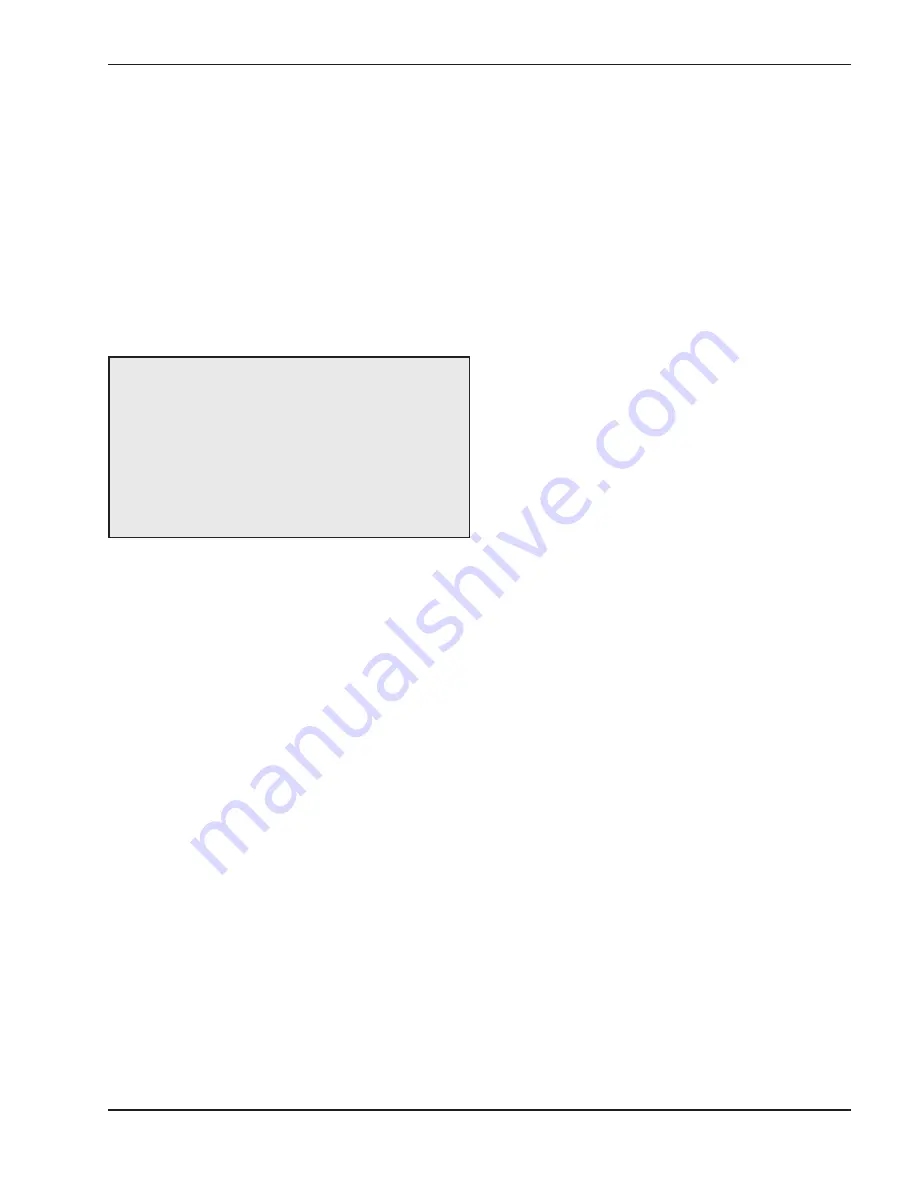
41
Control Settings
Boiler System (BOILER 1, 2, 3, 4)
These settings inform the control how many units are
part of a cascaded system. Each heater in the cas-
cade must have this setting adjusted to “ON” to be
recognized. In addition, DIP switch #2 on the MAS-
TER heater VERSA
®
Control Board must be set to
“ON” (Master) while the same DIP switch for the
remaining heaters must be set to “OFF”
(Follower/Slave). Connections between the additional
heaters must be made between the respective heater
PIM™ and the Master heater VERSA
®
Control Board
(see Wiring Connections on page 57 for details).
Outlet Max
The VERSA IC
®
control board uses this function in an
attempt to prevent an over-temperature condition from
occurring in hydronic systems. The Outlet Max value
will anticipate a rapid temperature increase and force
the system to modulate down before such an event
occurs. This setting has an adjustable range of 20 to
40
°F
above the Target value. The minimum value for
the resulting High Outlet Limit will always be 170
°F
,
regardless of the Target value. The resulting value
defines the high Outlet limit and the unit will start mod-
ulating 20
°F
below the high limit value.
Target Configuration (TARGET)
This setting is used to define if the control will operate
based on Outdoor Air Reset (RSET), setpoint control
(SETP), or an Energy Management System through
the ModBus communication protocol (MODB). The
default setting is SETP.
Mode Selection (MODE)
This MODE selection determines the operational char-
acteristics of the system. MODE = 1 relates to
hydronic heating or process heating applications.
Mode = 2 relates to conventional heating with an indi-
rect heating need located in the system loop piping.
Mode = 3 relates to conventional heating with an indi-
rect heating needs located within the boiler loop
piping. Refer to the Application diagrams and descrip-
tions on pages 9-21 for more details of how your spe-
cific system should be configured.
Setpoint Temperature (SETPOINT)
This is the target setpoint heater temperature when a
call-for-heat is present while operating in setpoint
operation. This value is only available to set/change
when the PIM™ identity is “H” and the TARGET =
SETP. The range of adjustments is from 50°F to the
maximum value programmed into the PIM™ for
instance XFyre 50 to 192°F, XPak-FT 50 to 192°F,
MVB / XTherm 50 to 220°F. The default value is
180°F.
Tank Setpoint (TANK SETP)
This is the set-point temperature for the storage tank.
It is only available to set/change when the PIM™ iden-
tity is “WH”. A range of 50 to 150°F is available with a
default of 125°F. For temperatures in excess of this
range, use an H model boiler configured in Mode 1 for
process application.
Pool Setpoint (POOL SETP)
This is the set-point temperature for the pool. This
value is only available to set/change when the PIM™
identity is “P”. A range of 50°F to 106°F is available
with a default of 80°F.
Pool Maximum Supply
(SUPPLY MAX)
This is the maximum supply temperature to the pool.
This value is only available to set/change when the
PIM™ identity is “P”. The heater will shut down if the
temperature exceeds this maximum value. The range
of adjustment is 110°F to 120°F.
Differential Settings
A heat source must be operated with a differential in
order to prevent short cycling. The heater differential is
divided around the heater target temperature.
1. Target Differential (TARGET DIFF)
This value is only available to set/change when
the PIM™ identity is “H” and the PIM™ DIP switch
#1 (Operator Differential) is set to ON (Manual
Differential). Target Differential is split equally
above and below the target set-point (SETPOINT).
For example, in the case of a 180°F set-point with
a 10°F differential, the control will energize the
boiler when the controlled temperature drops to
175°F and then will shut the boiler off at 185°F.
The Target Differential defaults to 10°F with a
range of 2°F to 42°F.
NOTE:
During service or if it is determined that a
heater should NOT be operational, this value can be
set to OFF to disable a heater so the system will not
use it or calculate it in the system operation. If the
MASTER unit needs to be powered off, the system
will allow functionality through the followers by using
limp-along mode. To allow proper functionality the
system pump and DHW pump (if applicable) must be
connected as depicted on figure 37 page 54.
Содержание VERSA IC
Страница 2: ...2 Rev 2 is a software revision J1214G Aug 2014 completely new edition of this manual...
Страница 28: ...28 Fig 26 WH Direct DHW single Heater with CWP VS Pump MIX TYPE 2 Fig 25 WH Direct DHW Single Heater...
Страница 78: ...78...
Страница 79: ...79...
Страница 80: ...80 www raypak com Raypak Inc 2151 Eastman Avenue Oxnard CA 93030 805 278 5300 Fax 805 278 9725 Litho in U S A...