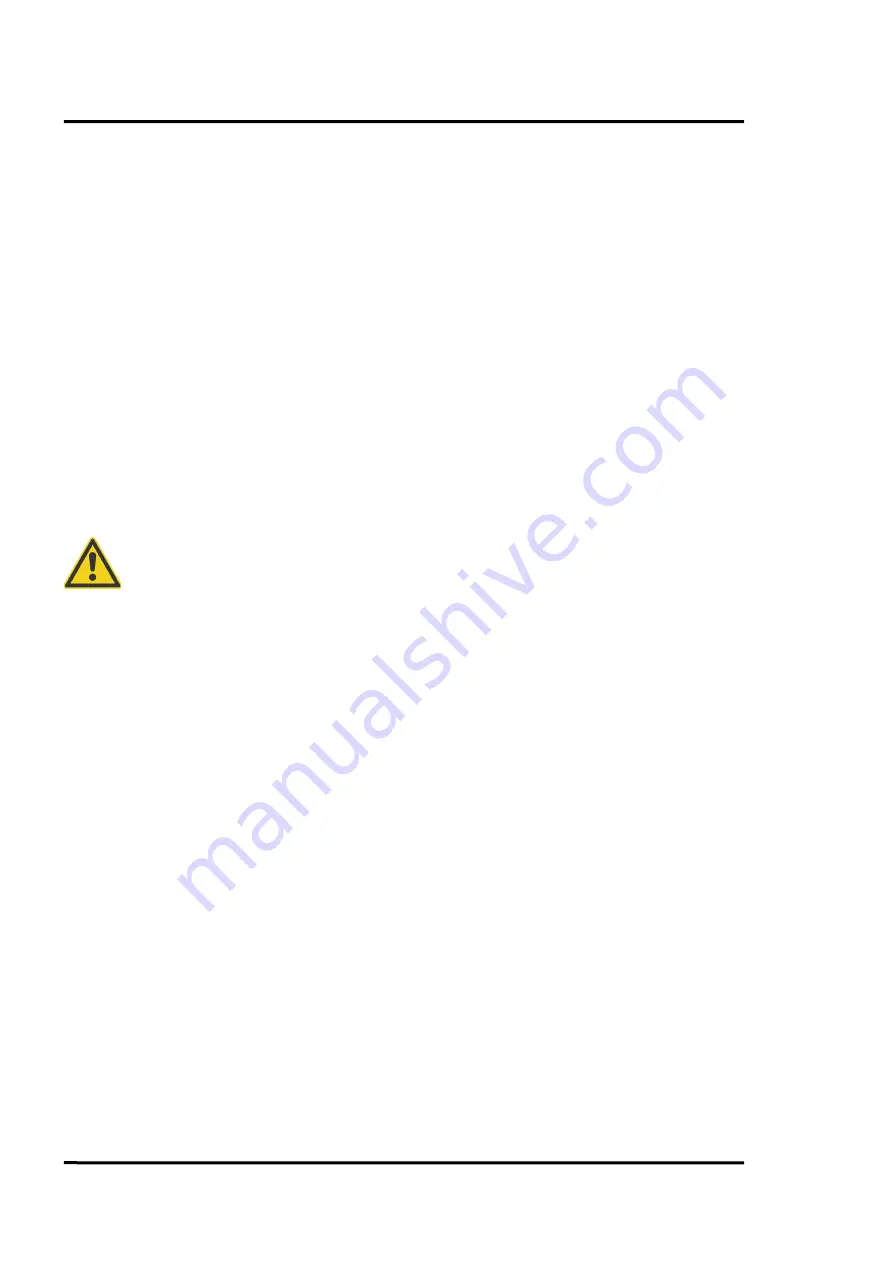
Installation
18
MP150
5
Installation
Linescanners are able to measure temperature values along a line through the use of a rotating mirror.
For 25% of its revolution, the linescanner scans the field of view (FOV). This corresponds to a scan
angle of 90°. The remaining 75% of its revolution is used for the internal operation of the sensor. The
rotating mirror views the scene and reflects the infrared energy striking it onto a system of lenses
which focuses the radiation onto a thermoelectrically cooled detector. The incoming signal is scanned,
digitized, and then converted to temperature values by the internal microprocessor. For every
revolution of the mirror, up to 1024 measured values will be internally collected. An air purge system
keeps the scanner’s window free of dust, debris, and condensation.
5.1
Ambient Temperatures
Without water cooling, the linescanner is designed for ambient operating temperatures between 0°C
and 50°C (32°F and 122°F). With water cooling, it can be used in environments of up to 180°C (356°F),
see section 5.9
, page 26. The internal temperature is the determining factor for proper
operation of the linescanner. It is displayed in the DataTemp software. The difference between the
external ambient temperature and the temperature inside the housing also depends on the thermal
contact of the linescanner and its mounting hardware.
The temperature inside the housing must be between 0°C to 60°C (32°F to 140°F) during
operation and never more then 65°C (150°F) at any time, including non-operation!
5.2
Environment
The linescanner complies with class IP65 and is therefore dust and splash resistant. The linescanner’s
window is made of a material that is resistant to thermal stresses and it is equipped with an integrated
air purge system which protects the window against contamination. Air supply for the air purge
should be oil free, clean “instrument“ air.
5.3
Electrical Interference
To minimize electrical or electromagnetic interference, follow these precautions:
•
Mount the sensor as far away as possible from possible sources of interference such as
motorized equipment producing large step load changes!
•
Ensure a fully insulated installation of the sensor (avoid ground loops!).
•
Make sure the shield wire in the sensor cable is earth grounded at one location!
•
To avoid potential differences use a single power circuit to power both the linescanner and the
PC running the software!
5.4
Geometry
The smallest possible object which can be measured depends on two conditions:
1.
The area measured must be no less than 90% (90% energy response).
2.
Hot spots must be clearly detected, when in front of a cold background (50% energy response).
Remark
:
The measured area for 50% energy response is approximately ⅓ of the area size of the
measured spot for 90% energy response.