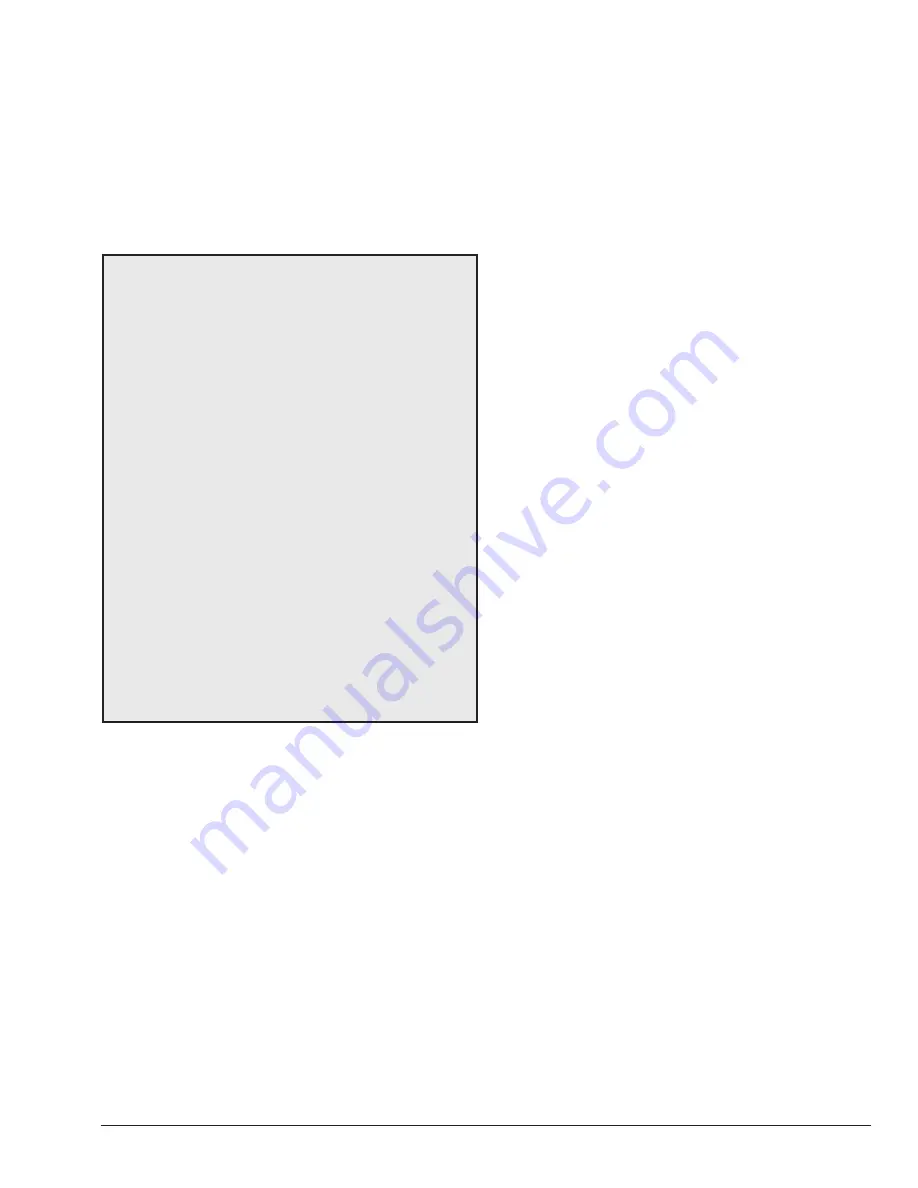
41
10. The PIM initiates a trial for ignition
(TFI)
counter to
the programmed number of trials for ignition (1 or
3)
and proceeds to Pump Purge mode.
11. The VERSA board will turn on the heater pump and/
or keep the Isolation Valve open, turn on the system,
and/or DHW pump as necessary to address the call-
for-heat. This is dependent on the Mode of operation
selected and the PIM DIP #3 position. The heater
will proceed through its pre-purge period before the
control will move into a Trial for Ignition.
Steps 12 and 13 are applicable if optional flow meter
is installed:
12. The PIM will only allow for ignition as long as the
flow meter detects a flow higher than the minimum
flow requirement for the unit. If minimum flow is not
achieved within 90 seconds, the unit will broadcast
a “Flow Error” condition and will hold from ignition
until proper flow is observed.
a. An alarm will notify the user that the unit did
not ignite due to insufficient flow.
b. If sufficient flow is present at the flow meter
and can be verified by the user, it is assumed
that the flow meter needs to be serviced.
Under this situation the user can override the
Flow Error and allow ignition and select an
allowable firing rate up to 80%. NOTE: Flow
Override will expire after 24 hours. Once time
has expired, the unit will cycle and alarm will
turn back on. If the unit cycles power within the
24-hour period, the Flow Override expiration
time will be reset.
13. If the flow meter detects flow equal to or higher
than the minimum flow requirement, then the unit
is allowed to proceed to the trial for ignition.
14. The PIM will only allow for ignition as long as the
flow meter detects a flow higher than the minimum
flow requirement for the unit. If minimum flow is not
achieved within 90 seconds, the unit will broadcast a
“Flow Error” condition and will hold from ignition until
proper flow is observed.
a. An alarm will notify the user that the unit did not
ignite due to insufficient flow.
b. If sufficient flow is present at the flow meter and
can be verified by the user, it is assumed that
the flow meter needs to be serviced. Under this
situation the user can override the Flow Error
and allow ignition and select an allowable firing
rate up to 80%. NOTE: Flow Override will expire
after 24 hours. Once time has expired, the unit
will cycle and alarm will turn back on. If the unit
cycles power within the 24-hour period, the Flow
Override expiration time will be reset.
15. If the flow meter detects flow equal to or higher
than the minimum flow requirement, then the unit is
allowed to proceed to the trial for ignition.
16. The VERSA board and PIM check the safety circuit
and will prevent a trial for ignition if any of the safety
devices are in an error/fault condition.
17. The blower is energized and set to pre-purge speed.
18. Once the blower speed is acknowledged as operating
at the prepurge speed by the tachometer output,
the blower proceeds to pre-purge for the specified
duration.
19. The secondary voltage level of the 24VAC supply
input is confirmed to be above 18VAC – if not, a Low
Voltage fault will be recorded and the heater will shut
off until the voltage rises above 18VAC consistently.
20. If all checks have passed, the system proceeds to
ignition.
21. The PIM re-initializes the ignition counter to the
configured number of trials (1 or 3).
22. The Hi Limit sensor is confirmed to read below the Hi
Limit setpoint.
23. The blower light-off RPM speed is verified.
24. The gas valve relay contacts are verified open – if
closed, a fault code will be issued and the heater will
post-purge and go into a hard lockout condition.
25. The XFiire heaters are equipped with direct spark
igniter (DSI).
:
a. The control turns on the DSI and the DSI proving
current is verified to be above the threshold value
(3.2A reference).
b. The configured heat-up delay takes place to allow
the DSI element to reach ignition temperature.
c. The gas valve output is energized for the trial for-
ignition time to light the burner.
d. The DSI is de-energized during the last second
of the trial-for-ignition period to sense for the
burner flame.
e. The flame sense is checked for successful
lighting of the burner. If a valid flame is detected,
the main gas valve, operating pumps and blower
relay remain energized and the PIM proceeds to
the Heating mode.
26. If flame is not detected during the trial-for-ignition
period, the gas valve output is disabled immediately
and the blower goes to a post-purge.
27. On single trial-for-ignition models, the PIM enters
ignition lockout and the LED on the PIM indicates the
fault code for ignition lockout. The VERSA IC Display
should also state Ignition Lockout. To reestablish
operation after the post purge has been completed
and clear the lockout error, press the reset button.
Содержание Xfiire 300B
Страница 54: ...54 6 WIRING DIAGRAM For a full size drawing visit www raypak com...
Страница 70: ...70 NOTES...
Страница 71: ...71 NOTES...